Altech manufactures all cells for first of two 60kWh salt battery prototypes
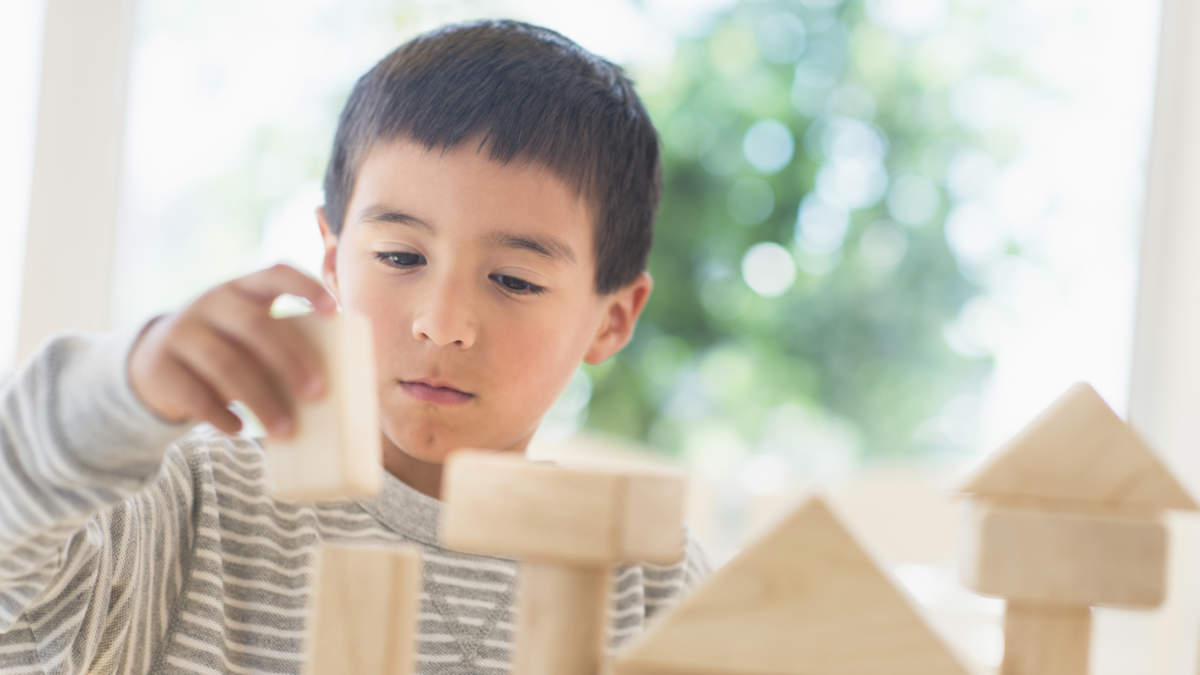
With all 240 cells for the first prototype completed, Altech Batteries will now start assembling the five modules that make up the ABS60 BatteryPack. Pic: Getty Images
- Altech Batteries completes manufacturing of all 240 cells for the first of two 60kWh CERENERGY® prototype batteries
- Cells now being welded to Cell Contacting System before completed modules are delivered to Fraunhofer IKTS for mounting into the ABS60 BatteryPack
- Improvements to cell design have improved energy capacity and reduced nickel content while lowering unit cost
Special Report: Altech Batteries has made excellent progress on manufacturing prototypes of its solid-state sodium chloride batteries with all cells for one of the two 60kWh CERENERGY® prototypes completed.
All 240 cells for the first ABS60 BatteryPack Prototype have now been fabricated, assembled and initialised at Fraunhofer IKTS Hermsdorf’s pilot plant after being cycled through several testing stations to ensure homogeneous cathode material distribution.
Altech Batteries’ (ASX:ATC) unique CERENERGY® solid-state batteries are ideally suited for grid energy storage use and require just common table salt (sodium chloride) and nickel with no need for lithium, cobalt, graphite and copper, limiting exposure to critical metal price rises and supply chain concerns.
They are capable of operating at a very wide temperature range (-40 degrees Celsius to +60 degrees Celsius), are fire and explosion-proof, and have a life span of more than 15 years.
Over their life, they are estimated to reduce costs by up to 40% compared to regular lithium-ion batteries and boast an emissions footprint at least 50% lower than that of lithium-ion batteries.
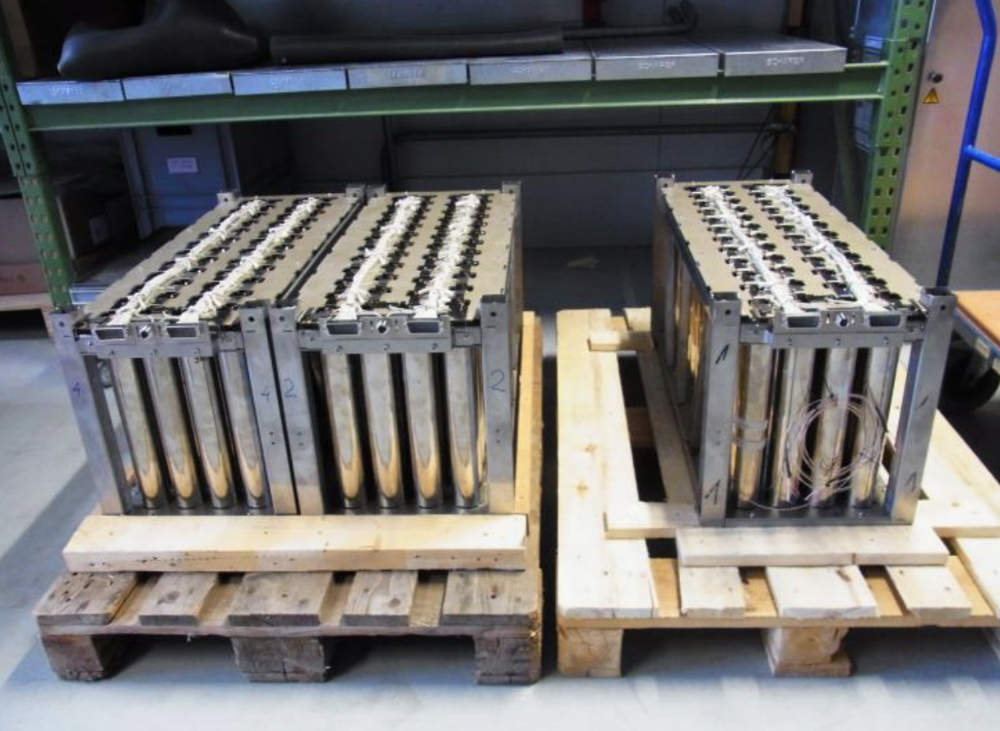
Manufacturing update
The completion of the first 60kWh prototype is accompanied by the completion and delivery of the cell contacting system (CCS) following stringent testing.
All parts of the five modules – each of which contains 48 cells – have now been collected for assembly with an external service contractor now welding the cells to the modules.
Once welding is completed, the ABS60 BatteryPack can then be completely assembled.
ATC adds that to ensure the most time-efficient welding, a unique tool was designed and built at Xenon, which is responsible for welding and quality control across the 120 MWh battery plant.
Trials to determine the best working parameters and to proof the handling of certain parts of the module have now been completed.
“Altech’s team in Germany, together with its joint venture partner Fraunhofer, and with the assistance of key suppliers, have made excellent progress on the fabrication of two 60kWh CERENERGY® ABS60 BatteryPack prototypes,” managing director Iggy Tan said.
“All components for the first BatteryPack have now been fabricated. Altech is now completing the welding of the cells to the Cell Contacting System, after which the five completed battery modules will be delivered to Fraunhofer IKTS in Dresden, where all five modules will be mounted into the ABS60 BatteryPack and the first ABS60 Prototype will be completed.
“The BatteryPack will then be available for testing and demonstration to potential customers, thereby assisting Altech in securing offtake and finance for the 120MWh CERENERGY® battery plant to be constructed on Altech’s land in Germany.”
Improved cell design
While the existing cell design for the CERENERGY® is already ground-breaking, both ATC and the Fraunhofer made several design improvements to the cell’s positive probe during fabrication of the prototypes.
These enhancements aimed to boost the cell’s energy capacity and reducing the nickel content while allowing for slightly faster charging and discharging, all at a lower unit cost.
Testing has revealed that most of the improved cells have higher-than-expected energy capacities, an outstanding result that strongly supports the chosen electrode design.
This article was developed in collaboration with Altech Batteries, a Stockhead advertiser at the time of publishing.
This article does not constitute financial product advice. You should consider obtaining independent advice before making any financial decisions.
Related Topics
UNLOCK INSIGHTS
Discover the untold stories of emerging ASX stocks.
Daily news and expert analysis, it's free to subscribe.
By proceeding, you confirm you understand that we handle personal information in accordance with our Privacy Policy.