Aussie made: ASX firms boosting local health & medical manufacturing
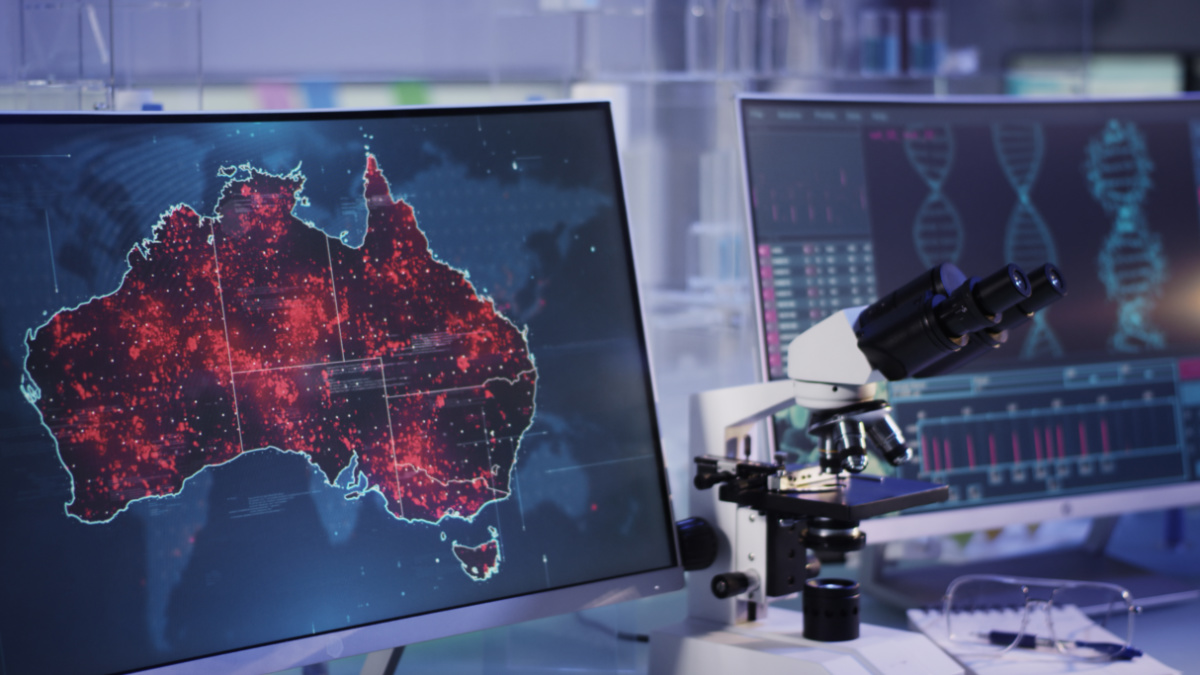
ASX health companies are proudly embracing Aussie made. Pic: Getty Images
- Several ASX healthcare companies are proudly manufacturing products in Australia
- Polynovo, Optiscan and Trajan Group all have manufacturing facilities in Melbourne
- Orthocell says government funding can boost manufacturing capabilities of Aussie biotechs
This is the third of a three-part special delving into the significant growth of Australia’s health and medical manufacturing industry and its current and future opportunities.
With moves to make Australia a global force in the manufacturing of health and medical products, leaders of ASX healthcare companies are embracing opportunities to be proudly Aussie made.
Large ASX companies such as CSL (ASX:CSL), Cochlear (ASX:COH) and ResMed (ASX:RMD) have manufacturing facilities in Australia. Here’s some more ASX healthcare companies we’ve noticed manufacturing products locally.
PolyNovo (ASX:PNV)
The wound care company, based on technology spun out of the CSIRO, is headquartered and has manufacturing facilities in Port Melbourne.
PNV specialises in development and commercialisation of dermal regenerative solutions with Novosorb BTM (biodegradable temporising matrix) used to close deep dermal wounds and aid the body in generating new tissue.
NovoSorb BTM is a synthetic polymer that does not contain any biologic materials, which the company says is important because traumatic wounds often contain bacteria that may cause infection.
NovoSorb MTX uses the tech platform underpinning the clinical success of BTM without a sealing membrane. The company’s products are sold in 39 countries, backed by a large body of clinical evidence, and have treated more than 50,000 patients.
CFO Jan Gielen told Stockhead PNV’s implantable dermal scaffold products fall under a class three medical device subject to stringent regulation, so the manufacturing process is crucial.
“Quality is critical due to being an implantable medical device and the stringent requirements from regulatory bodies.”
Gielen says PNV started off with a modest lab and manufacturing facility back ~2015 before buying the building next door to expand.
“Then another building next door, which was the same size as the two combined, came up for lease about a year and a half ago,” he says.
Gielen says, PNV is now building a brand new manufacturing facility which will add another half a billion in annual revenue in terms of capacity to the existing $180m it can get out of their current two facilities.
Assisted by a $2 million Victorian Government grant, PNV is expanding its R&D facilities, developing a pipeline of new medical devices, including products for the treatment of hernia.
He says gross margins are high, with raw materials and a simple manufacturing process combining to make their product cost-effective.
“The costs are in the overheads so the more we make, the lower the cost per unit, and the more efficient we become,” Gielen says.
Gielen says the value for a medtech company is often the “trade secrets” of its manufacturing as much as patents.
“We may eventually build another facility in the northern hemisphere, maybe the US, but once the new facility in Port Melbourne is complete that will add half of billion in terms of revenue capacity here, so it’s a while off,” he says.
“For now, it’s good to be able to keep the trade secrets close regarding how we go about manufacturing and focus on quality systems, optimising processes and getting that right.”
Optiscan (ASX:OIL)
OIL, is a global leader in developing, manufacturing, and commercialising confocal endomicroscopy imaging technologies for medical, translational, and pre-clinical applications.
The company’s technology, known as optical biopsy, generates real-time microscopic images, potentially eliminating the need for physical biopsies.
CEO and managing director Dr Camile Farah told Stockhead all OIL’s R&D and its products manufacturing is conducted at its headquarters in Mulgrave, Melbourne.
“We build all our devices on site at our Melbourne facility,” he said.
“This includes everything from the optical sub-assemblies that form the major component of our imaging probes, to the imaging towers themselves.
“We have many suppliers for the various parts that go into our devices – all being said that’s about 150 individual pieces required for the multi-stage build.”
OIL has three products currently on the market including ViewnVivo, which it sells to research institutions, universities and big pharma.
“It’s for anyone using living imaging for animal research or live imaging for cell culture research where they need a very small miniaturised microscope to enter the animal,” Farah says.
“Drug companies use our technology to monitor progress of their drugs when injected into animal models of cancer for example.”
The company’s second device is its intra-oral digital microscope InVivage, designed for oral cancer and pathology imaging in a dental surgery or hospital.
In June OIL unveiled its third microscopic medical imaging device InVue, which is designed to enable precision surgery by putting real-time digital pathology access directly into the hands of surgeons.
The company also has several other imaging devices and platforms under development. In May, OIL announced it had inked a know-how agreement with the world-renowned Mayo Clinic in the US to develop a digital confocal laser endomicroscopic imaging system for use in robotic surgery.
“All of that manufacturing and R&D will be done in Melbourne,” Farah says.
Farah says OIL has several reasons for maintaining manufacturing in Australia.
“We’re a spinout from Monash University so our R&D focus has been very strong and all of the know how is within our company,” he says.
“We’ve tried to outsource some things along the way but its very technically challenging to do and you need a lot of the insights and skills to manufacture and assemble our products.
“We have plans to expand our manufacturing and have taken up more space on premises so we can grow and are going to take on more staff as we scale up. We want to control the quality of what is high-precision technology.”
Furthermore, Farah says the Victorian and Australian Governments have been very supportive of manufacturing in the medical technology space.
In February, OIL announced it had received a $3m Cooperative Research Centres Projects (CRC-P) grant to work on its Edge-AI-enabled gastrointestinal endomicroscope from the Federal government.
Have a listen to our Vital Signs podcast with OIL
Orthocell (ASX:OCC)
The regenerative medicine company is focused on advancing tissue regeneration and repair with a manufacturing facility based at its headquarters on the grounds of Murdoch University in Perth.
OCC’s Striate+ is a collagen barrier membrane used to support guided bone and tissue regeneration in dental implant procedures.
It is distributed globally by one of the largest global dental implant companies, BioHorizons Implant Systems Inc.
Remplir is a collagen wrap used to augment nerve repair surgery and is approved for sale in Australia and New Zealand.
Regulatory approval for Remplir in Singapore is forecast for within six months and US FDA approval within nine months.
Managing director Paul Anderson told Stockhead OCC received a discretionary grant of $250,000 from the Western Australian government in the early days of the company in 2008 and put to work in 2009.
“That discretionary grant was used to leverage up with other money and build our world-class clean room facility which enabled us to build prototypes, conduct clinical studies at the very highest level and undertake early commercialisation work,” he says.
“We were able to translate these fantastic concepts that we had developed into products, procedures and practices that are now being used the globe.
“From a very small grant enabling us to build the facility we now have more than 120 patents delivered across the world and products approved in Europe, the US, Canada, Australia, New Zealand and Singapore.”
He says the company continues to grow its manufacturing capability, in turn creating more jobs.
“We have 45 people and are looking to employ more and the people we’ve employed predominantly around manufacturing involve quality assurance, quality control, manufacturing production, regulatory affairs,” Anderson said.
“We’re increasing the educational process with our staff and others about what is involved in translating technologies into a marketplace.
“I have been trying to champion this ecosystem and the benefits of small investments from grants and support from governments, which can turn into large things.”
EZZ Life Science (ASX:EZZ)
EZZ has a focus on genomic research and development to address four key human health challenges including genetic longevity, human papillomavirus (HPV), children’s care, and weight management.
The company has a strong omni channel distribution network across Australia, New Zealand, China and worldwide for its range of products, including health supplements, probiotics and skin care.
Former COO and CEO of Ausbiotech and EZZ chairman Glenn Cross says all of its products are manufactured in Australia or New Zealand.
“All our products are manufactured under good manufacturing practice (cGMP) principles,” he says.
“Wherever its relevant all our products are registered with the TGA and now we’ve gone into the US and they have recognised the capability of the our manufacturing.”
EZZ recently announced the US Food and Drug Administration had approved nine of its products in the food category.
“One of our primary selling points, especially into China and Asia, is that our products are manufactured in Australia or New Zealand under good manufacturing practice and are registered with the relevant authorities in countries as appropriate, which gives people a sense of comfort,” Cross says.
Trajan Group (ASX:TRJ)
TRJ is an Australian headquartered, global developer and manufacturer of life sciences products and devices used in the analysis of biological, food, water, and other environmental samples.
The company was established in October 2011 by CEO Stephen Tomisich and his wife Angela, who both have applied science backgrounds and decided around the kitchen table to acquire their first pathology consumables businesses.
“With more than a 600-strong workforce, we have a global infrastructure with R&D, manufacturing and distribution operations spanning four major continents – US, Australia, Asia and Europe – designed to support future growth at scale and in close proximity to key customers,” Tomisich told Stockhead.
He says one of TRJ’s core capabilities is our capacity to collaborate with academic and research institutions and industry leaders globally to deliver on the next generation of technologies.
“From our global headquarters and manufacturing facility in Ringwood, Melbourne, Trajan produces a range of laboratory consumables, focusing on glass technologies for chromatography such as analytical syringes,” Tomisich said.
“We use automation technologies in a very targeted and selective manner to ensure repeatable, high-precision products are always delivered to our customers in the pharmaceutical, clinical, environmental and food sectors.”
READ Part One: Australia’s medical manufacturing sector – a global success story in the making
And Part Two: ‘Huge economic potential’ – Moves to make Australia shine as a medical manufacturer
At Stockhead, we tell it like it is. While Orthocell, EZZ and Optiscan are Stockhead advertisers, the companies did not sponsor this article.
Related Topics
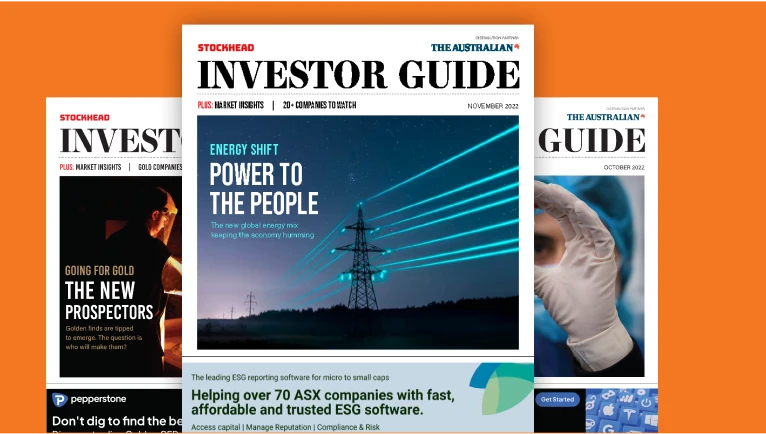
UNLOCK INSIGHTS
Discover the untold stories of emerging ASX stocks.
Daily news and expert analysis, it's free to subscribe.
By proceeding, you confirm you understand that we handle personal information in accordance with our Privacy Policy.