Australian Vanadium secures $1.25m government grant for research initiative
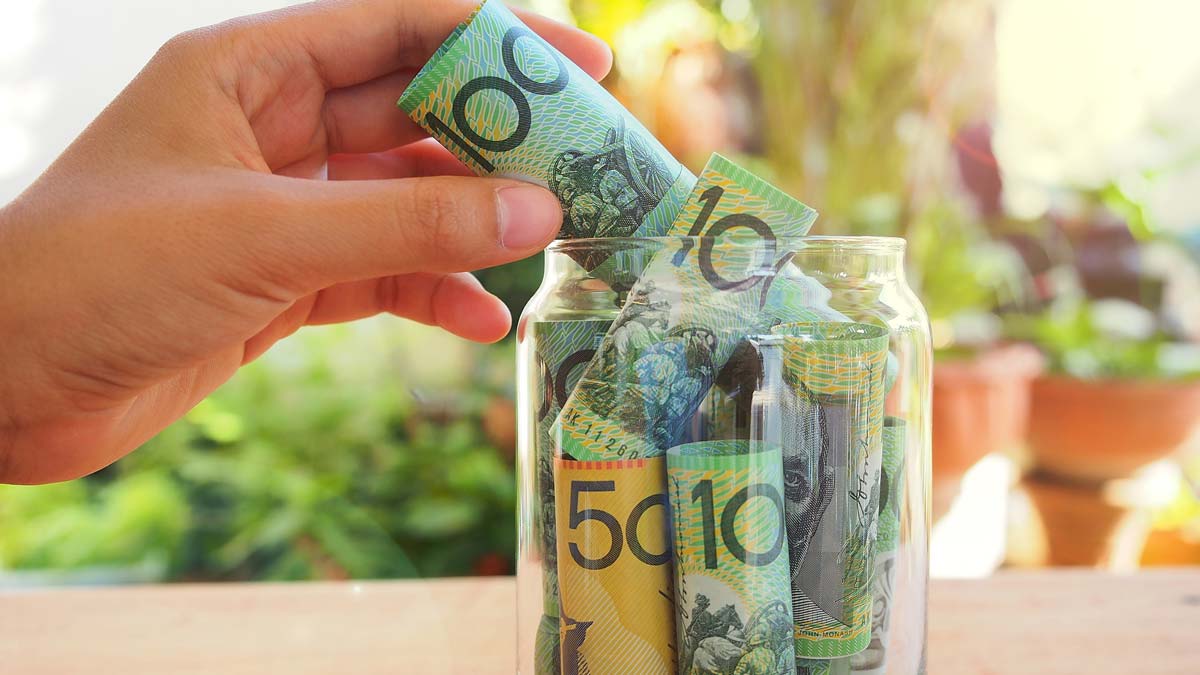
Australian government funds Pic: Getty Images
Special Report: Australian Vanadium has received a $1.25m grant from the Australian government to help fund research aimed at improving the efficiency of vanadium processing.
The company is carrying out the $4.9m research initiative in conjunction with Wood, ALS Laboratory, Curtin University and the Australian Nuclear Science and Technology Organisation.
Australian Vanadium (ASX:AVL) has committed to contributing $2.5m to this research while the government is injecting its $1.25m through its highly competitive CRC-P grant for critical metals research.
The remaining funding will be provided by the participating partners through in-kind contributions.
This research is aimed at improving all aspects of vanadium production from vanadium-titanium-magnetite (VTM) deposits such as the company’s namesake project.
It will investigate four opportunities in comparison to the conventional process for producing vanadium as vanadium pentoxide.
“The results of this research and development project will have far reaching benefits in the vanadium market globally and will enable us to develop and operate a low-cost, fully integrated vanadium operation here in Western Australia,” chief operating officer Todd Richardson said.
Research opportunities
The first is the testing and evaluation of new processing equipment and approaches to improve on the existing extraction techniques.
Standard rotary kiln roasting and vat leaching methodology used in the conventional process achieves an average of about 87 per cent vanadium extraction.
This test work will begin in February 2020 with a pyrometallurgical pilot test using a travelling grate kiln at the Metso Research and Test Center.
Read: Test work proves up processing pathway for Australian Vanadium
The research initiative will also explore and test integrated hydrometallurgical processing technologies with the goal of lowering the cost of producing ultra-high purity vanadium.
Standard leach and precipitation flowsheets limit final vanadium product quality and are not capable of producing ultra-high purity vanadium used for battery, catalyst and aerospace applications without separation and costly upgrading.
Thirdly, research will also be carried out to develop economic processes to enable the recovery of additional by-products, such as chromium, from the VTM ore that would normally be rejected as waste during the conventional process.
Australian Vanadium added that alternate processing pathways and new advances in processing technology would be explored to create saleable by-products and reduce the need for sulphate salts disposal and mine closure reclamation activities.
Potential outcomes
The company says possible outcomes from the research include the use of a pelletisation process for vanadium concentrate rather than a standard rotary kiln design.
This could increase vanadium extraction while reducing gas consumption.
Other benefits could include pilot scale testing that could reliably produce ultra-high purity vanadium, economic recovery of critical minerals and developing a fully integrated geological, mining and processing model for the Australian Vanadium project.
These could decrease processing costs, improve the quality of vanadium products and enable the extraction of valuable by-products, all of which could support the company’s goal to become one of the world’s lowest cost vanadium producers.
>> Now watch: 90 seconds with Vincent Algar, Australian Vanadium
This story was developed in collaboration with Client Name, a Stockhead advertiser at the time of publishing.
This story does not constitute financial product advice. You should consider obtaining independent advice before making any financial decisions.
Related Topics
UNLOCK INSIGHTS
Discover the untold stories of emerging ASX stocks.
Daily news and expert analysis, it's free to subscribe.
By proceeding, you confirm you understand that we handle personal information in accordance with our Privacy Policy.