Battery Day: Tesla confirms nickel as metal of choice
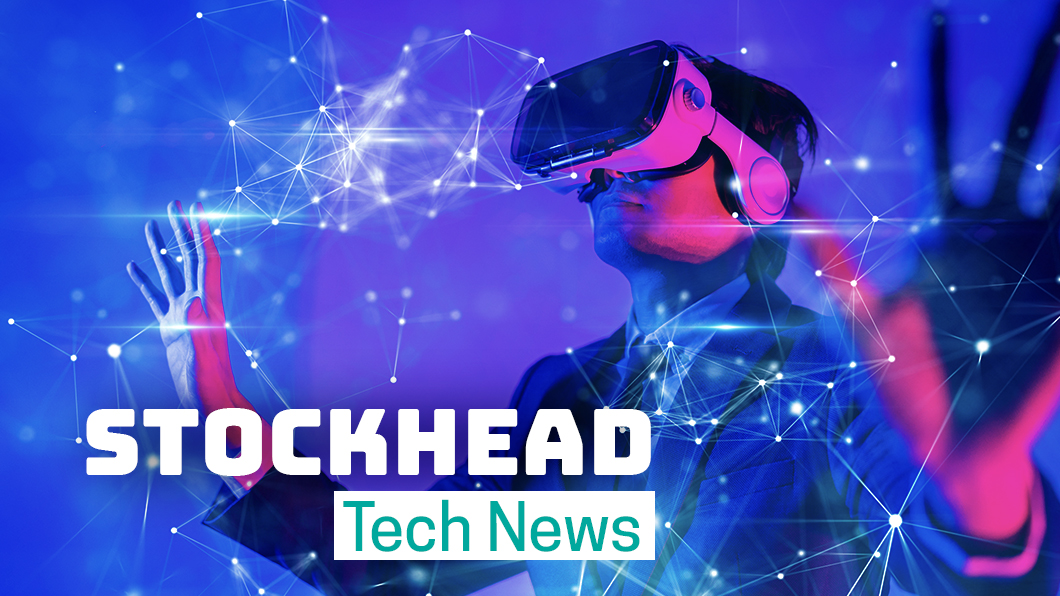
Pic: Thinkhubstudio / iStock / Getty Images Plus via Getty Images
- Tesla to increase nickel usage in EV batteries, and use less cobalt
- ‘We need to make more affordable cars… but we need to get the cost of batteries down’
- Lithium ASX stocks guide
Tesla’s widely anticipated Battery Day event went ahead Tuesday US time with several important announcements around Tesla’s choice of metal for its EV batteries.
The EV maker intends to use more US-sourced nickel in its cathode battery production and less cobalt.
“Nickel is the cheapest and the highest energy density metal,” Drew Baglino, senior vice-president for Tesla’s Powertrain and Energy Engineering division, told the crowd that had gathered in Teslas drive-in style for the Battery Day event.
“That’s why increasing nickel is a goal of ours,” he said.
Cobalt is also used in Tesla batteries because it provides a relatively stable structure for cathodes and has a good longevity, but Tesla wants to use less of this metal.
Tesla has been working on a high nickel cathode battery that has zero cobalt content.
By using nickel Tesla can get a 15 per cent reduction in the cost of its battery cathodes on a US dollar per kilowatt hour basis.
“In order to scale [production], we need to ensure we are not constrained by total nickel availability,” said Elon Musk, founder and chief executive of Tesla.
He told shareholders at the Battery Day event he had spoken to leaders of some of the largest nickel miners and asked them to increase their nickel output, and thought they would respond to his call.
Multi-tiered approach to Tesla battery production
Tesla will take a three-tiered approach to battery development starting with iron-based batteries for long-life cycle cathodes for stationary storage and where energy density is not paramount.
Then nickel-manganese for medium-life batteries, and high nickel for long-range vehicles like Tesla’s EV Cybertruck.
“It is relatively straightforward to do a cathode that is two-thirds nickel and one-third manganese, which would then allow us to make 50 per cent more cell volume with the same amount of nickel,” said Musk.
“Nickel is 50 to 60 per cent better than iron [for batteries],” said Musk.
Tesla to streamline battery production costs
Tesla is planning to steam-line its nickel production process and is targeting cost reductions in its cathode battery production.
Battery processing and production account for 35 per cent of Tesla’s battery production costs.
The remaining 65 per cent cost of Tesla’s battery cathode production expense is down to metal costs, namely, 35 per cent nickel, 25 per cent lithium, and 5 per cent cobalt.
“We have looked at the entire value chain and said, ‘how can we make this as simple as possible’,” said Musk.
The existing production process for nickel sulphate was “insanely complicated”, said Musk.
The company plans to use raw nickel powder, some of it from recycling, instead of using intermediate battery-grade nickel in metal sulphate form.
“We can eliminate billions in battery-grade nickel intermediate production, it is not needed at all, and we can also use that same process to directly consume nickel powder from recycling EV and electric grid batteries,” said Baglino.
Tesla’s new nickel cathode production process will reduce its investment costs by 66 per cent and process costs by 76 per cent.
The company will build its own cathode production facility in North America to process raw material nickel mined in the US, and the same goes for Tesla’s lithium production.
“There is enough lithium in the US to convert the entire US fleet to electric, all the 300 million cars in the US, using only lithium discovered in the US,” said Musk.
Tesla’s lithium battery content to be sourced in US
Tesla is also to pioneer a sulphate-free process for lithium used in its batteries, that extracts lithium using sodium chloride.
Musk said that moving into the business of nickel cathode production was a necessity for Tesla.
“We do see the fundamental constraint as total cell production, and that is why we are putting so much effort into making cells and trying to reinvent every aspect of total cell production from mining the ore to a complete battery pack,” he said.
“We are not getting in the cell business for the hell of it, but because it is the limiting factor for rapid growth,” he said.
The EV company produces battery cells for its four vehicle models at its factory in Nevada.
Battery cost critical to EV affordability
The EV company is planning to build an affordable mass market car with a sales tag of around $US25,000 ($35,000), according to reports.
“We need to make more affordable cars,” said Musk.
“One of the things that troubles me the most is that we don’t have an affordable car, but in order to do that we need to get the cost of batteries down,” said Musk.
Reports said that Tesla is working on a million-mile battery capable of powering an EV for that distance, but few details of this development were revealed at the Battery Day event.
EVs are still a relatively small proportion of the 2 billion vehicles in use around the world, Musk conceded.
“Less than 1 per cent of the total global fleet is electric. So there is a massive amount of work ahead to get new vehicle production to be sustainable,” he said.
Tesla’s Shanghai EV factory continues to scale up and has target production of more than 1 million vehicles per year.
Related Topics
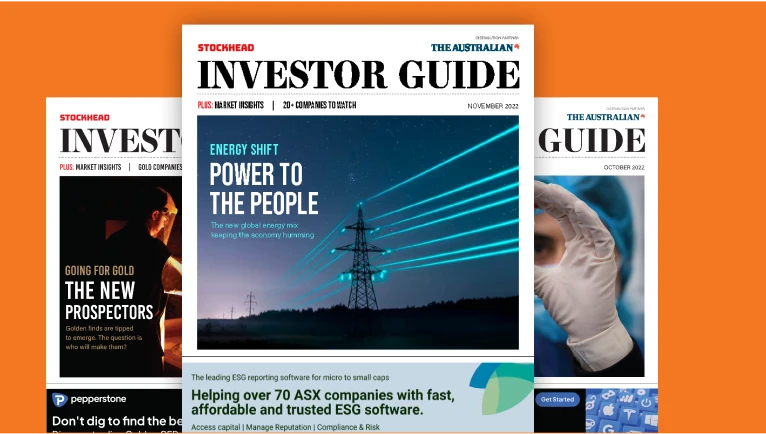
UNLOCK INSIGHTS
Discover the untold stories of emerging ASX stocks.
Daily news and expert analysis, it's free to subscribe.
By proceeding, you confirm you understand that we handle personal information in accordance with our Privacy Policy.