Bulk flotation test work supports premium-grade phosphate-rare earth concentrate out of RareX’s Cummins Range
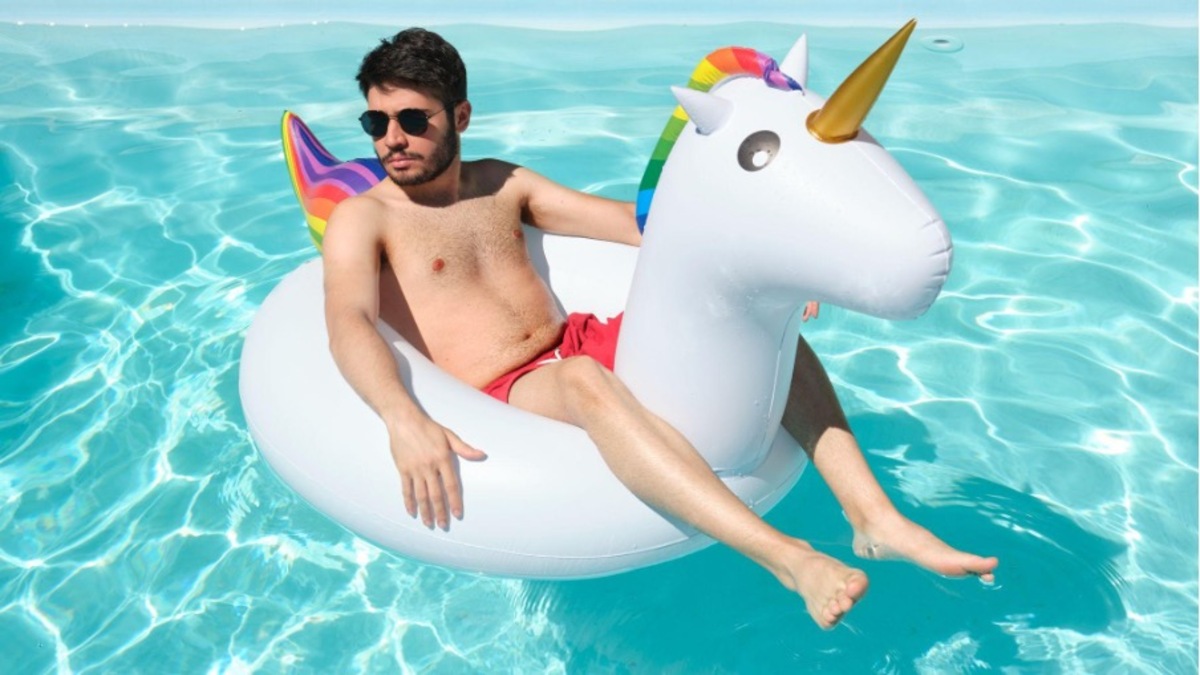
RareX has confirmed from bulk flotation trials that it can produce high grade concentrate grades. Pic via Getty Images.
- RareX added to its understanding that producing phosphate concentrate from a conventional flotation circuit is best for mineral recovery for both phosphate and rare earths
- A Stage 1 DFS is due at the end of the year
- Cummins Range is shaping up to be a significant REE and phosphate producer across its three-stage development plan
Bulk flotation testwork has now provided further support to RareX’s plan to produce premium-grade phosphate-rare earth concentrate in Stage 2 of its Cummins Range development.
A recent enhanced scoping study – the first proper look at the economics of building a project – envisaged a three-stage, 18 year project development strategy for Cummins Range, Australia’s largest undeveloped rare earths project and a significant source of phosphate.
The first three years of production, called Stage 1, involves a simple mining and crushing operation to produce a phosphate DSO that can be used as direct application fertiliser, RareX says.
This de-risking step requires low capex of $45m to deliver robust economics from the production of about 300,000tpa of ore grading 23% P2O5.
The substantially larger $304m capex Stage 2 beneficiation operation would then produce 550,000tpa of higher value phosphate-rare earth mineral concentrate, containing about 169,000t of P2O5 and 12,000t of total rare earth oxides (TREO).
Stage 3 will see a $63m upgrade to the Stage 2 plant in year 13 to produce a concentrate from the un-weathered, fresh rock.
‘Outstanding’ met test work continues to support and build understanding of Stage 2 of the project.
Recent bulk flotation test work now shows consistent and “outstanding” performance in production of a phosphate-rare earth concentrate, supporting production of a premium grade concentrate in Stage 2. Stage 2 product is destined for the phosphoric acid producers where a low concentration leach shows clean phosphate can be stripped from the mineral concentrate, leaving the rare earths behind.
91% of the phosphate content recovered into a concentrate at a grade of more than 34% phosphate, supporting the company’s belief that a simple, conventional flotation circuit is all that’s required to produce a premium phosphate-rare earths product.
CEO James Durrant, when interviewed by Stockhead, said: “Stage-2 is when we become a rare earth producer through a combined phosphate-rare earth mineral concentrate. These tests were part of the ongoing metallurgical trials, across the resource, to check that our floatation regime is performing as modelled for Stage-2. This has proved to be so with excellent recovery of the phosphate and rare earth minerals. We will continue to test other parts of the resource to ensure we understand the variability and build that into our engineering.”
Additionally, the results also show good, rare earths recovery of about 70%, which is in line with expectations and further supports assumptions laid out in the Scoping Study.
“This floatation testwork further supports the opportunity at Stage 2 to produce a high value-in-use phosphate-rare earth beneficiated product at Cummins Range as part of our rare earths business,” chief executive officer James Durrant said.
“The upgrade and grade recovery results are very encouraging and support good product quality and resource utilisation.”
Geotechnical testing supports Stage 1 DFS
The company also received results from initial drill core geotechnical testing that will support the Stage 1 Definitive Feasibility Study that’s due at the end of 2023.
This testing found that most samples collected from the regolithic material to be mined in Stage 1 and 2 of the project are in the range of about 70MPa in the unconfined compressive strength (UCS) tests.
Importantly for the company, this result is well within the range for surface mining, making it the preferred mining method over drill and blast, which could reduce permitting requirements for the project.
Surface miners could also provide further upside to mining and processing costs through pre-screening and crushing of ore in-situ, which could lower costs by replacing primary crushing, and reduce environmental impacts common with regards to blasting operations.
“The geotechnical results not only support optimised mine designs but also open up the opportunity for surface miners, rather than drill and blast, potentially simplifying the project further, particularly at start-up,” Durrant says.
Coming work
With the encouraging flotation results, RareX plans to focus the next phase of the phosphate mineral beneficiation testwork on demonstrating similar, if not better, flotation performance of the Rare Dyke material.
This work will also seek to optimise grind size, further suppress gangue (waste material), improve flotation conditions and optimise the circuit configuration to ensure the technical and economic feasibility of the beneficiation flowsheet.
RareX has also reached out to potential providers of surface miners and surface mining services to establish the viability of surface mining as an operational pathway.
This article was developed in collaboration with RareX, a Stockhead advertiser at the time of publishing.
This article does not constitute financial product advice. You should consider obtaining independent advice before making any financial decisions.
Related Topics
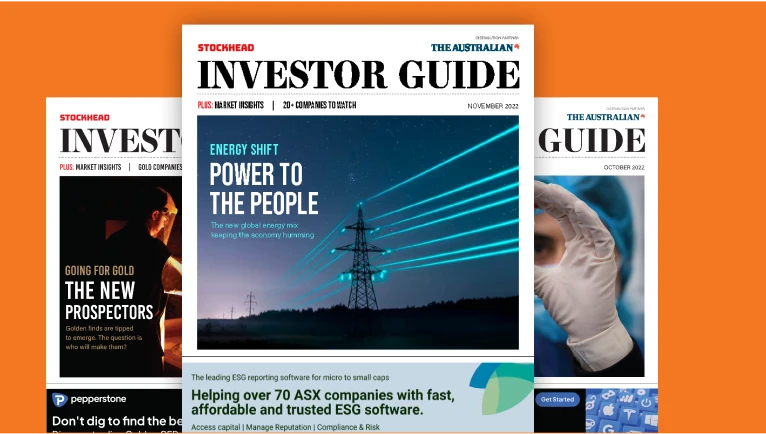
UNLOCK INSIGHTS
Discover the untold stories of emerging ASX stocks.
Daily news and expert analysis, it's free to subscribe.
By proceeding, you confirm you understand that we handle personal information in accordance with our Privacy Policy.