IperionX’s recycled titanium is a low carbon champion
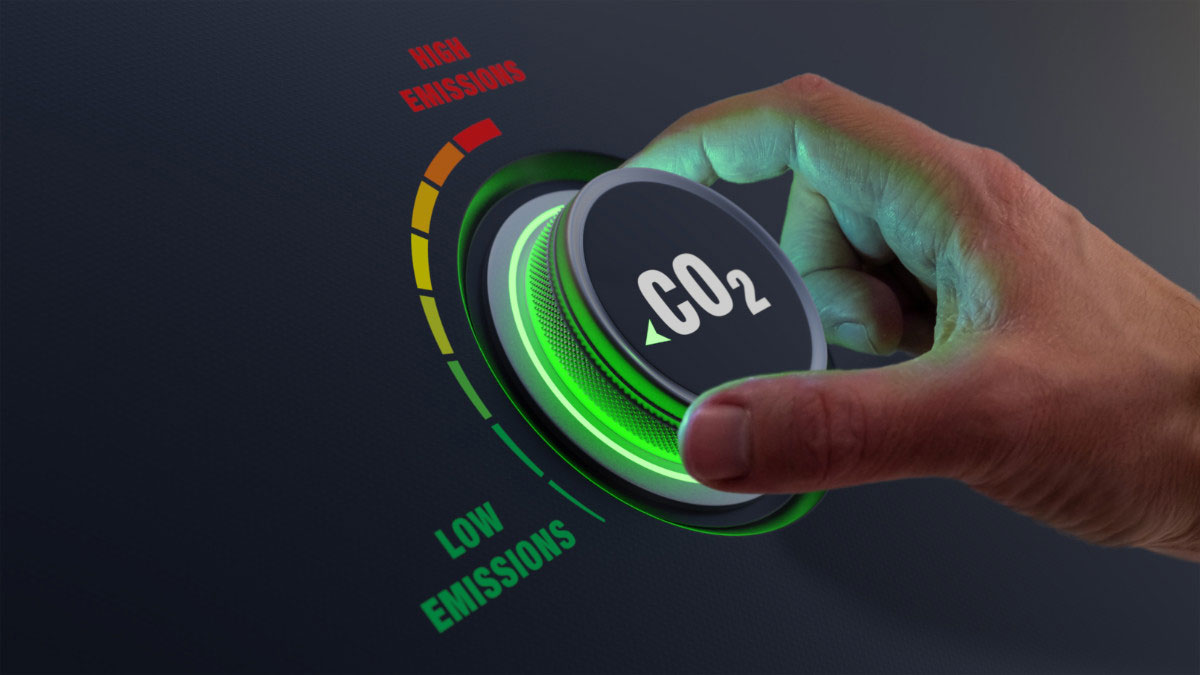
Dialling down the emissions with IperionX’s recycled titanium powder found to have a carbon footprint over 90% lower than existing products. Pic via Getty Images
The low carbon credentials of IperionX’s recycled titanium powder has received a shot in the arm after a study found that it has a carbon footprint more than 90% lower than traditional titanium powders.
The life cycle assessment (LCA) by EarthShift Global found that recycled titanium powders that are planned to be produced at the company’s planned Titanium Demonstration Facility in Virginia using its patented technology have the potential for a life cycle carbon footprint of just 7.8 kg of carbon dioxide equivalents (CO2e) per kilogram.
This is over 90% lower than traditional titanium powders produced via plasma atomisation, 80% lower than titanium ingot produced from the Kroll process, more than 50% lower than aluminum ingot and near equal to stainless steel.
Perfect timing
With IperionX (ASX:IPX) determined to re-shore a low cost and sustainable US titanium supply chain using its breakthrough technology, the LCA – the first known critically reviewed study of its type focused on titanium metal powder – couldn’t have come at a better time as consumers look to source low carbon, affordable titanium from traceable recycled sources.
It also represents a key step in validating the company’s patented titanium technologies, which provide the only commercially available fully circular, low-carbon titanium using 100% recycled titanium scrap as feedstock.
“This independent verification of the lowest quantified life cycle carbon footprint for titanium powders in the market today is an important milestone for IperionX and for our customers who want an affordable, low carbon and circular domestic titanium supply chain,” chief executive officer Anastasios Arima said.
Low carbon titanium
EarthShift Global director of analytical services Dr Nathan Ayer said the company had shown a commitment to using the results of the anticipatory life cycle analysis of their recycled titanium powder process to focus on ways to perform better on environmental metrics, especially related to climate change.
Titanium metal produced using the current Kroll process is high carbon, energy intensive, expensive and has low levels of circularity.
This has restricted the use of titanium despite its advantages in strength, weight and corrosion resistance.
IperionX’s technology seeks to address these flaws by significantly reducing the carbon footprint, reducing costs and allowing products to be recycled at the end of their life.
This article was developed in collaboration with IperionX, a Stockhead advertiser at the time of publishing.
This article does not constitute financial product advice. You should consider obtaining independent advice before making any financial decisions.
Related Topics
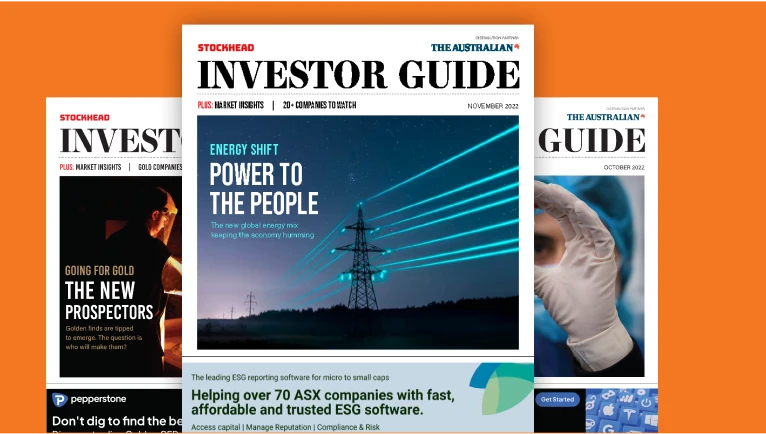
UNLOCK INSIGHTS
Discover the untold stories of emerging ASX stocks.
Daily news and expert analysis, it's free to subscribe.
By proceeding, you confirm you understand that we handle personal information in accordance with our Privacy Policy.