Confirmed: Magnetite’s iron ore is ‘very high quality’
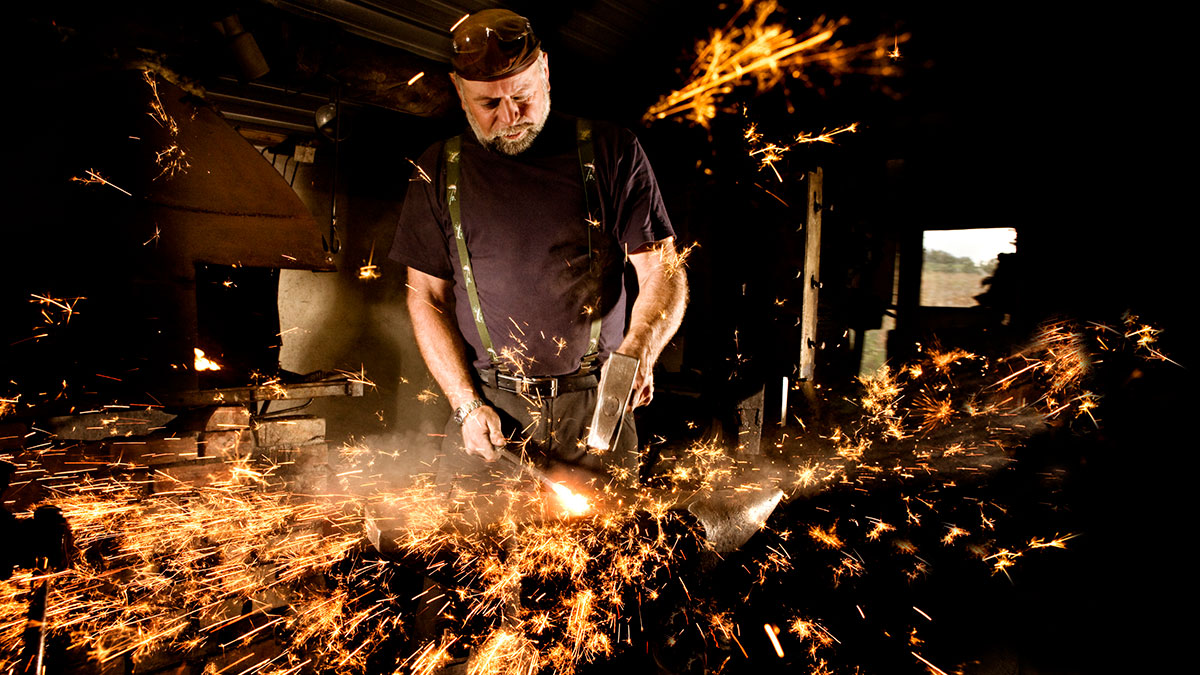
Things are heating up for Magnetite thanks to interim metallurgical testwork that’s confirmed the company’s on the right track for iron. Pic via Getty Images.
Magnetite has received a massive leg up after interim metallurgical testwork confirmed the ability of its flowsheet to produce a very high-quality iron ore concentrate.
The ability to produce concentrates exceeding the design specification of 67.5% iron and 4.5% silica+alumina – with one sample producing 69.7% iron and 2.5% silica+alumina – is hugely positive.
That all this is achieved with little waste is another tick in the testing to verify and establish metallurgical performance of the process flowsheet and plant design.
Magnetite Mines (ASX:MGT) has also identified the potential to produce Direct Reduction (DR) grade concentrates with flowsheet optimisation while comminution testwork has demonstrated that the ore body requires just low-medium crushing and grinding energy.
Additionally, testwork has identified Vertical Roller Mill (VRM) as an alternative method for low energy, fine grinding of ores which could feature as a low operating expenditure alternative in early-stage grinding.
The company will now start comprehensive testing to assess the suitability of Razorback ore to premium DR concentrates and further VRM bulk testing and analysis.
“We are very pleased with the results of the metallurgical testwork so far as the detailed work completed thus far validates the Razorback process flow sheet,” Chief Executive Officer Stephen Weir said.
“Confirmation of the orebody’s potential to produce DR grade concentrates is a particularly exciting development for Magnetite Mines as we look to match Razorback’s very long life with our customers’ future requirements as they decarbonise their steel production inputs.
“Coupled with the premium paid for DR grade concentrates and the low carbon ESG benefits of high-grade concentrates, Magnetite Mines looks forward to exploring the potential to produce DR grade concentrates.”
Test work to back iron production
The Definitive Feasibility Study metallurgical test work is designed to test all steps of the Hatch designed processing flowsheet.
It consists of crushing followed by dry HPGR and air classification processing for primary grinding. There is a rougher magnetic separation stage followed by ball milling and a rougher flotation circuit for a cleaning stage.
A final silica rich flotation concentrate is subject to fine grinding before cleaner magnetic separation with the magnetics reporting to final concentrate.
The flowsheet is conventional by modern standards and makes use of proven technologies currently installed in iron ore processing plants.
Magnetite expects the planned processing plant to receive 15.5 million tonnes per annum of ore feed to produce between 2.5Mtpa and 3Mtpa of high-grade concentrates.
Adding further interest, this plant represents a single stage of the mining production and has been designed as a replicable processing line, to be duplicated with mining expansion opportunities.
Upcoming work
Work to date represents a preliminary confirmation of the processing flowsheet.
In the coming months, the company expects to receive results from variable flotation, filtration, thickening and tailings product characterisation, and bulk flowsheet stimulation.
Magnetite is also testing the amenability of VRMs with respect to Razorback ores as an optimisation study running in tandem with the current DFS.
Results to date have indicated significant operational expenditure upside with low power utilisation and low wear rates while further testwork to test the lateral continuity of the project deposits is planned for August.
Additionally, a key outcome of the testwork is to confirm the ore body’s potential to produce DR grade concentrates, which are characterised by high grades of iron and low contents of gangue minerals and deleterious elements such as phosphorus and sulphur.
This product attracts premium pricing and significant demand from steelmakers for use in decarbonising steel mills.
Hatch has highlighted that the project concentrates produced during recent testwork indicated that DR grade concentrates were potentially achievable with additional flotation/hydroseparation and/or grinding to produce a separate DR product stream.
This potential will be explored through a suite of test work designed by Hatch process engineers.
This article was developed in collaboration with Magnetite Mines, a Stockhead advertiser at the time of publishing.
This article does not constitute financial product advice. You should consider obtaining independent advice before making any financial decisions.
Related Topics
UNLOCK INSIGHTS
Discover the untold stories of emerging ASX stocks.
Daily news and expert analysis, it's free to subscribe.
By proceeding, you confirm you understand that we handle personal information in accordance with our Privacy Policy.