IperionX driving a circular titanium economy with the potential to be one of US’s largest suppliers

Waste not, want not – IperionX is making the most of scrap metal to make waves in the world of titanium. Pic via Getty Images
As the world shifts towards a circular economy, IperionX is taking titanium scrap and recycling it into titanium powder, with the potential to be one of the US’s largest suppliers.
The Industrial Revolution derived demand for commodities with minerals extracted from earth and fabricated into advanced products via mass production methods.
Customers were encouraged to use these products until end of life, dispose of them, before purchasing more.
The linear economy model worked well for economic growth but poorly for ensuring that the world’s resources would sustain generations to come.
However with shifts from a linear to circular economy, materials and products are now being regenerated and reused for as long as possible.
Meeting titanium needs in US
IperionX’s (ASX:IPX) is a leader in the circular economy taking titanium scrap and recycling it into titanium powder for fabrication of new products needed today.
IPX CEO Taso Arima said its mission is to be the leading developer of low-to net-zero carbon, sustainable, critical material supply chains for advanced industries including space, aerospace, electric vehicles, and 3D printing in the US.
He said although the US is the largest consumer of high-quality titanium in the world, it doesn’t currently produce any of the titanium metal that it needs.
“It is our mission to change that, and to re-shore a low-cost, sustainable, end-to-end titanium supply chain in the US,” Arima said.
Headquartered in the US, with operations currently in Tennessee and Utah, IPX is also listed on the NASDAQ (IPX).
Titanium Demonstration Facility in Virginia
Final engineering and design for its 125 tonne per annum Titanium Demonstration Facility (TDF) in Virginia, using its breakthrough Hydrogen Assisted Metallothermic Reduction (HAMR) technology, is nearing completion, with first titanium powder production targeted for the first quarter of 2024.
There are also defined plans for a simple modular expansion that will transform the TDF into the Titanium Commercial Facility (TCF-1) with production capacity of 1,125tpa in 2025, which will make it one of the world’s largest producers of titanium metal powders, and the only producer using 100% titanium scrap metal as a feedstock. No other incumbent titanium metal manufacturing process, including the Kroll process, can use 100% scrap metal as a feedstock.
Assuming a conservative spherical titanium metal powder price of ~US$130/kg (vs. current estimated market pricing of ~US$200/kg), and using key operating assumptions, the TCF-1 has the potential to generate revenue of ~US$145 million and EBITDA of ~US$100 million in 2026.
IPX has conducted a life cycle assessment to understand the overall potential impact of its technology, with the TDB being the only such facility with zero Scope 1 & 2 emissions and the lowest carbon intensity for any commercial titanium metal powder product.
“IperionX technologies are key to transitioning the US domestic titanium supply chain to a more circular mode,” Arima said.
He said that IperionX’s proprietary metal technology demonstrates that the development of a sustainable and low-cost supply chain to support the Titanium Age is possible.
“Increasingly, titanium is the metal of choice for critical applications and advanced industries, including air and ground transportation, electronics, construction, and industrial, medical, and consumer goods,” he said.
Arima said by diverting valuable titanium from yesterday’s waste stream and recycling the metal for new titanium products, IPX is helping meet today’s critical needs for North American sourced materials.
“IperionX will be adding value to the economy and enabling current and future generations to access the materials they need,” he added.
This article was developed in collaboration with IperionX, a Stockhead advertiser at the time of publishing.
This article does not constitute financial product advice. You should consider obtaining independent advice before making any financial decisions.
Related Topics
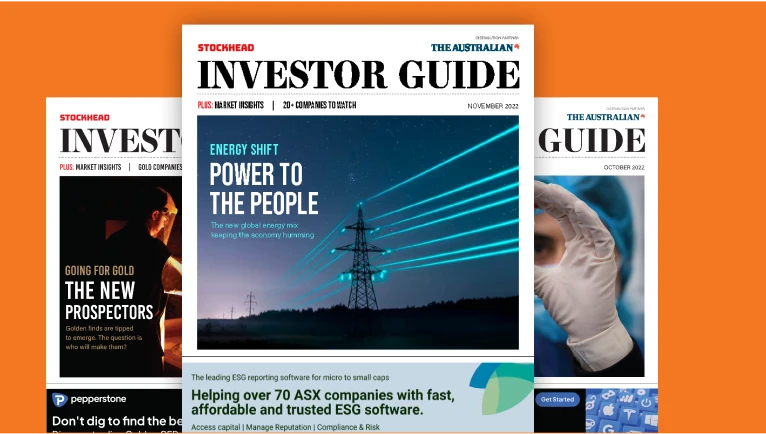
UNLOCK INSIGHTS
Discover the untold stories of emerging ASX stocks.
Daily news and expert analysis, it's free to subscribe.
By proceeding, you confirm you understand that we handle personal information in accordance with our Privacy Policy.