Hazer’s disruptive clean hydrogen tech set to make prime time debut
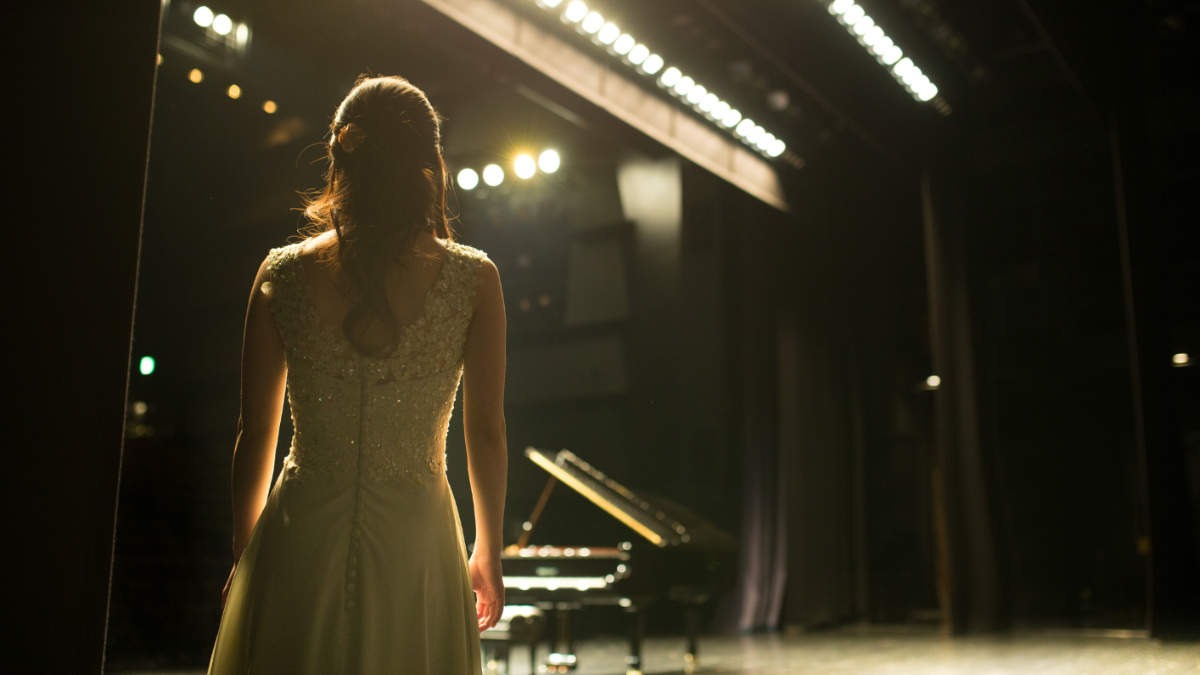
Hazer Group’s clean hydrogen technology is all but ready for commercial deployment. Pic: Getty Images.
- Hazer Group’s technology produces hydrogen and graphite without any carbon emissions using a methane-rich feedstock
- Process is less energy intensive compared to competitors and seven times cheaper than green hydrogen
- Commercial demonstration plant has clearly proven the reliability of the company’s tech with up to 98% uptime
Special Report: Disruptive technologies tend to significantly alter the way things operate and that’s exactly what Hazer Group expects its namesake hydrogen production technology to do to the hydrogen sector.
However, before we get into why the HAZER process is so disruptive, we need to look into hydrogen and its industrial uses to understand why it has the potential to make a significant impact.
Hydrogen is the lightest and single most abundant element in the universe though its high reactivity means it is rarely found in its natural state on Earth and is most commonly found in good old water, which is made up of two hydrogen and one oxygen atoms.
The same reactivity makes it highly combustible as we found to our detriment when it was used as the lifting gas (being much lighter than air) for zeppelins, which led directly to the Hindenburg disaster in 1937.
More importantly, hydrogen is used in a multitude of industrial uses with notable examples being the upgrading of fossil fuels, the production of ammonia fertiliser, as a hydrogenating agent, and as feedstock for producing chemicals such as ethanol and methanol.
Emerging uses which are still developing and include replacing coal in the production of steel and for energy generation – either by burning hydrogen or a carrier such as ammonia or in a fuel cell.
The point that needs to be made is that large quantities of hydrogen are already in use throughout the world for many critical applications.
Where the problem lies is that most of the hydrogen used today is produced using steam methane reforming (SMR), a high temperature process that uses the reaction of water and methane (natural gas) to produce hydrogen and a heap of carbon dioxide emissions.
Cleaning up hydrogen
The high level of emissions is one of the key reasons why industrial users are so keen to replace SMR with cleaner alternatives.
For a long while, green hydrogen was seen as the answer to producing clean hydrogen that could quickly decarbonise the industries which require the gas as feedstock.
However, as Fortescue’s decision to pull back on its ambitious goal of producing 15Mtpa of green hydrogen by 2030 due to high costs demonstrated, this was easier said than done.
While it is still a promising technology, many factors need to come together – such as cheaper energy costs along with more affordable and efficient electrolysers – before prices come down sufficiently to make it competitive. A process that could potentially take too much time.
Here is where Hazer Group (ASX:HZR) believes that it can successfully disrupt the production of hydrogen for industrial users.
While the HAZER process is essentially a variation of methane pyrolysis, which uses heat to break down methane into hydrogen and a solid carbon, it is considerably ahead of its competitors with some 17 years of work and $110m invested into its development.
“We have scaled this up successfully five times. Not many technologies in this space can claim to have done that,” managing director Glenn Corrie told Stockhead.
“We are a leader in this space worldwide – the use of thermocatalytic methane pyrolysis to remove carbon from natural gas to produce clean hydrogen and a solid, advanced carbon material in graphite with zero emissions.”
He noted that the company’s current commercial demonstration plant (CDP), which has now achieved considerably more than the 240 hours of continuous operation it had announced in early August, is the latest scale-up that seeks to demonstrate that its technology operates at commercial scale on a continuous basis.
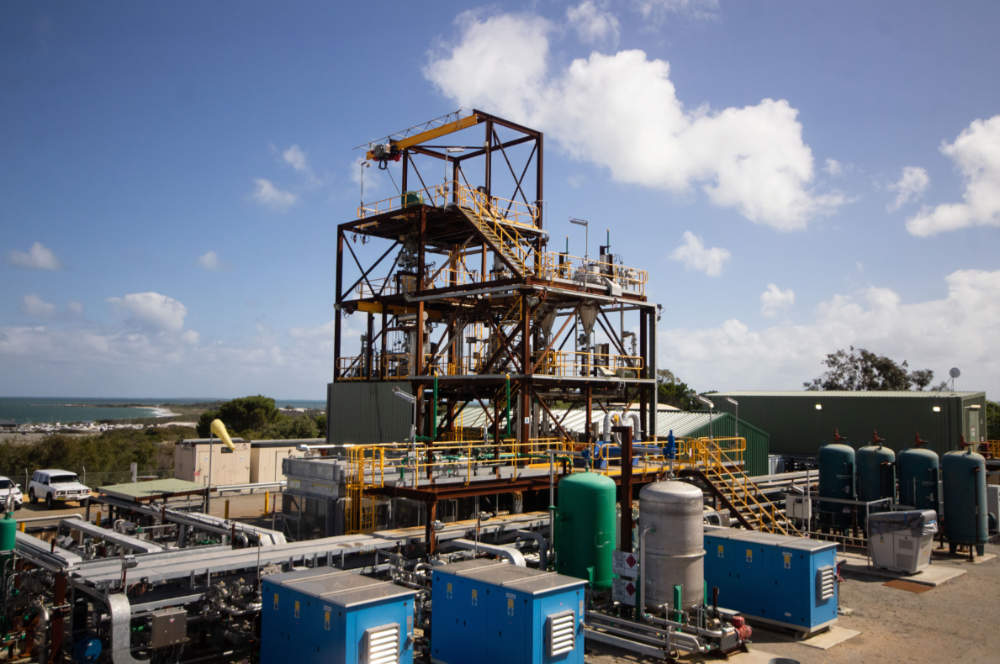
Hazer’s commercial demonstration plant in Western Australia. Pic: Bevis Yeo
This in turn will completely de-risks the technology for commercial deployment, a process that Corrie believes will be completed by the end of this year.
“The plant is doing everything it should be doing in terms of the technology. The most important things are continuous operation. Our uptimes are very close to 98% of the time, which is very high,” he added.
“We have really demonstrated and proven that the reliability of the facility is there.”
The CDP, whose construction was supported by a grant of almost $10m from the Australian Renewable Energy Agency back in 2020, is designed to be capable of producing 100 tonnes of hydrogen per annum using methane-rich biogas feedstock sourced from Western Australia’s Water Corporation.
As a result of using biogas, Corrie notes that the CDP’s carbon footprint is actually negative as “we are taking a very dirty source of gas, removing impurities like hydrogen sulphide, flowing the resulting methane through our process and emerge with clean hydrogen and a graphite co-product”.
Growing interest
The advanced nature of HZR’s project is clearly demonstrated by the company having signed up four foundation customers across its target markets of North America, Europe and Asia.
“In North America, we are partnered up with FortisBC, Europe the giant utility Engie, in Asia we have teamed up with Chubu Electric Power – the world’s largest LNG importer – and Chiyoda Corp as a partnership,” Corrie said.
“We have also joined forces with Mitsui, a big global trading group to explore and develop the markets for our graphite co-product.
“The most recent deal we signed up is with POSCO, the sixth largest steel maker worldwide and largest outside of China. It is a massive opportunity for us to be chosen as the preferred technology provider for their green steel process, which has got massive potential and scale.
“You can imagine the potential of that transaction. We are very excited about it, it is the first time that we have struck a partnership in steelmaking, which is responsible for up to 10% of the world’s CO2.
“It is definitely an industry that is low hanging fruit and to be able to work with groups like POSCO is strong validation of our technology.”
Corrie pointed out that all of its partners have completed anywhere between one and three years of due diligence on its technology and had chosen to go ahead with the HAZER process.
The point of difference
So just what makes HZR’s technology stand out from its competitors?
Unlike regular methane pyrolysis, the company’s HAZER process uses an abundant and low-cost iron ore catalyst to help split methane into clean hydrogen and graphite.
“Importantly, it drives down the process temperature to between 800-900 degrees Celsius,” Corrie said.
“That’s important because all the other pyrolysis technologies in this space are using the same reaction above 1500C sometimes even in excess of 2000C.
“You can immediately see the advantage that we have relative to others because we are less energy intensive, less power requirement, less heat and much lower costs.
“We can deliver hydrogen in the US for about US$1/kg relative to Green, that’s at least seven times cheaper. That’s conservative as you are going to see green hydrogen numbers well in excess of US$10/kg.”
The production of graphite as a co-product is the other competitive advantage.
While pyrolysis technologies normally deliver a carbon black, graphite is an advanced carbon material that has a broad range of uses from lithium-ion batteries all the way down to asphalt bitumen. This includes water purification, steel making and advanced thermal energy storage.
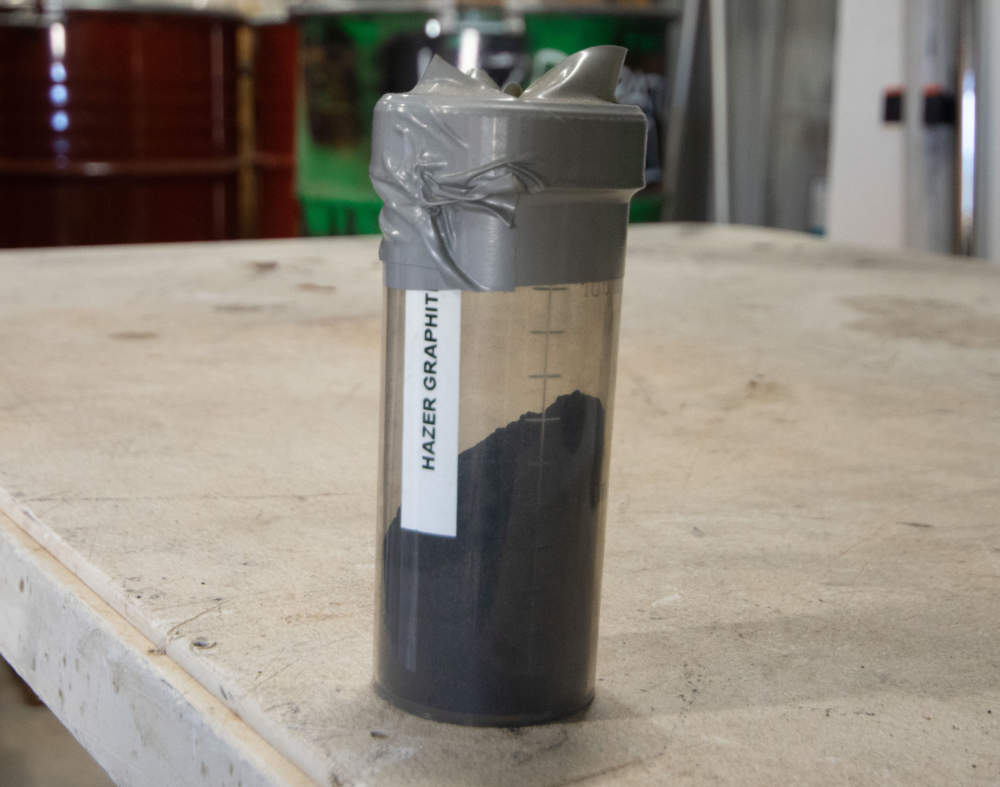
Hazer’s graphite co-product. Pic: Bevis Yeo
“We would envisage graphite prices anywhere between $500-600/t to over $1000/t,” Corrie added.
“So we achieve a clever, low-cost carbon capture and utilisation technology that has a valuable carbon product which is so much easier to dispose of than a gas.
“It is one technology that serves three markets, the hydrogen market, the carbon or graphite market, and industry decarbonisation market.”
He added that another advantage was being able to be plugged into existing infrastructure including the use of the same feedstock as SMR.
Clean hydrogen milestones
Looking ahead, Corrie noted that the company is currently focused on producing more graphite.
“To date, we have bagged over 2t, which is quite a lot of graphite, but we have prospective customers in Japan, Korea and other places that want large scale volumes to do some large-scale testing,” he said.
“We are on track to deliver commercial readiness this year. That’s a big gating item for some of our commercial projects including the Canada (FortisBC) project.”
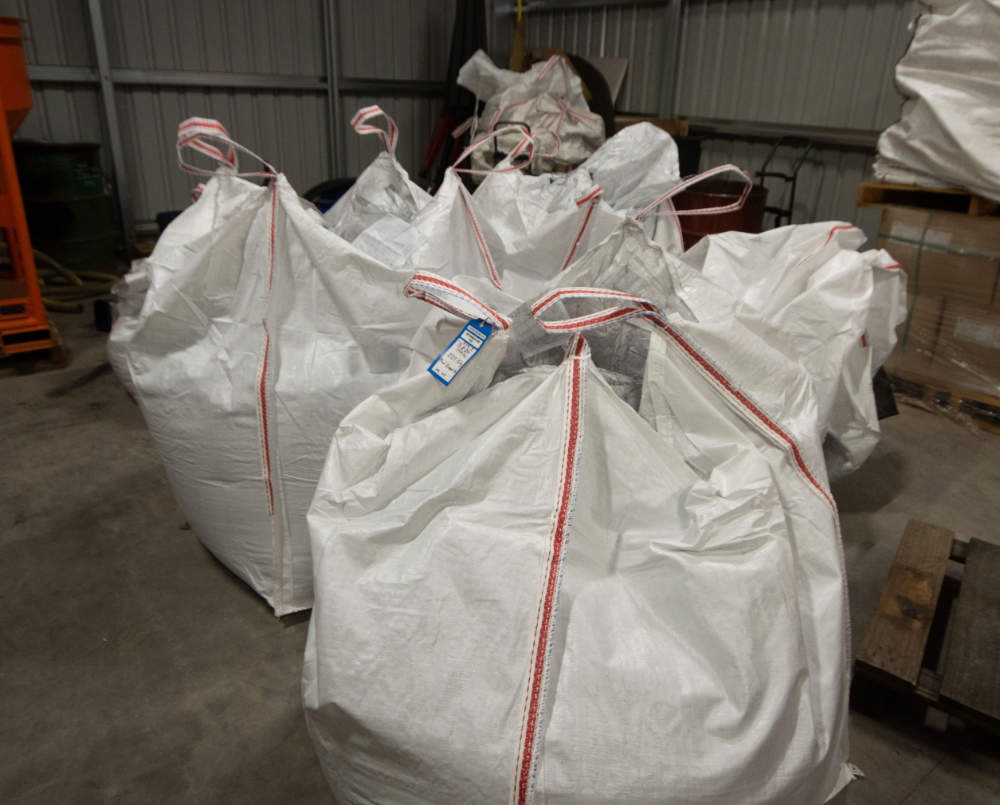
Bagged graphite at Hazer’s CDP (220kg per bag). Pic: Bevis Yeo
FortisBC is currently the most advanced of its partners with a final investment decision on a planned HAZER plant, which is 25 times the scale of the CDP, expected in the middle of 2025.
“The project has actually completed its initial FEED, which is quite an advanced step,” Corrie noted.
“Concurrently we have just signed a binding agreement with them to advance the project to the next phase and have agreed the commercial terms for the technology licensing and also agreed that Hazer will also be covered on past costs and future costs associated with our involvement in the project.
“This not only delivers a little bit of early operating revenue for us, it also shows that the project and partnership are moving forward commercially.
“We have a number of milestones between now and FID in terms of licence fees coming probably towards the end of this year and the completion of the FEED once the site is finalised.”
He added that FortisBC might not necessarily continue to be the front-runner as other customers also have their own commercial milestones.
“Corporately, we are in a really good position from a financial perspective, we raised earlier this year.
“We have a low-cost, and fully flexible business. Every year we get an attractive R&D refund, which is due again this half.
“We have got more ARENA funding milestones coming and we are in the running for some other federal and state opportunities as well, so there’s a pretty solid runway to some significant milestones for the company.”
This article was developed in collaboration with Hazer Group, a Stockhead advertiser at the time of publishing.
This article does not constitute financial product advice. You should consider obtaining independent advice before making any financial decisions.
Related Topics
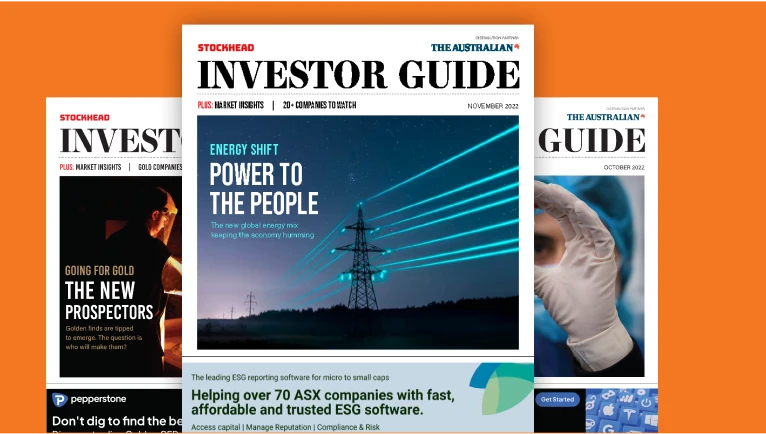
UNLOCK INSIGHTS
Discover the untold stories of emerging ASX stocks.
Daily news and expert analysis, it's free to subscribe.
By proceeding, you confirm you understand that we handle personal information in accordance with our Privacy Policy.