Suvo’s ‘green cement’ targets Co2 emissions, eyes massive global market
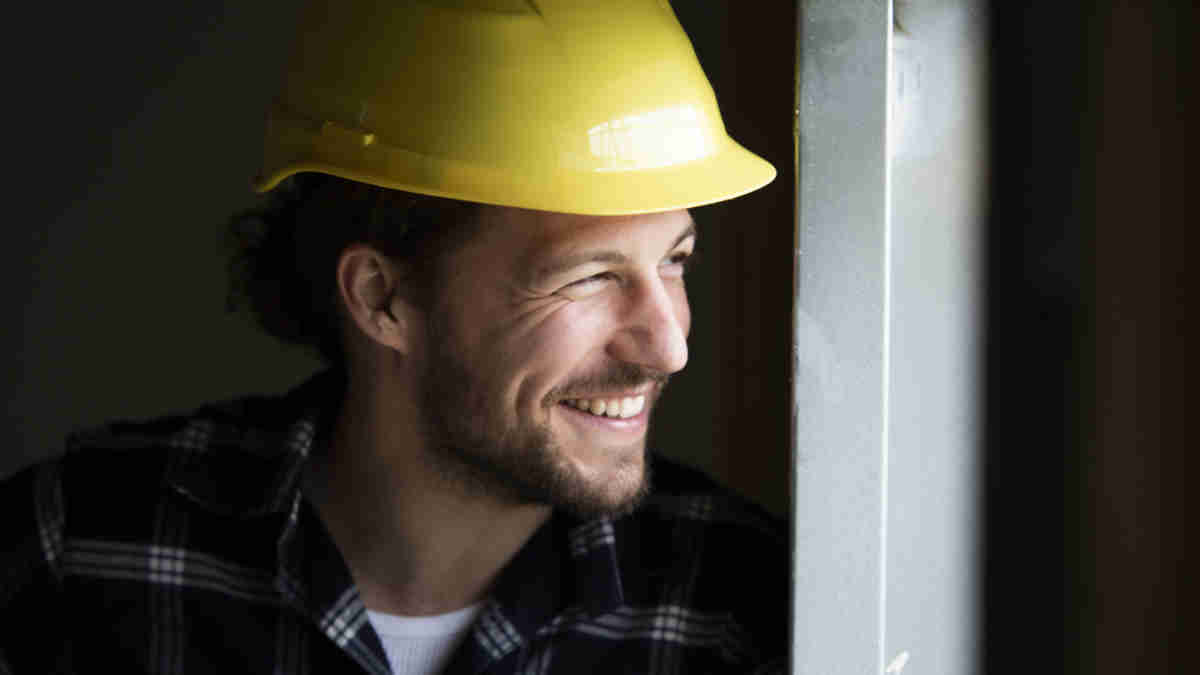
Suvo’s green cement could cut emissions in cement production. Picture via Getty Images
- Cement’s greenhouse problem is increasingly in focus
- Suvo is aiming to cut emissions in cement production
- The company eyes a potential trillion dollar market
The global cement industry is nearly a trillion-dollar market, with concrete being the second most consumed material on Earth, surpassed only by water.
But while cement is the cornerstone of modern construction, its production generates large amounts of carbon dioxide (Co2), making it one of the highest sources of global emissions.
According to Aaron Banks, executive chairman of Suvo Strategic Minerals (ASX:SUV), this sector has an immense environmental footprint.
“Cement production has long been one of the most carbon-intensive activities on the planet,” Banks said. “If you look at it, cement production alone accounts for more emissions than the entire global car fleet.”
Portland cement, which is the most commonly used type of cement in construction, is produced by heating limestone to extreme temperatures. This process not only requires vast amounts of energy, typically derived from fossil fuels, but also releases Co2 as a byproduct.
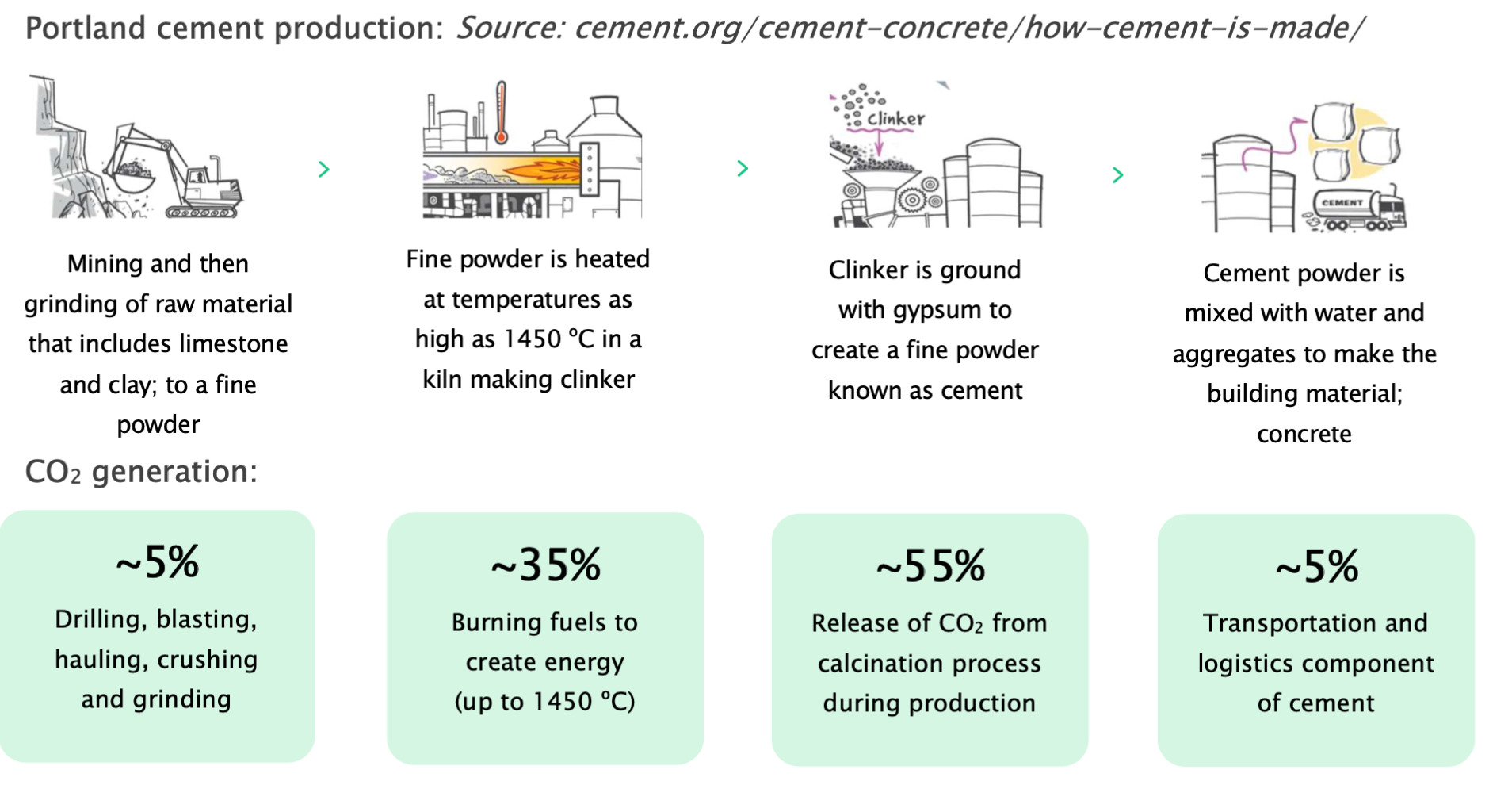
Recognising the dire need for change, Suvo has concentrated on developing alternatives.
The company focuses on producing the essential binder for concrete – as opposed to concrete itself – which allows for greater scalability and a wider global reach.
“We’ve been working on an alternative product – a green cement that eliminates the need for Portland cement entirely,” Banks explained.
Suvo’s solution comes in the form of geopolymer cement, a material made from industrial by-products such as nickel slag.
Nickel slag is a waste product from making nickel pig iron, which would usually be discarded in landfills. Suvo’s partnership with PT Huadi in Makassar, Indonesia, provides the company with a significant supply of nickel slag well into the future.
The process of making geopolymer cement involves combining nickel slag with other waste materials, such as fly ash, along with chemical activators.
This mix results in a product the company says has a significantly lower carbon footprint than Portland cement.
“We’ve also achieved a compressive strength of 40 megapascals in lab tests, which is more than enough for most precast concrete products,” Banks added.
Banks believes this result positions Suvo’s geopolymer cement as a viable alternative for up to 80% of precast concrete applications worldwide.
Hybrid cement solution
However, making a shift away from Portland cement won’t be without its challenges.
“The whole industry has been reliant on Portland cement for over 150 years, so it’s not an easy change,” Banks acknowledged.
To ease the transition, Suvo has been developing a hybrid cement solution. This hybrid product combines Portland cement with calcined clays, reducing the amount of Portland cement by as much as 70%.
“The hybrid model is important because it offers a way for companies to reduce their carbon footprint without abandoning Portland cement entirely,” said Banks.
“It’s a stepping stone. If we can get this hybrid cement into the market quickly, it’ll be a bridge to full adoption of our geopolymer cement.”
Suvo has already partnered with a company called Permacast to explore the viability of the product.
Permacast is one of the largest precast concrete companies in Australia, and has worked on high-profile projects including the construction of Optus Stadium in Perth.
“They’ve just cornerstone-funded our last round,” Banks said. And they’re already on board to trial and incorporate our green cement into their production.
“If a commercial partner as prominent as Permacast is going to those lengths, to people who know the industry inside out, it speaks to the potential of Suvo’s products and the risk profile.”
Kaolin’s role in Suvo’s strategy
In addition to its work with geopolymer cement, Suvo’s kaolin operations play a key role in the company’s strategy.
Kaolin, a type of clay, is a material that can be used in cement production to reduce emissions. When calcined, kaolin can serve as a substitute for traditional cement components, further lowering the carbon footprint of concrete products.
Suvo’s Pittong Kaolin operation in Victoria is Australia’s only wet kaolin mine and processing facility.
The company has invested more than $5 million since acquiring it in 2021 and has increased production. The resource now boasts over 18 million tonnes of JORC-compliant inferred and indicated kaolin.
“We’re exploring ways to use this material, alongside nickel slag and fly ash, to further reduce the carbon footprint of concrete production,” said Banks.
Suvo has already established a good customer base for the kaolin products, particularly within the ceramics, paper, cosmetics, and paint industries.
At the moment, clients include Dulux, Nippon Paint, and even BodyShop and Estee Lauder.
A turning point for the cement industry
Banks said Suvo has spent years refining its process, which he describes as “perfecting the characterisation piece” – the ability to identify various waste streams to determine their suitability for cement production.
He believes this technical advantage puts Suvo “ahead of the curve” compared to others in the industry, especially as the company collaborates with major players in sectors like lithium and bauxite mining.
“I’m not aware of anyone else in the space that’s that far up the curve. We’re at a point now where we can start to see these relationships materialise into concrete results.”
The company is already producing precast concrete products for government projects, which will undergo lifecycle analysis and environmental testing soon.
And Banks said it’s now moving towards financial studies and commercial agreements with some of the largest mining companies and industrial players in the world.
“We expect to fully commercialise our hybrid cement within the next 12 months, and our geopolymer cement could take another 18 months to gain broader market adoption,” he shared.
He’s also optimistic about Suvo’s potential to generate carbon credits.
“By taking waste streams, repurposing them, and getting the methodology right, we’re also addressing the carbon accounting piece.”
Banks sees the current moment as a major turning point for the cement industry, similar to the movement away from fossil fuels.
He sees a future where greener alternatives to Portland cement become the norm.
“The opportunity is enormous,” Banks said.
“The cement industry is bigger than the global lithium market, bigger than the global copper market and even larger than the global iron ore market.”
The views, information, or opinions expressed in this article are solely those of the interviewee and do not represent the views of Stockhead.
Stockhead has not provided, endorsed or otherwise assumed responsibility for any financial product advice contained in this article.
At Stockhead we tell it like it is. While Suvo Strategic Minerals is a Stockhead advertiser, it did not sponsor this article.
Related Topics
UNLOCK INSIGHTS
Discover the untold stories of emerging ASX stocks.
Daily news and expert analysis, it's free to subscribe.
By proceeding, you confirm you understand that we handle personal information in accordance with our Privacy Policy.