Sweden’s H2 Green Steel plant is $4bn green giant fuelled by hydrogen

Sweden is host to a new fossil-free green steel plant. Image: Getty
- H2 Green Steel plant to start production in 2024 using energy from green hydrogen instead of coal
- ‘The next step is to build vehicles from high-quality fossil-free steel’ – Swedish truck company Scania
- Australian companies including Fortescue Metals Group, Iron Road and Australian Vanadium have green steel projects
Decarbonised steel production is becoming a reality in Sweden where H2 Green Steel is building a €2.5bn ($3.9bn) hydrogen powered steel plant that is set to start up in 2024.
H2 Green Steel‘s plant in northern Sweden is to supply European end users with steel produced without fossil fuels and is billed as the world’s largest green hydrogen plant.
Explaining its green steel initiative, the company said demand for fossil fuel-free steel is rising substantially in sectors such as automotive, white goods and furniture.
“We want to accelerate the transformation of the European steel industry,” H2 Green Steel chairman, Carl-Erik Lagercrantz, said.
Steel production accounts for one-quarter of Europe’s industrial carbon dioxide emissions, and more than the total emissions from Denmark, Norway and Sweden.
“Electrification was the first step in reducing carbon dioxide emissions from the transportation industry. The next step is to build vehicles from high-quality fossil-free steel,” he said.
Plant to cost €2.5bn ($3.9bn)
The company said awareness was increasing about the impact of climate change and the need to improve the sustainability of high impact industries such as steel production.
The Sweden-based company includes Spotify founder Daniel Ek among its backers and is headed by Scania chief executive, Henrik Henriksson.
Henriksson said H2 Green Steel will accelerate existing rapid change in the steel industry, and “make Swedish steel world famous, not only for its quality, but also as the world’s greenest steel”.
Funding for the plant is estimated at €2.5bn and will be raised from a combination of equity capital and green project financing, and investment banks Morgan Stanley, Societie Generale and KfW IPEX Bank are financial advisers to the project.
Equity financing of €50m has been raised from a group of investors for the H2 Green Steel plant, including Scania, and it has close links with battery company Northvolt.
“A Scania truck weighs about six tonnes and five of those are steel, which today unfortunately is produced with a substantial carbon footprint,” said Scania executive vice president and head of purchasing, Anders Williamson.
“By investing in and partnering with H2 Green Steel we are now further accelerating the journey towards emission-free products across the whole value chain,” he said.
Production target of 5 million tonnes per year
A production target of 5 million tonnes per year for steel by 2030 has been set for the H2 Green Steel plant which will be powered by a 800MW hydrogen plant.
The plant will initially produce 2.5 million tonnes of steel per year by 2026, and then expand to 5 million tonnes per year by 2030.
Conventional steel production uses coking coal to heat iron ore and other steelmaking ingredients in a blast furnace and produces significant carbon emissions in the process.
According to H2 Green Steel’s company presentation, conventional steelmaking using coking coal produces ~2 tonnes of carbon dioxide for each tonne of steel.
Steel production from green hydrogen is a much cleaner process without any carbon dioxide or other greenhouse gas emissions that come with coking coal.
Instead of producing steel in a blast furnace, green steel is made in an electric arc furnace in a process that produces less than 0.1 tonne of carbon dioxide for 1 tonne of steel.
Green hydrogen employs electrolysis to split water into its two elements of hydrogen and oxygen and the electrolysis process can be powered from low-emission sources like solar.
Another investor in H2 Green Steel is investment firm Vargas which has a large shareholding in Sweden-based battery company Northvolt.
“As chief executive of Scania, Henrik has been one of the most visionary and active leaders for the business community in leading action on climate change and making progress toward a world without fossil emissions,” chairman of Vargas, Harald Mix, said.
Australian Fortescue Future Industries to study hydrogen
Several Australian firms have early stage projects for producing green steel or iron ore products such as pellets from hydrogen produced from fossil-free sources like solar.
These include the Andrew Forrest-led Fortescue Metals Group (ASX:FMG) which last month took a significant step forward in its green steel strategy.
The iron ore company has set up its Australian Fortescue Future Industries (AFFI) group, and appointed former Prime Minister Malcolm Turnbull to head the organisation.
AFFI’s task is to identify renewable energy and green hydrogen projects for development both in Australia and globally using Fortescue Metal Group’s expertise in this area.
Fortescue Metals Group has a stated policy target of achieving net zero carbon emissions from its operations by 2040, effectively decarbonising its iron ore production.
The iron ore producer announced in November a study to build a green ammonia plant in Tasmania’s Bell Bay, a location for aluminium smelting.
The company’s vision is for a 250MW plant to produce 250,000 tonnes per year of green hydrogen for domestic use and international export.
An investment decision on the plan is expected sometime in 2021.
Other green hydrogen projects being studied by the company include a refuelling facility for passenger vehicles at its Christmas Creek iron ore mine in WA.
Green iron ore pellet production in South Australia
ASX company Iron Road (ASX:IRD) has a project for green hydrogen to produce iron ore pellets at a new production facility at South Australia’s Cape Hardy port.
The project could serve as a prototype for green hydrogen projects in Australia’s iron ore sector as it hopefully moves from the drawing board and into reality over the next few years.
Hydrogen Utility (H2U), a developer of green hydrogen projects in Australia, is a partner in the project, as is Japanese engineering and technology company Mitsubishi Heavy Industries.
The company’s chief executive Larry Ingle told Stockhead about the project and the reasons underlying Iron Road’s investment in green hydrogen.
Meanwhile, Australian Vanadium (ASX:AVL) is seeking to use green hydrogen produced from renewable energy sources to reduce emissions at its eponymous project in WA.
As vanadium ore is extracted from the project it is subject to a process called a reductive roast – roasting it in the absence of oxygen – to create a pig iron product.
ASX share prices of Australian Vanadium (ASX:AVL), Fortescue Metals Group (ASX:FMG), Iron Road (ASX:IRD)
Related Topics
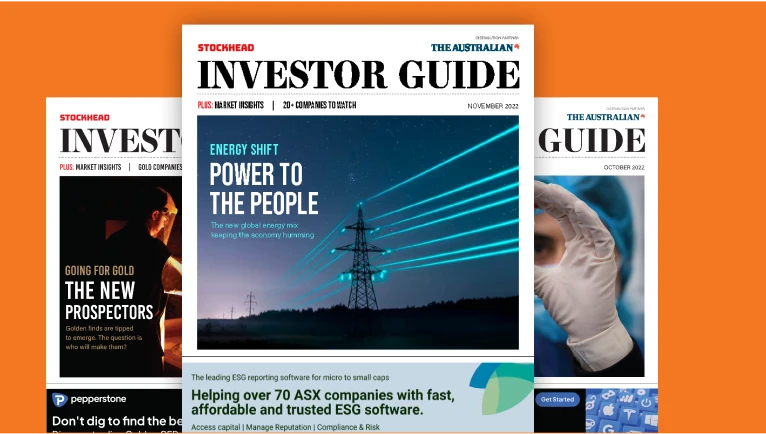
UNLOCK INSIGHTS
Discover the untold stories of emerging ASX stocks.
Daily news and expert analysis, it's free to subscribe.
By proceeding, you confirm you understand that we handle personal information in accordance with our Privacy Policy.