Supercharging mining: Using innovative tech to change the resources landscape
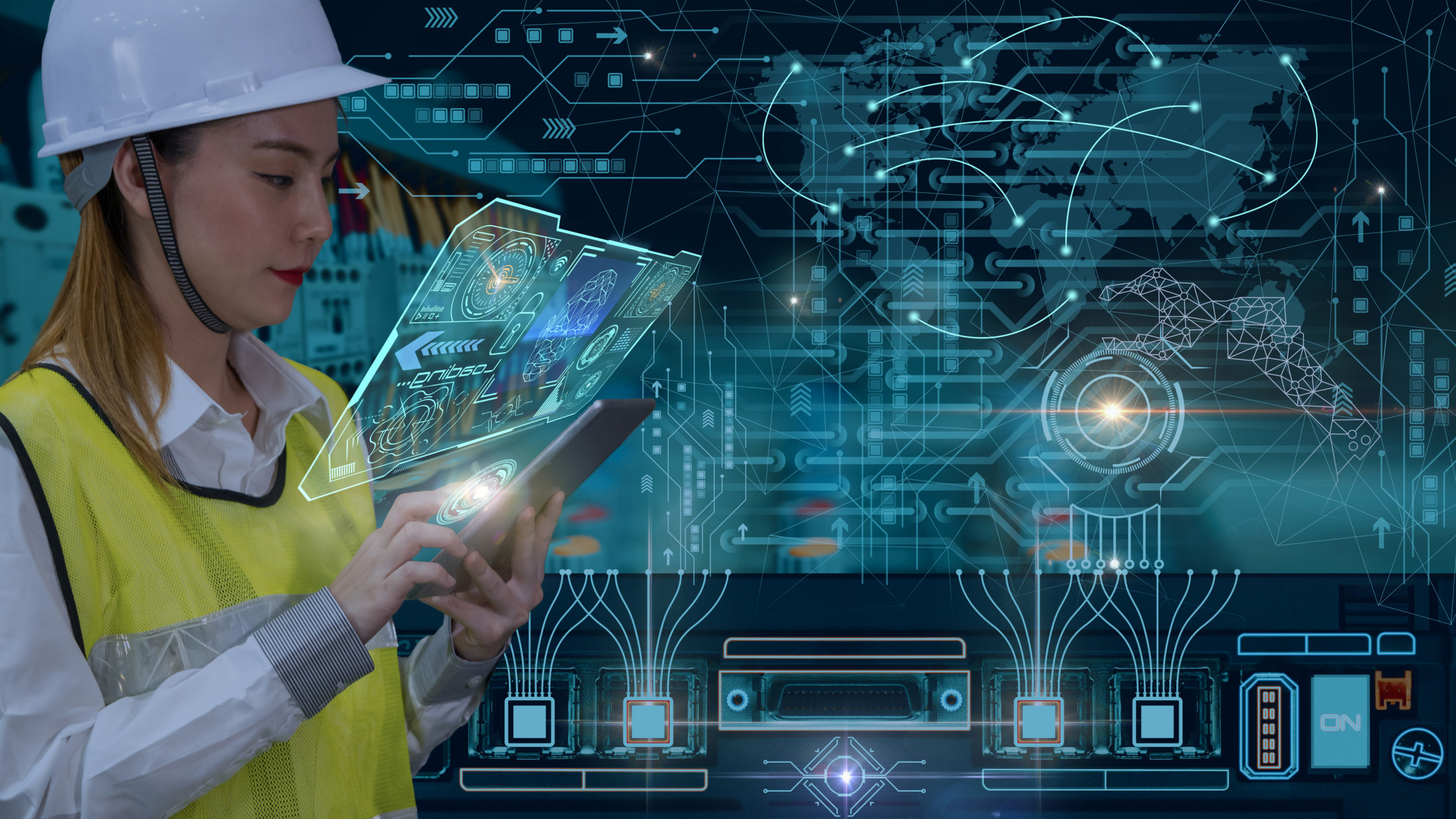
Pic: via Getty Images
Mineral processing breakthroughs have a history of completely disrupting the resources industry, making a style of mineralisation that was previously considered uneconomic, economic.
Consider copper, where the last major metallurgical breakthrough occurred in the mid-1980s with the introduction of Solvent extraction and electrowinning (SX-EW) which allowed copper producers to mine and extract copper from low-grade oxide deposits for the first time.
The industry maintained a deep inventory of such deposits but neglected them because traditional flotation technology yielded poor copper recoveries – but SX-EW enabled copper miners to get these deposits into production economically.
A similar technological revolution happened with pig nickel (a cruder form of pure nickel) back in the day, when nickel processing was extremely expensive and the metal used to make everything from kitchen utensils to aircraft quintupled in value to more than $50,000 a metric ton in mid 2007.
So, China’s Tsingshan developed a new, cheaper processing tech that transformed the industry.
The company found a way to use nickel pig iron from massive deposits in Indonesia, unleashing a low-grade substitute that helped send prices back below $10,000 just two years later.
With the bumper demand for battery metals expected for electric vehicles, Tsingshan is looking to shake up the industry again, this time turning pig nickel into a product as effective as pure nickel for lithium-ion batteries.
And if you take a look at lithium, current extraction techniques like evaporation ponds require lithium concentration to be high enough for the operation to be commercially viable – while also requiring vast amounts of land and water.
Innovation in the industry comes from players like American start-up Aether which uses molecular assemblers to extract lithium from previously untapped sources and using 50,000x less water than the amounts required in evaporation ponds.
It’s an extraction process that also eliminates the need for costly infrastructure that takes years to build, relying instead on portable, modular, shipping containers where the extraction and refinery occurs.
Kind of similar to Direct Lithium Extraction (DLE) where brine is pumped into a tank where ion exchange beads latch onto the lithium and then the remaining water is then released (sans lithium) back into the aquifer, meaning less of an environmental footprint for a project.
In all fairness though, DLE tech has been used in water treatment for decades but is now becoming popular for lithium players – although it’s yet to be proved on a commercial scale for lithium extraction.
Bridging the supply chain gap and creating $$ value
McKinsey says that improvements in processing technology, particularly for copper, could bridge supply chain gaps – and make miners a bunch of money (no-brainer really, right?).
“Three technological developments are gaining acceptance and scaling across the industry and can contribute meaningfully to bridging the supply gap: coarse particle recovery, sulphide leaching, and process optimization with machine learning,” McKinsey said.
If applied across the industry, coarse particle flotation could result in an additional 0.5 million to 1.5 million metric tonnes of annual copper production by 2032.
If applied across all metals found in sulphide deposits, the technology represents potential value creation of $9 billion to $26 billion per year.
Primary sulphide leaching could be a pathway to recover copper from material that is currently below mill head grade and considered waste – representing a $45 billion per annum opportunity across all sulphide-borne metals, McKinsey says.
And using machine learning to keep processing plants working consistently in the upper range of their capabilities could add 2-4% to metal recoveries and 5-15% to throughput.
“Such improvements offer an increase in global production from existing and planned mines of half a million to one million metric tonnes of refined copper by 2032, creating $9 billion to $18 billion in value per annum across all sulphide concentrators,” McKinsey said.
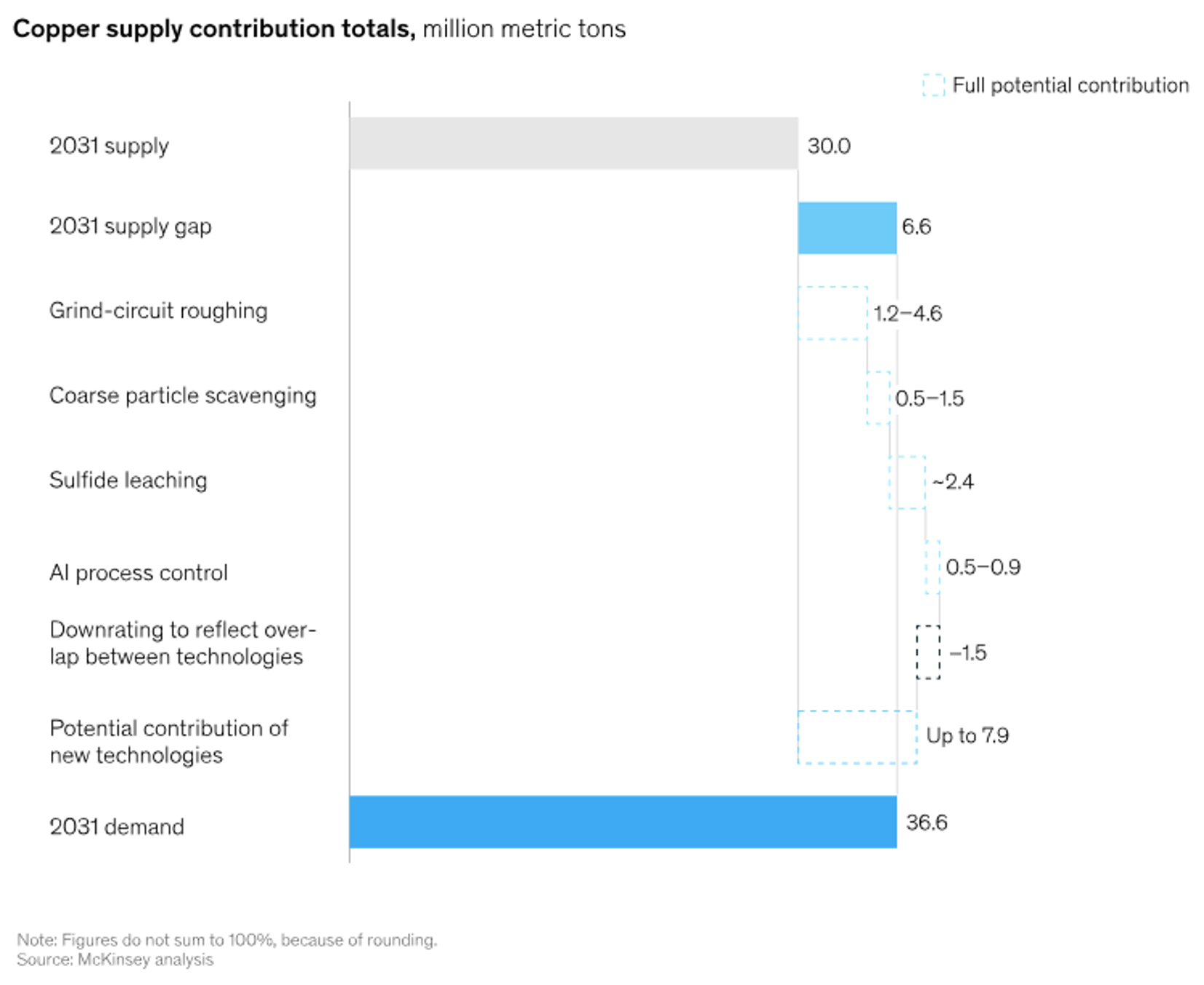
Miners increasingly turn to tech to boost processing
More and more companies are turning to innovative tech to improve processing. Earlier this year, BHP (ASX:BHP) and Microsoft teamed up to use artificial intelligence (AI) and machine learning to improve copper recovery at the world’s largest copper mine, Escondida, in Chile.
The project is expected to increase copper recovery by up to 5 per cent, which could generate an additional $1 billion in revenue for BHP each year.
Fellow mining giant Rio Tinto (ASX:RIO) uses the unique Nuton system which focuses on bioleaching to economically inlock copper bearing waste and tailings with more efficient water usage and lower carbon emissions.
Then there’s Jetti Resources which uses a catalyst-based system to leach primary sulphides for major miners.
Some resources companies are even developing their own tech, like Elevate Uranium (ASX:EL8) who’ve created a unique beneficiation process specially for uranium called U-pgrade – which could be a game-changer for production and project economics.
U-pgrade can sift out more than 95% of the mined ore mass before the leaching stage, producing a low-mass, high-grade uranium concentrate.
And since leaching is the highest unit cost operation of any uranium processing facility, lowering the mass to be leached has a huge impact, with the cost (both capital and operating) around 50% lower than conventional processing.
Global Lithium Resources (ASX:GL1) is another. It’s using multi-ore sorting separation technology to potentially increase concentrate production capacity at its Manna processing plant in WA by 20%.
So far test work showed the tech can upgrade low-grade pegmatite ore from 0.9% to 1.5% Li2O.
BHP, RIO, EL8 and GL1 share prices today:
Who are the tech stocks changing the processing game?
Each year global miners are estimated to lose >$2b worth of recoverable gold during processing, which Chrysos Corporation (ASX:C79) aims to defeat with its PhotonAssay tech developed by CSIRO.
The method, which has gained traction with major gold miners and drew famous Aussie mining services firm Ausdrill as an early investor five years ago, bombards drilling samples with X-rays to assess gold and other metal grades.
The company says the tech provides miners with access to real-time data, helping to improve decision making, enabling process optimisation to generate productivity gains (i.e. recover more gold).
Miners using the company’s tech include Barrick Gold, Ravenswood Gold and Novo Resources.
Zeotech (ASX:ZEO) is another player, with their invention associated with mineral processing technology for ‘treating a material’ is currently in the national phase of the patent granting procedure to protect and commercialise the IP.
It essentially converts a lithium process by-product (leached spodumene) to zeolites, which has potential as a tailings management solution and has already shown promise using feedstock from Covalent Lithium in its pilot plant.
Synthetic zeolites are known as molecular sieves and are made up of tiny pores that make them useful as adsorbents, catalysts and ultrafine filters.
Parkway Corporate (ASX:PWN) has innovative waste water treatment tech that deals with the extensive wastewater generation, including waste brines and acid & metalliferous drainage (AMD) from mining.
The company’s tech can convert waste brine into valuable industrial commercial products like caustic soda, agricultural lime, industrial salt and fresh water.
It’s also a problem with wastewater brine ponds from coal seam gas production, but that’s a story for another day.
RPM Global (ASX:RUL) has a suite of mining software products, including Product Optimiser, which determines the optimal way to process, blend and stockpile products to maximise value from what is scheduled to be mined and can be used for individual mining operations or multiple mines with shared processing facilities.
There’s also Plotlogic (unlisted) whose OreSense tech has already been picked up by some of the world’s largest miners including BHP, Glencore and Anglo American.
The tech combines hyperspectral, LiDAR and RGB imaging with artificial intelligence (AI), fusing huge amounts of data collected by a range of sophisticated sensors to produce extremely accurate, real time automated results.
It can be used to scan core, blasthole samples or even mounted on light vehicles to create digital maps of open pit and underground mine faces, draw points and stockpiles.
When mounted above the conveyor belt, the tech can accurately characterise materials – identifying deleterious materials or variance in ore quality and feed grade in real time.
This could mean big bucks. The company says an unnamed gold mine producing 1m tonnes of ore at 1.8g/t saw a $1.4m productivity bump with just a 1% increase in feed grade from 1.8g/t to 1.82g/t over one year.
C79, ZEO, PWN and RUL share prices today:
At Stockhead we tell it like it is. While Parkway, Plotlogic and Elevate Uranium are Stockhead advertisers, they did not sponsor this article.
Related Topics
UNLOCK INSIGHTS
Discover the untold stories of emerging ASX stocks.
Daily news and expert analysis, it's free to subscribe.
By proceeding, you confirm you understand that we handle personal information in accordance with our Privacy Policy.