QPM’s MD says they’ve won the ESG nickel race while competitors are still putting their shoes on
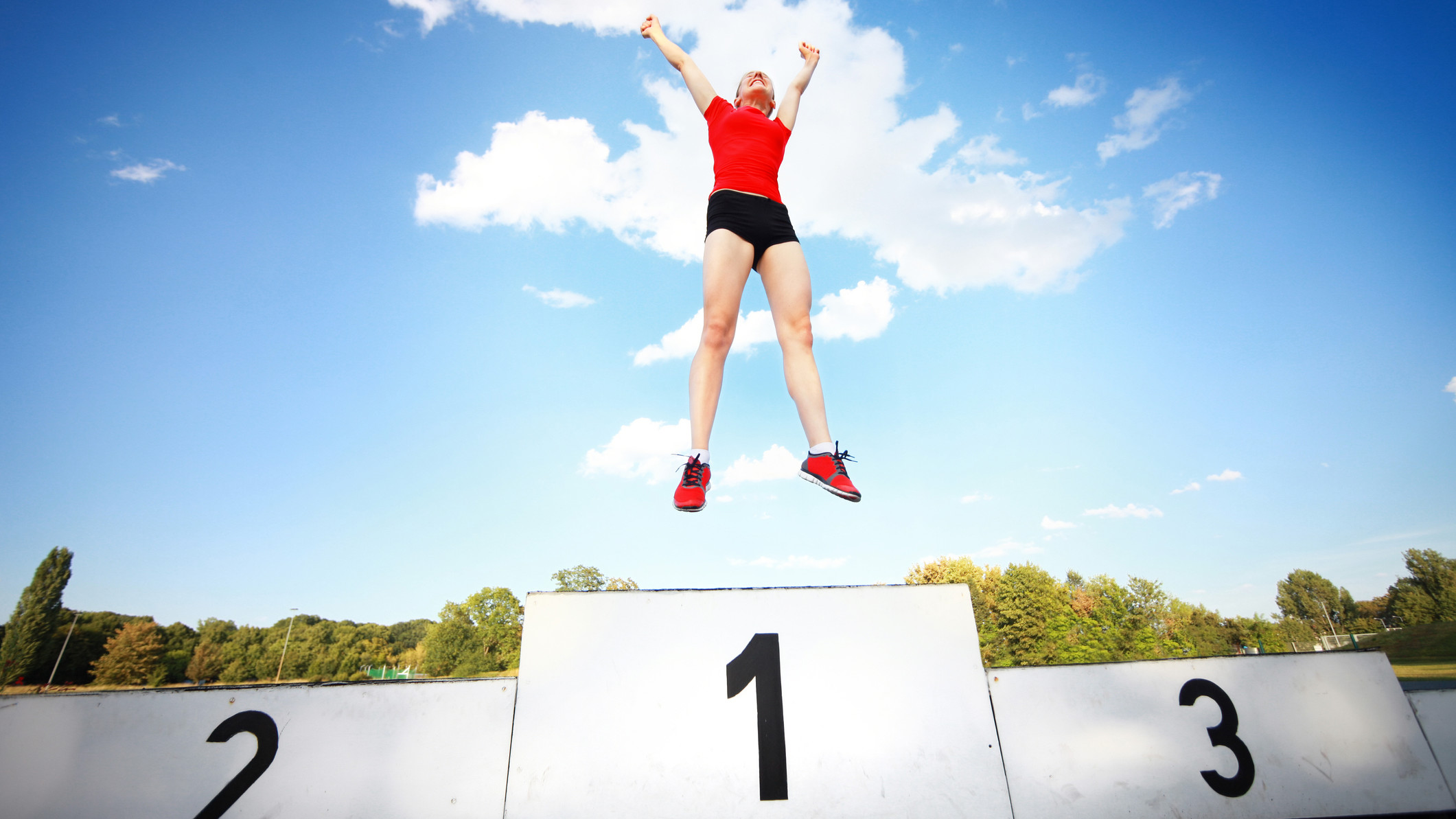
Pic: TommL / E+ / E+ via Getty Images
- For every 50kg on nickel in an EV around 5 tonnes of tailings are produced
- QPM has its sights set on zero waste from its TECH hub in Queensland
- An End of Waste Code means residue would be recognised as a resource – not waste
Most of the nickel produced today can’t economically or sustainably be used in the electric vehicle battery space without high pressure acid leaching (HPL) plants.
And when battery producers are looking at the ESG credentials of the nickel going into their products, the waste produced by HPL plants should be a major sticking point, Queensland Pacific Metals (ASX:QPM) MD and CEO Dr Stephen Grocott says.
“There’s about a dozen of these HPL plants in the world and there’s about four being built by the Chinese in Indonesia,” he said.
“Setting aside the technical complexity and failure rate of those plants, which is terrifying, for every dried tonne of ore that they take, they will produce around about 1.2 to 1.4 dry tonnes of tailings – in the form of sloppy, contaminated stuff that typically goes into a tailings dam.”
And while some geological locations mean this waste is handled reasonably well, in Indonesia it’s not only a high earthquake risk area, it has dense population centres – and high rainfall.
Dr Grocott says all those elements combined can raise the risk of a tailings dam disaster akin to the tragedy that unfolded at Vale’s Brumadinho dam in Brazil on 2019.
“Some of those dams that failed … destroyed huge swathes of the environment and killed hundreds of people,” Dr Grocott said.
“Unfortunately, the same Chinese company who’s designing those plants in Indonesia have built one which is in operation in Papua New Guinea and because tailings management is so difficult, they dump it in the ocean.”
“They’re now going to build these Brazil-style tailings dams in Indonesia, of the most seismically active regions of the world, which has intermittently high rainfall,” Dr Grocott says.
Interestingly, old mate Elon Musk just visited Indonesia to discuss a potential investment in Indonesia’s nickel industry and supply of batteries for electric vehicles.
This comes just a month after a consortium led by South Korea’s LG Energy Solution announced plans to invest $9 billion in Indonesia as part of a deal that would include everything from nickel refining to producing battery cells in country.
Indonesian President Joko Widodo met Tesla Inc (TSLA.O) Chief Executive Elon Musk on Saturday in Texas to discuss potential investments and technology, Indonesia’s government said in a statement. https://t.co/2p0DYxKNCS
— Stanley Widianto (@stanleywidianto) May 15, 2022
50kg of nickel in an EV equals 5 tonnes of tailings
Dr Grocott says that all of the nickel produced from the Papua New Guinea plant goes into the lithium-ion battery industry – which represents about 8% of the world’s nickel for EVs at the moment.
“I’ve calculated that 8% of the world’s electric vehicles are driving around on five tonnes of tailings dumped in the ocean,” he said.
“An average battery pack in an EV would have about 50kg of nickel and if you work it out, that’s about five tonnes of tailings dumped in the ocean.
“Countries like North America, North Asia, South America, Australia, and the EU – they do care where their nickel comes from.”
And he says it won’t be long until emerging technologies mean customers will be able to scan a QR code on their electric vehicle which will tell them where the nickel, cobalt, aluminium and rubber has come from.
Zero waste potential an industry first
What QPM are doing at their Townsville Energy Chemicals Hub in North Queensland is vastly different from the competition.
The TECH project will use an alternative to high pressure acid leach processing called the DNi Process, which QPM says will extract metals from nickel laterite ores (to be imported from New Caledonia) at a lower capital cost and with better environmental outcomes.
Essentially, all the valuable metals will be leached into solution and then recovered and refined into saleable products.
And the company has just highlighted the potential to achieve zero waste from their process.
“In the sustainability waste race, we’ve finished the race and we’ve got our feet up in the bar having a cold drink while the competitors are still strapping on their running shoes,” Dr Grocott said.
“I have been in this industry for a long time; I have never, ever in all my life seen anything which has the potential for zero solid waste – never.”
The ore processed is around 40% iron which ends up as a relatively pure iron product called hematite which – while not as valuable as the nickel and cobalt – can be sold.
And instead of producing a magnesium sulphate in tailings, the process also produces a magnesium oxide, which can also be sold.
Then the aluminium can be processed into high purity alumina and all that’s left is around 0.2-0.3 tonnes of silicon, which is mostly quartz, or beach sand.
“From one tonne of dry ore we don’t produce 1.2-1.4 tonnes of waste, we only produce around 0.2-0.3 tonnes of tailings, most of which is sand that is easily filtered and washed inert material that you can store on site,” Dr Grocott said.
Residue as a revenue stream
Through work with James Cook University, the company has shown the sand left from processing could potentially be used as engineered fill for industrial or construction use.
The plan is to undertake further geotechnical testwork on the residue and also environmental leaching testwork to confirm compliance with regulations – then the company can start the approvals process to obtain an End Of Waste Code from the Queensland Department of Environment.
‘End of waste’ meaning the residue would be recognised as a resource rather than a waste stream.
“Even if there was zero value in the hematite, if there was zero value in the magnesium, the direct nickel process would still be producing them and we would just have to store them,” Dr Grocott said.
“We don’t actually do a lot of extra work to produce them so we’re not bending over backwards and spending vast sums of money, it’s just that we’ve been lucky enough or clever enough to choose a process which is inherently less waste producing.”
The company is now working on the DFS for the TECH hub for mid-year, with production slated for 2024.
Related Topics
UNLOCK INSIGHTS
Discover the untold stories of emerging ASX stocks.
Daily news and expert analysis, it's free to subscribe.
By proceeding, you confirm you understand that we handle personal information in accordance with our Privacy Policy.