Here’s how green concrete can meaningfully slash global emissions
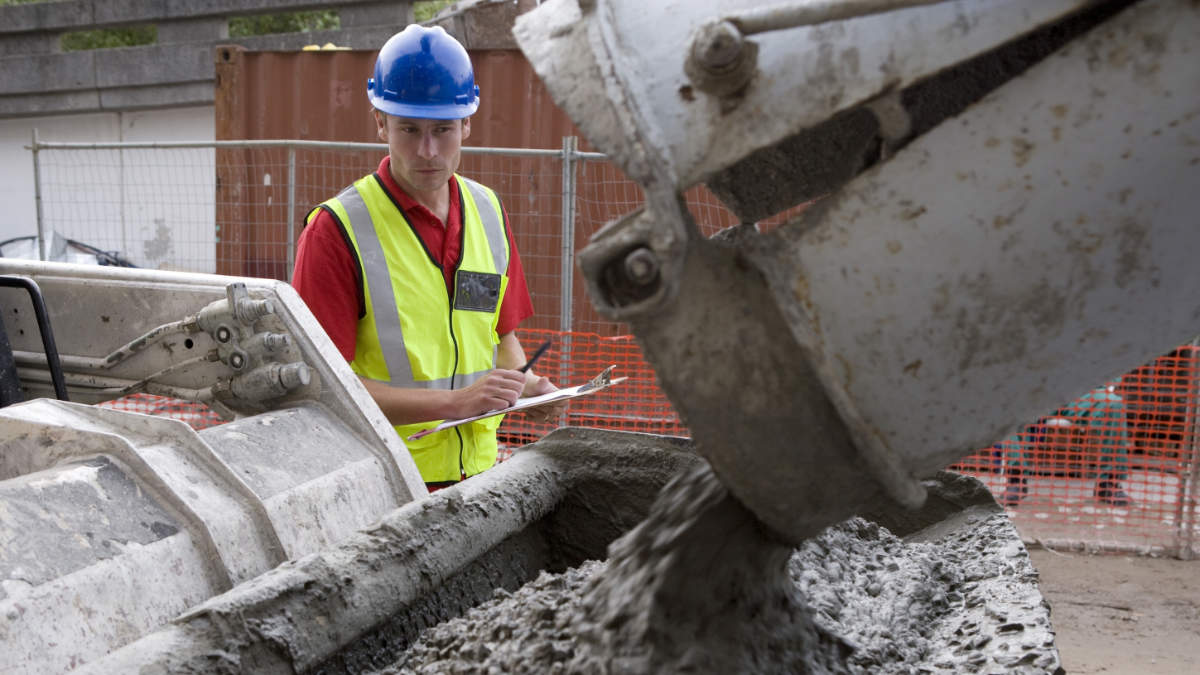
Making concrete green by either reducing the use of cement or using cement alternatives can drastically cut global emissions. Pic: Getty Images
- Producing green concrete could significantly reduce the building and construction sector’s emissions
- Cement production generates significant emissions due to energy requirements and process method
- Suvo Strategic Minerals is providing both a transition and replacement product for cement use in concrete
The global push to achieve net zero emissions by 2050 requires a multi-pronged approach outside of just power generation and transportation, which are two areas that have received excessive attention to date.
Efforts also need to be made to clean up industrial processes with one example being the use of clean hydrogen – whether of the green or white varieties –to quickly reduce emissions in industries and sectors that already use the gas as a feedstock.
Using clean hydrogen to displace the use of fossil fuel-derived hydrogen in the manufacture of ammonia fertiliser for instance could significantly reduce emissions as producing ammonia accounts for about 1.2% of global emissions in 2020.
Another challenging sector to decarbonise is the building and construction sector, which accounts for a staggering 37% of global emissions.
The production and use of materials such as cement, steel and aluminium all come with a significant carbon footprint.
Having the ability to reduce this footprint will go a long way towards meeting net zero targets.
This has been recognised by Australia with the federal government introducing a $1bn Green Iron Investment Fund in February 2025 to boost green iron manufacturing by supporting early mover green iron projects and unlocking private investment at scale.
Green concrete
The ability to reduce the emissions associated with producing cement and concrete will also go a long way towards cleaning up the sector.
One method to making concrete greener is to displace the use of cement with coal ash, a process that is already seen in some low carbon concrete that replaces 40% of the cement with coal fly ash – a widely available waste product from the burning of coal to generate electricity.
Engineers at RMIT University have developed a method that doubles the amount of coal fly ash that can be used, which will in turn reduce the amount of cement required.
This method can also be used to harvest and repurpose lower grade and underutilised ‘pond ash’– taken from coal slurry storage ponds at power plants – with minimal pre-processing.
This has the added benefit of using a byproduct of burning coal, which is probably the most carbon intensive method of power generation and heating, to reduce emissions, and could also reduce the amount of waste in coal slurry storage ponds if pond ash is used.
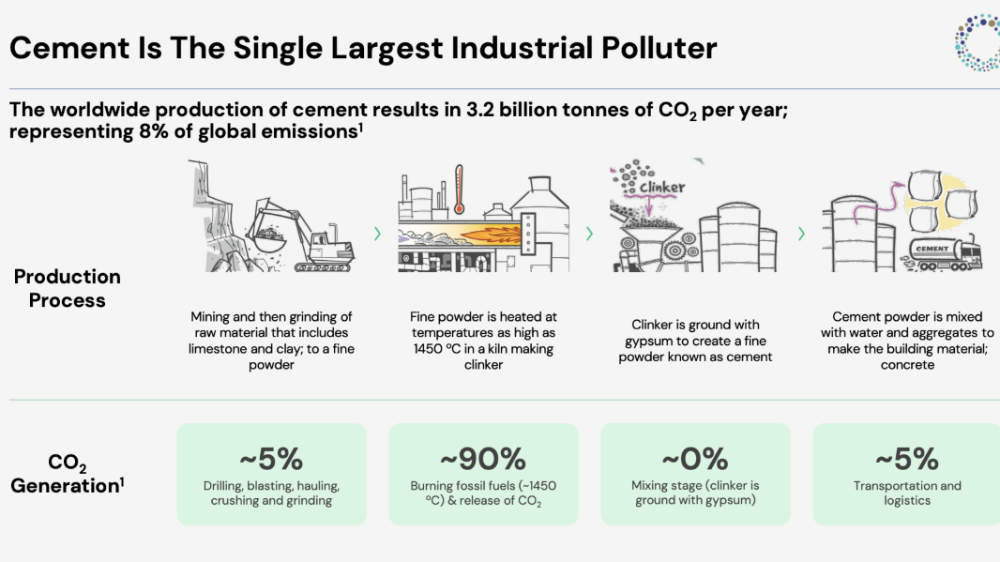
Cleaning up cement
Another path to making concrete greener is the one taken by Suvo Strategic Minerals (ASX:SUV), which strikes at the core of the issue by either replacing cement or making cement greener.
Cement production makes up 8% of global carbon emissions – more than the entire global car fleet – and its demand has risen in lockstep with that for concrete, one of the most common building materials.
Its sizeable share of the emissions pie is thanks to the high energy requirements and carbon emissions associated with producing clinker – the mix of limestone and other minerals that make up the bulk of cement.
Clinker is produced when limestone and other minerals are heated to extreme temperatures in a kiln to start and sustain the process.
This process not only requires vast amounts of energy – typically through the burning of fossil fuels that generate CO2 – and also releases CO2 as a byproduct.
One alternative that SUV has developed is geopolymer cement, a material made from industrial by-products such as nickel slag – a product from making nickel pig iron that would typically be discarded in landfills.
Nickel slag is combined with other waste materials, such as fly ash, along with chemical activators to create geopolymer cement, which has a significantly lower carbon footprint than cement.
Its compressive strength of 40 megapascals in lab tests could make it suitable as a viable alternative for up to 80% of precast concrete applications worldwide.
However, expecting the industry to jump immediately on its geopolymer cement is a big step. With that in mind, Suvo is also working on hybrid cement products to bridge the transition.
It has been developing a hybrid cement solution which combines cement with calcined clays produced using kaolin sourced from its wholly-owned Pittong operation in Victoria.
This has the potential to reduce the amount of cement used by up to 70%.
As part of this, SUV is working with Deakin University to formulate various lower carbon concrete mixes.
The university’s Institute for Frontier Materials will develop various mixes using a low-cost hydrous kaolin supplied by Suvo, targeting the formulation of structural, 50 megapascal concrete.
Formulations developed at this stage will comprise ~50% Portland cement replacement with the second stage testing program targeting to develop up to 70% Portland cement replacement, which will further reduce embodied carbon.
Resulting products will form part of the field trials offered the Victorian Government’s Level Crossing Removal Project.
SUV has also partnered with WA’s PERMAcast R&D in an equal joint venture to deliver low carbon concrete products.
At Stockhead, we tell it like it is. While Suvo Strategic Minerals is a Stockhead advertiser, it did not sponsor this article.
Related Topics
UNLOCK INSIGHTS
Discover the untold stories of emerging ASX stocks.
Daily news and expert analysis, it's free to subscribe.
By proceeding, you confirm you understand that we handle personal information in accordance with our Privacy Policy.