Alternatives to lithium-ion batteries are making their presence known
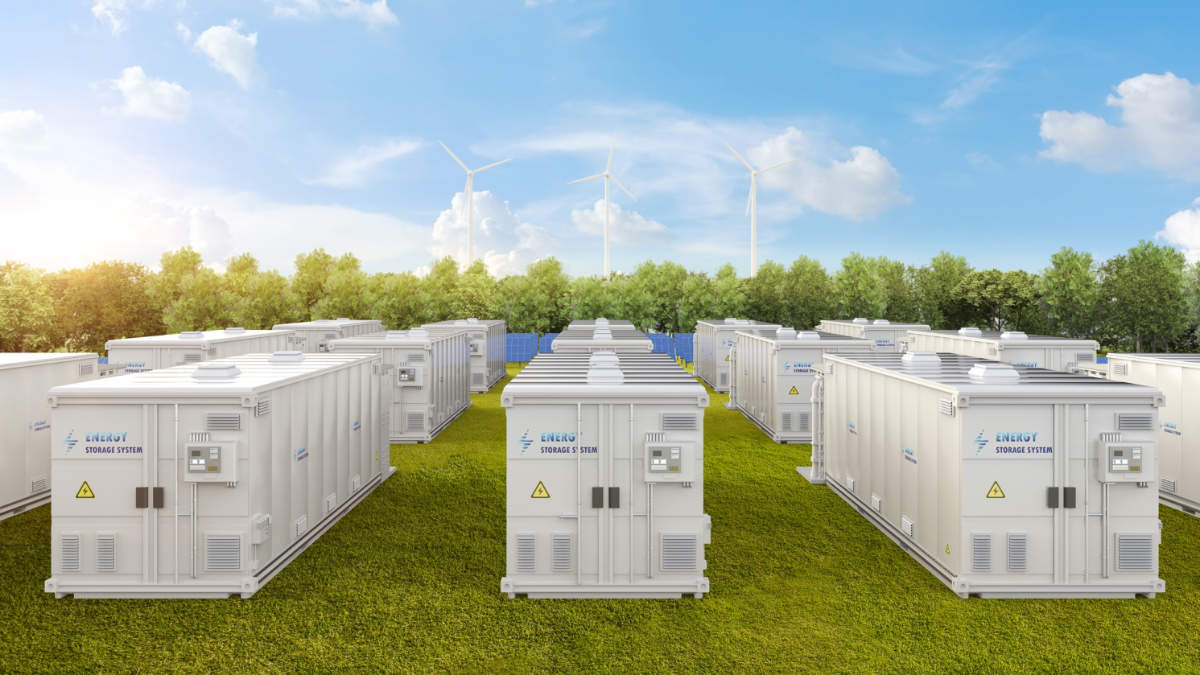
Alternative battery technologies are starting to make gains. Pic: Getty Images
Battery Tech 101 – your guide to the different battery technologies, who’s involved and what commodities are required.
Despite what reports might indicate – namely that demand for battery storage is dropping – the truth is that demand for batteries is still rising albeit at slower rates.
London-based Rho Motion noted in December 2024 that demand for lithium-ion batteries is still set to increase 26% year-on-year in 2024 compared to 2023.
It added that while the electric vehicle market continued to make up the bulk of demand, its growth rate had lagged behind the growth rate for stationary battery energy storage systems, which doubled from 7% in 2020 to 15% in 2024.
The International Energy Agency also flagged in its World Energy Outlook 2024 that the share of EVs in new car sales worldwide will rise from ~20% to 50% by 2030 in its Stated Policies Scenario.
Altech Batteries (ASX:ATC) chief financial officer Martin Stein concurred, noting that while there was a slow down in the speed of EVs being taken up, demand growth for industrial grid-storage or data-centre batteries was “growing, with some of the leaders of the big tech companies commenting that the bottleneck to AI implementation will not be computing power, rather it will be energy”.
What it all means is that demand for batteries remains robust and is set to keep rising and while lithium-ion batteries currently rule the roost, there are alternative technologies that might be better suited for specific applications.
Solid state sodium chloride batteries
We will start off out examination of alternative technologies with solid state sodium batteries, represented by Altech’s CERENERGY batteries, which uses plain old sodium chloride – common table salt – and nickel powder without the use of critical minerals such as lithium, copper, cobalt, graphite and manganese.
“I think as the world continues with achieving the renewable energy transition, having energy security in batteries that don’t use those raw materials will become more important,” Stein said.
And that’s not the only difference.
“Lithium-ion batteries use a liquid electrolyte and has a plastic separator sheet. These are organic materials and are what catches fire when li-ion batteries experience thermal runaway,” Stein said.
“What the industry is trying to do is move towards solid state technology which is replacing those flammable items with a ceramic electrolyte which is solid and then fires/explosions can’t happen.
“That’s what Altech has got, it has a solid-state technology.”
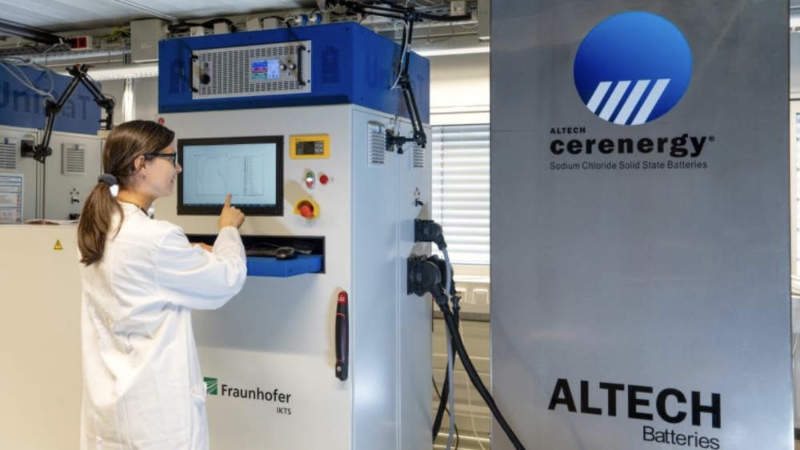
This combination makes Altech’s batteries safer, and gives them a longer lifespan and an operating temperature range from -40 degrees C to 60C.
While they are not suitable for use in EVs, which require very high power in a short period, CERENERGY batteries are targeted squarely at stationary applications such as grid storage or in data centres.
“We can also stack our batteries three high as we don’t have the fire issues lithium-ion batteries have that prevents them from stacking. This reduces our footprint,” Stein added.
Potential users of these batteries have already taken note with the company having secured three offtake agreements.
“One is with an industrial park, the other a utility provider in Germany and the last is with a company called Axsol, which provides services and goods to NATO,” Stein said.
“I’m pretty happy that we have a mix of potential customers there. It shows that there are many different industries and applications suitable to the CERENERGY battery.”
The first deal is with Germany’s Zweckverband Industriepark Schwarze Pumpe, which agreed to purchase 30 megawatt hours of energy storage capacity annually for the first five years of production.
Meanwhile, RefLau – a green hydrogen joint venture between European utility and energy companies Enertrag SE and Energiequelle GmbH – will purchase an initial 30MWh of CERENERGY energy storage capacity in the first year.
It will then buy 32MWh of energy storage capacity per annum for the next four years of production.
The final agreement is with NATO certified supplier Axsol – a leading, award-winning German provider of integrated renewable energy solutions – for the supply of 10MWh of energy storage capacity in the first year, rising to 30MWh in subsequent years.
For now, though, Stein says the company is focused on securing finance to construct its 120MWh battery plant in Germany.
“We are talking to banks, equity providers, grant and subsidy providers like the European Investment Bank to raise the €200m that we require to build the plant.”
Flow batteries
Another alternative to lithium-ion batteries for utility-scale battery energy storage system are vanadium redox flow batteries, which is a type of electrochemical cell that uses vanadium in the electrolyte solution.
They are considered to be safer, more scalable, and longer lasting than their lithium counterparts with a lifespan of more than 20 years, or up to 25,000 cycles.
While still lagging behind their more common counterparts, VRFBs are starting to see greater use with China’s Rongke Power completing in December 2024 a 175MW/700MWh system – the largest of its type in the world.
The battery system in the city of Wushi will provide grid forming, peak shaving, frequency regulation and renewable integration.
Rongke has also installed the previous largest 100MW/400MWh battery in Dalian.
Over in Australia, the WA Labor government made an election pledge to build a 50MW, 10 hour VRFB to support the grid around Kalgoorlie, which has suffered from blackouts in the past two years.
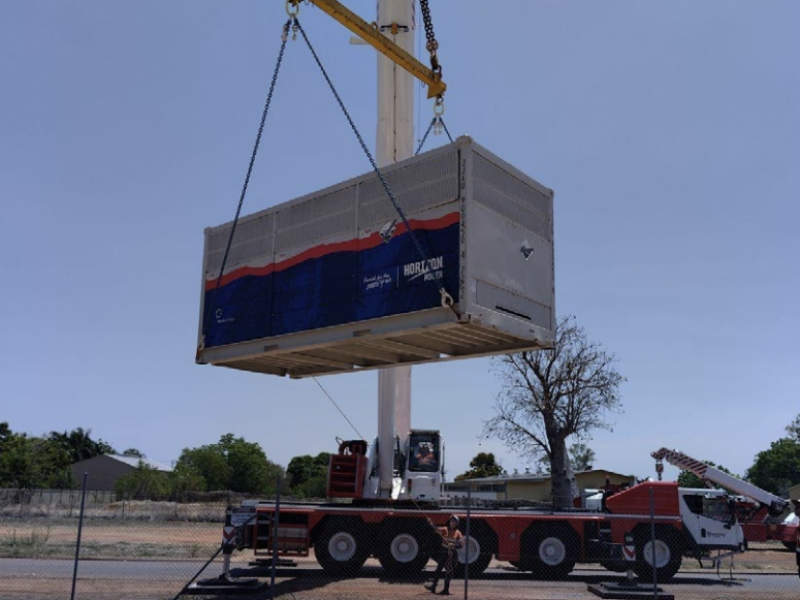
In November 2024, the state’s regional energy provider Horizon Power also started a 12-month trial of a 78 kW/220 kWh VRFB in Kununurra to determine whether it can solve technical challenges associated with establishing long-duration energy storage solutions in extreme environments.
This system was supplied by VSUN Energy, a wholly owned subsidiary of Australian Vanadium (ASX:AVL).
Besides its efforts to push for greater use of VRFBs, which is demonstrated by its progress on Project Lumina that seeks to develop a modular, scalable, turnkey, utility-scale BESS, AVL is also progressing its Gabanintha vanadium project to capture the raw material stage of the vanadium value chain.
There’s also the lesser known zinc-bromine flow batteries, although the future of this tech is in doubt as its Australian developer Redflow (ASX:RFX) is currently in administration due to an inability to secure financing.
Other alternatives
Another lithium-ion battery alternative includes lithium-sulphur batteries, which while still using lithium, replaces the use of critical minerals such as nickel, manganese and cobalt in the cathode with commonly available sulphur.
While they have yet to be commercialised, their similarity to lithium-ion batteries means that existing plants can easily swap over to producing lithium-sulphur batteries.
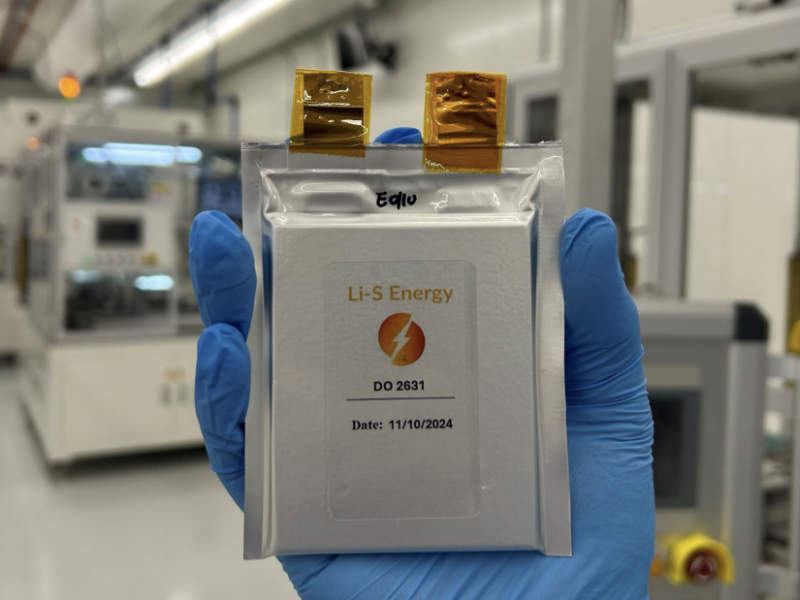
In Australia, Li-S Energy (ASX:LIS) is developing high energy density lithium-sulphur batteries and had in October 2024 successfully achieved 456Wh/kg after formation cycling in its semi-solid-state pouch cells produced at its Phase 3 automated production facility.
These cells, which offer substantial weight reductions, improving range, payload, and operational efficiency, are designed for high-growth sectors such as drones, defence, and electric aviation.
It has also tested its battery packs in successful drone test flights late last year.
Other technologies include solid state batteries that use a solid electrolyte made from ceramic, glass or solid polymer, along with iron-air and zinc batteries.
Solid state lithium batteries are more efficient, compact, longer-lasting and safer than lithium-ion batteries but have yet to be commercialised due to difficulties in scaling the technology up for wide-spread use.
Meanwhile, iron-air batteries are very affordable but have to contend with the issues of large size and slow recharge times.
At Stockhead, we tell it like it is. While Altech Batteries is a Stockhead advertiser, it did not sponsor this article.
Related Topics
UNLOCK INSIGHTS
Discover the untold stories of emerging ASX stocks.
Daily news and expert analysis, it's free to subscribe.
By proceeding, you confirm you understand that we handle personal information in accordance with our Privacy Policy.