IperionX on track to be leading recycled titanium metal powder producer
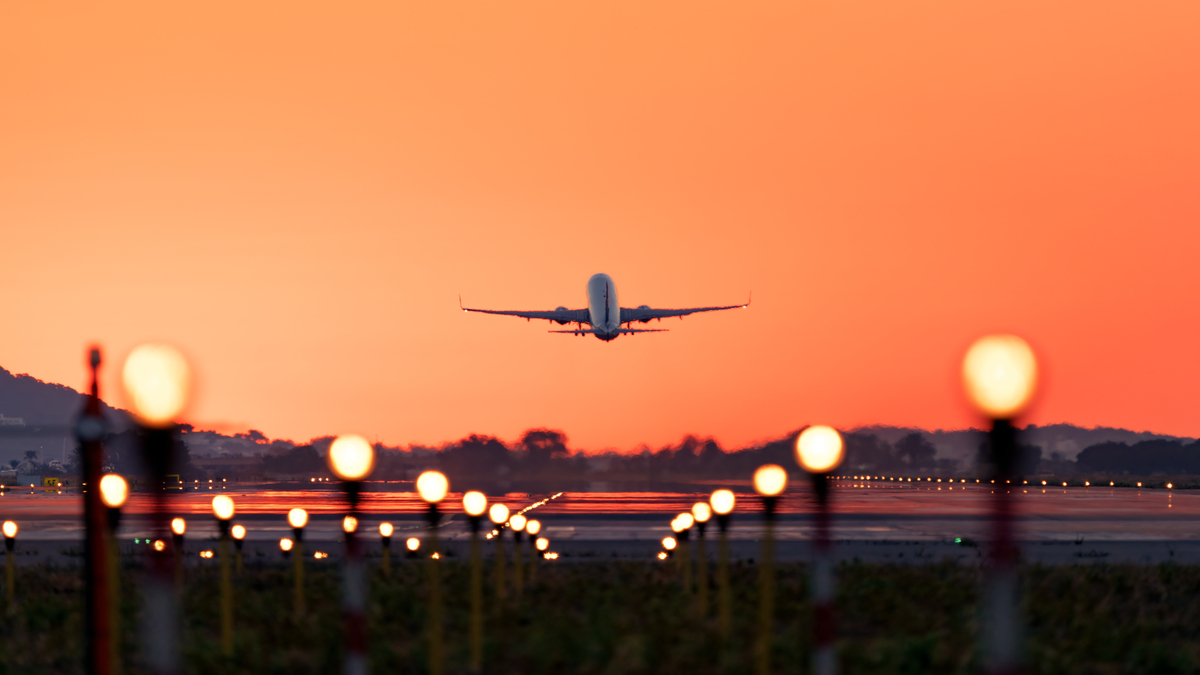
Picture: Getty Images
IperionX’s goal of becoming a leading producer of low-cost, low-carbon recycled titanium metal powder is another step closer to fruition.
Final engineering and design for its 125 tonne per annum Titanium Demonstration Facility (TDF) in Virgina, using its breakthrough Hydrogen Assisted Metallothermic Reduction (HAMR) technology, is nearing completion with first titanium powder production targeted for the first quarter of 2024.
More importantly for IperionX (ASX:IPX), there are defined plans for a simple modular expansion that will transform the TDF into the Titanium Commercial Facility (TCF-1) with production capacity of 1,125tpa in 2025.
This will not only be the largest producer of 100% recycled titanium metal powders in the world, it also provides a pathway for a step change in reducing the cost of titanium, with projected cash costs of about US$42/kg compared to a current third-party forecast titanium powder market price of approximately US$200/kg.
With this low cash cost, TCF-1 is forecast to generate EBITDA of about US$100m in 2026 based on key operating assumptions and using a conservative titanium metal powder price of US$130/kg.
Significant interest into the commercial supply of titanium powders has already been received by the company with advanced discussions underway with customers across various industries.
“We have now developed plans for the world’s first and largest recycled titanium powder facility, with initial production from the first stage 125tpa TDF forecast to come online in early 2024 with a simple and modular expansion to a 1,125tpa TCF-1 by the end of 2025,” chief executive officer Anastasia Arima said.
“The pathway for the development of the TDF and TCF-1 build upon the learnings from our current Industrial Pilot Facility operations in Utah where we have been producing circular titanium metal since early 2022.
“The development of the TDF & TCF-1 will scale our production to commercial quantities of 100% recycled titanium metal while also reducing the cost providing the potential for titanium to compete on price with other metals, including stainless steel and aluminium.”
He added that the company looked forward to rapidly advancing its developments through 2023 and moving towards scaled production of titanium powder to secure a US supply chain for the critical metal.
Low carbon credentials
The progress towards titanium powder production comes on the heels of a life-cycle assessment (LCA) by EarthShift Global which found that the company’s recycled titanium powder has a carbon footprint more than 90% lower than traditional titanium powders produced via plasma atomisation.
Its technology will also have 80% less carbon footprint compared to the high carbon, energy intensive and expensive Knoll process, which also has low levels of circularity.
This article was developed in collaboration with IperionX, a Stockhead advertiser at the time of publishing.
This article does not constitute financial product advice. You should consider obtaining independent advice before making any financial decisions.
Related Topics
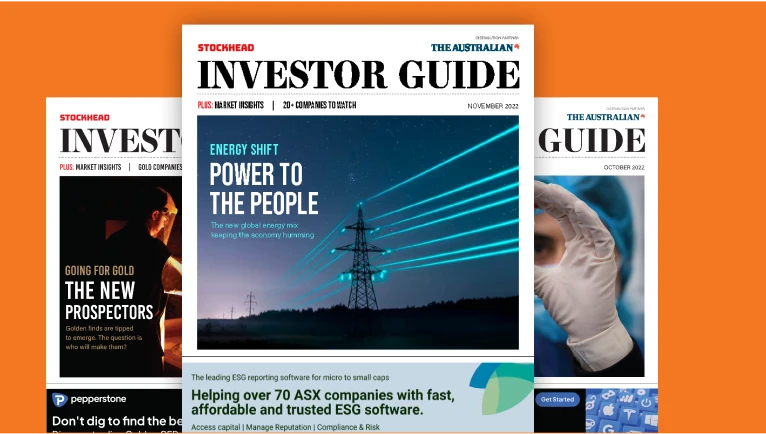
UNLOCK INSIGHTS
Discover the untold stories of emerging ASX stocks.
Daily news and expert analysis, it's free to subscribe.
By proceeding, you confirm you understand that we handle personal information in accordance with our Privacy Policy.