The magnesium market could double in under a decade and one ASX-listed company is ready to make its move
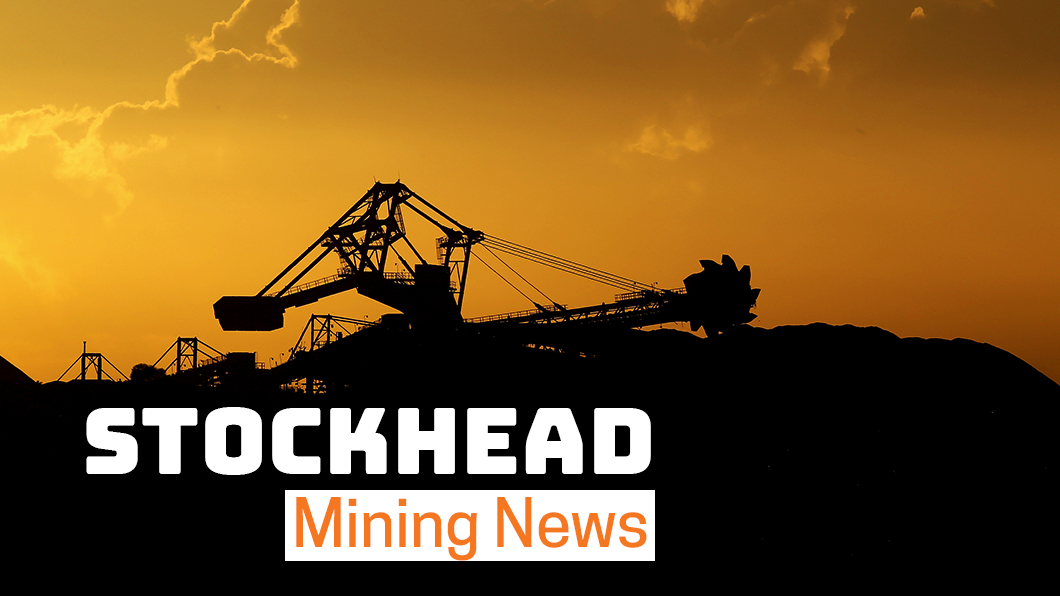
Pic: Bloomberg Creative / Bloomberg Creative Photos via Getty Images
Magnesium is the seventh most abundant element in the Earth’s crust, but the concentration of its supply chain in China has obscured it from the view of Australian investors.
Highly conductive and with the best strength to weight ratio among the world’s common structural metals, it is far more than just a remedy for Charley Horse.
Around one million tonnes of the metal is produced and sold every year, primarily for use in the desulphurisation of steel, aluminium for cans, the aerospace and automotive sectors in China.
Latrobe Magnesium (ASX:LMG) is the only equity on the ASX with exposure to magnesium.
CEO David Paterson said the operation, which is set to enter production in 2023, would be emerging at the right time and with the right process to take advantage of demand growth from the automotive sector.
“Traditionally we use magnesium about a third in steel desulphurization for your stainless and stronger steels, it takes out the sulphur and makes it harder,” Paterson said.
“The other third was in aluminium cans and that’s a mature market, then the other third was in a plethora of modern stuff.
“About 10 per cent die-casting.”
But its real growth story is in its emergence in recent years in lightweight aluminium sheet for panels in cars, a technological development that could leverage it to the growth of the Chinese automotive sector and, in particular, Electric Vehicles (EVs).
Latrobe Magnesium share price today:
Mag alloys getting bump from lightweight cars
“If you look in a vehicle it’s always been in the parts that take the heavy hits, so your engine mountings, your steering wheel, your steering wheel columns and also your seat braces,” Paterson said.
“What’s been the big change up in lightweighting cars has been in aluminum sheet; that came in around 2015-2016.
“To make aluminium sheet strong you need anywhere between 1-6% Mag alloy.
“Aluminium sheet is the saviour of the aluminium business because there was a lot of over-capacity in the aluminium business. You’re talking 65Mt a year of aluminium made in the world.
“If you’re talking a big chunk of that going into car panels, then you’ve got a big pick-up in your use of Mag.”
By 2027 the market for magnesium could double from 1Mtpa to 2Mtpa on vehicle production alone.
According to the latest Chinese 13-year plan, the volume of magnesium in a car will rise from an average of 8.6kg/car in 2017 to 45kg by 2030, with a compound annual growth rate in the market of 5%.
“We’re about 1Mt in the Mag market, that’s going to double off the back of aluminium sheet,” Paterson said. “Forget about any other use, it will just double off the back of that.”
While it is not regarded as a “battery metal” – yet – magnesium remains an incredibly crucial part of the passenger EV narrative because the lower the weight of the vehicle, the greater its range and efficiency.
“There hasn’t been a big push in it taking over from lithium batteries, but a big push in it going into electric vehicles because the most important part in an electric vehicle is the lightweight, it’s not the lithium battery,” Paterson said.
“The lithium battery is about 74kg of your weight and that’s what they’re trying to reduce all the time.”
Battery potential as well
While research is in its infancy, work is also under way to assess whether magnesium ion batteries could emerge as a cheaper, safer replacement for lithium ion.
That includes researchers from the University of Houston and Toyota Research Institute of North America, although there remain questions about their power performance.
“You’re talking two to three times the storage capacity and all of a sudden you’re getting out of that 150km range to 350-400km range,” Paterson said.
“One of the reasons why Toyota initially said in the States they would not get to the number of vehicles Obama wanted was because they just said you haven’t got the range, and everyone in the States gets on the freeway and drives for 10-12 hours.”
“You’ve got 2-3 times the storage capacity, there’s more of it, it’s cheaper than lithium in the marketplace and it’s recyclable.
“Aluminium sheet with mag in it, 100% recyclable. Lithium, when you make it, it’s a real problem child and you get some nasties, so it’s hard to recycle.”
Local made magnesium – A strategic aim
Australia had a go at developing a magnesium industry 20 years ago, when AMC raised hundreds of millions of dollars from investors and received backing from both Newmont Mining and the Howard Government.
That ended in tears when it placed the Stanwell project near Rockhampton in Queensland in mothballs before it got off the ground.
“There was a massive push back in Howard’s era, they spent a lot of money, and we were the last hopeful,” Paterson said.
“Magnesite I think is the seventh most abundant mineral in the Earth’s crust and we have magnesite up in Queensland.”
“There was a big failure back in 2000 when AMC blew about $1 billion of equity, heavily financed by the State and Federal Government.”
Paterson said it was impossible for local producers to compete on cost in the mainstream market with China on magnesium alone. It dominates the trade with around 85% of global supply.
“There is no supply in Australia, there is none currently in Canada with one to come, there is one supplier of 50,000t in the US, none in the EU and none in Japan,” he said.
“They’ve dominated it because of the requirement of the Mag in steel and aluminium, where they’re the biggest producers, and then magnesium in its own right because of the growth of their car business.”
“That’s an 80-90 million unit market worldwide. Cost-wise, it’s China, and new technologies haven’t really come through in the magnesium (mining) business.”
Process makes Latrobe Magnesium cost competitive
Rather than traditional magnesite mining and processing, Latrobe is using another method to extract the lightweight metal.
It will produce magnesium metal from fly ash at the Yallourn coal plant in Victoria via a patented hydrometallurgical process at a 3,000tpa demonstration plant.
By selling another five products – supplementary cementitious material (SCM), aglime, silica, char, and iron – Latrobe will also improve the payability of the operation.
“The reason we’re able to do it, and the other business out of Canada, is we’re using a different feedstock,” Paterson said.
“We’re using brown coal. Out of that 10% is mag. If we only got 10% of the metal out, we wouldn’t be able to compete.
“What we do get out is – depending on the type of fly ash – anywhere between an additional two products and up to five products.
“In Australia for every tonne of brown coal you burn you make around 2% fly ash.
“It’s very fine, it’s like a talcum powder but it’s black and it’s got a high iron oxide content.
“We pull out a high-grade hematite as well. We’re making saleable products out of it and that’s what makes us viable against China.”
Paterson says Latrobe’s process is also cleaner than traditional magnesium extraction, with CO2 emissions some 50% lower than Chinese producers.
“We make a product that is very low in CO2 emissions. China traditionally will make about 21t of CO2 per tonne of mag,” Paterson said.
“We’re down to about 10t of CO2 per tonne of mag, none in the cement and none in the other products.
“All of a sudden you’ve got a very saleable product because it’s low in emissions – that’s what everyone is looking for in the product.”
Latrobe eyeing 2023 production
Latrobe recently appointed Mincore as its engineering, procurement and construction management contractor for the Latrobe Valley project.
The company is aiming to release major tender packages for the 3,000tpa demonstration plant in January with a roughly 12-month construction period to follow.
That could see the demonstration plant – a precursor to a 40,000tpa commercial scale operation – up and running by early 2023.
Paterson said one of the benefits of the site was that it is fully permitted, and it has some 14,000m2 of buildings suitable for the initial demonstration plant.
The company currently has a grant application pending with the State government and expects to announce funding arrangements for the project in the coming quarter.
Related Topics
UNLOCK INSIGHTS
Discover the untold stories of emerging ASX stocks.
Daily news and expert analysis, it's free to subscribe.
By proceeding, you confirm you understand that we handle personal information in accordance with our Privacy Policy.