From military aircraft to submarine parts – the ASX stocks at the forefront of additive manufacturing
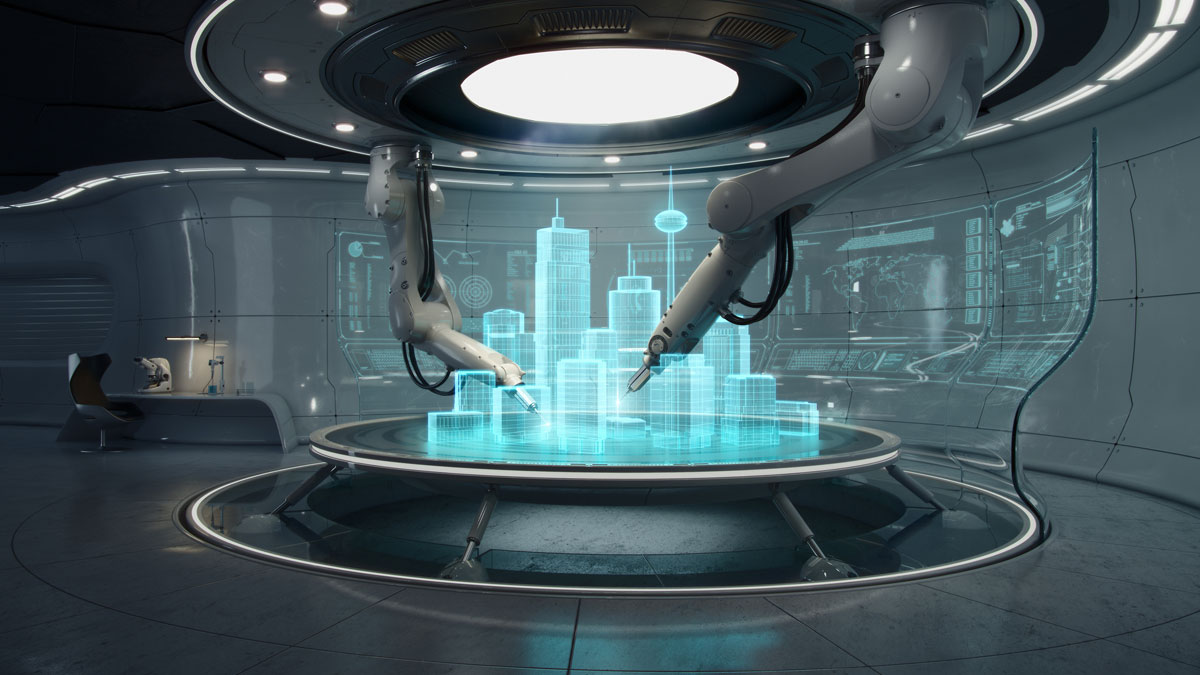
Picture: Getty Images
- Additive manufacturing poised for significant growth in coming years with CAGR of 20.8% from 2022 to 2032
- Securing supply chains, demand for prototyping and countries re-establishing sovereign manufacturing driving growth
- Several ASX listed additive manufacturing companies are finding success both in Australia and abroad, including the US
Additive manufacturing is the fancy industrial name for 3D printing, which encompasses a computer-guided industrial fabrication method that constructs three-dimensional objects through the gradual accumulation of materials in successive layers.
Additive manufacturing is poised for significant expansion in the upcoming years with the global market size estimated at US$13.84 billion in 2021 and a compound annual growth rate (CAGR) of 20.8% from 2022 to 2030.
Demand for prototyping applications across diverse sectors and industries including healthcare, automotive, aerospace and defence, along with increasing research and development efforts in the field of 3D printing, are major drivers of the market’s expansion.
Furthermore, the ability for additive manufacturing to help companies take control of their supply chain, producing parts where and when they need them is further propelling growth of the industry.
Specialising in additive printing Titomic (ASX:TTT) head of sales and marketing Dominic Parsonson told Stockhead additive manufacturing has particularly risen to prominence in recent years following supply chain disruptions.
“Although the idea for decentralised manufacturing has been around for a long time, the last three years with the Covid-19 pandemic, geopolitical stressors in the Asia Pacific and war in Ukraine has really highlighted to organisations that additive manufacturing has real value,” he says.
AML3D (ASX:AL3) interim CEO Sean Ebert also told Stockhead additive manufacturing is playing a key role in helping to re-establish Australia’s sovereign manufacturing capability and mitigate supply chain risk.
He says other countries like the US, a key market for AL3, is also looking at improving their sovereign manufacturing capability.
“In May last year the Biden administration launched its Additive Manufacturing Forward initiative, or ‘AM Forward’, to drive the adoption of 3D printing within the US manufacturing base,” he says.
“In the US AML3D’s metal 3D printing technology is seen as a way to increase the resiliency and competitiveness of America’s supply chains.
“Their view is additive manufacturing will give companies the ability to make and sell higher-performing parts, shorten lead times for needed parts, increase workers’ wages, and expand access to better products.”
Back home, Parsonson says Australia has large reserves of the precursor feedstock for titanium production, known as titanium mineral sands, positioning it well to take advantage of downstream manufacturing opportunities as well as upstream exploration and mining.
Titanium is often considered superior to both steel and aluminium in many applications because of its durability, reduced weight and strength.
However, titanium is cost-prohibitive to manufacture using traditional methods of casting and forging. Parsonson says the rise of additive manufacturing is enabling manufacturers to use highly desirable metals such as titanium.
“The reason Titomic exists is our big goal or intention was to build enough of a titanium industry in Australia that would encourage the government or a major mining company to start processing titanium rather than shipping it overseas,” Parsonson says.
“We dig all of our titanium mineral sands out of the ground in Australia and ship it off overseas to get converted into titanium and then companies like ourselves buy it back which is a little bit sad.
“But if more manufacturing companies like Titomic and more companies like our customers say we get value out of this low-cost method of producing finished goods from titanium, it might spark a whole new demand down the line.”
Parsonson says despite our small size with ~25.5 million people, Australia has a relatively strong position globally with small innovative additive manufacturing companies. Here are some of the additive manufacturing stocks on the ASX we’ve noticed.
Titomic
With it head office and manufacturing facilities in Melbourne along with a European office and factory in the Netherlands, TTT has been working with the CSIRO to develop its Kinetic Fusion technology employing innovative near-net-shape manufacturing and cost-effective materials to create large-scale titanium and other alloy parts.
Parsonson says the approach minimises waste, boosts efficiency, and reduces costs, serving as a compelling alternative to traditional forging and casting.
He says the Kinetic Fusion process uses supersonic particle deposition to establish robust bonds between metal particle layers, resulting in highly durable components with exceptional mechanical properties, suitable for diverse applications.
“We’ve taken technology that is 25 or 30 years old, and five years ago together with the CSIRO decided this tech could be very useful in additive manufacturing and was exceptionally valuable,” Parsonson says.
“We’ve spent the past five years optimising the performance and making sure it does what we expect it to do and promoting it to the market.”
Parsonson says a key advantage of Kinetic Fusion is its versatility with raw materials, including economical titanium, enabling enhanced part performance while maintaining cost competitiveness.
The Kinetic Fusion technology finds practical use in producing complex aerospace, defence, and mining components.
“We build additive manufacturing machines which we sell around the world via our resellers and sister companies as well as make parts for customers who want to explore additive manufacturing but aren’t ready to own machines,” Parsonson says.
“Where there is value we also set up joint ventures to do ongoing production of specialised parts.”
The Kinetic Fusion tech has produced lightweight doors, cost-effective radiation shielding, gun barrels, invar tooling faceplates, and automated glass mold coatings, showcasing its versatility.
AML3D
AL3’s patented Wire Additive Manufacturing (WAM) process is at the heart of its ARCEMY industrial metal 3D printing systems.
The WAM process combines welding science, robotics automation, materials engineering and proprietary software to design and 3D print industrial scale metal components.
Ebert says its ARCEMY systems have several advantages over traditional manufacturing processes.
“We can provide automated, on-demand, industrial 3D manufacturing solutions at the point-of-need that are more efficient, cost-effective and deliver better ESG outcomes when compared to traditional casting, forging and billet machining processes,” he says.
AL3 has won a number of significant manufacturing contracts with the US Department of Defence. Its share price recently bounced 22% after announcing a $2 million contract to manufacture high demand components for US Navy submarines.
“As a result, right now, demand for additive manufacturing technology in the US, by far, outstrips other markets and as the global leader in the supply of advanced, industrial scale, metal 3D printing technology AML3D is focused on meeting that demand,” Ebert says.
He says the company’s tech can design and print the industrial scale components needed within the US Defence sector and, in particular, the US Navy’s submarine industrial base.
“We can do that faster and better, using a proven technology that has been accredited by the leading global standards agencies, Lloyds Register and DNV.
“A case in point is we are currently working on designing and printing a submarine part that is no longer available from the original US manufacturer.
“Add to that the US is ramping up its submarine manufacturing to meet the requirements of the AUKUS alliance, which is driving demand from the US navy submarine industrial base.”
Ebert says it just makes sense for AML3D to focus on the US market, where it is seeing the greatest demand for our technology.
“As Australia progresses along the additive manufacturing journey we expect greater demand to emerge here and for AML3D’s technology to deliver similar benefits,” he says.
Amaero International (ASX:3DA)
Founded in 2013, 3DA emerged to bring to market advancements in additive manufacturing of metals and alloys, stemming from innovations developed at Monash University.
The company is focused on production of titanium and specialty alloy powders and their use in advanced manufacturing applications across aerospace and defence, medical, and various other industries.
With recent expansions encompassing both machinery and alloy offerings, 3DA now delivers comprehensive end-to-end solutions for the additive manufacturing of metal components.
Its services encompass design, manufacturing, and materials provision. 3DA continues to collaborate with the Monash Centre for Additive Manufacturing (MCAM) in the areas of materials science, alloy design, metal 3D printing, and surface engineering.
As part of its growth strategy, 3DA is developing its flagship titanium project in the US. The company’s powder manufacturing, research and development and corporate headquarters will be located at 12,100m2 purpose-built facility in Tennessee. Equipment installation is expected to start in July 2024.
Aurora Labs (ASX:A3D)
Perth-based A3D kicked off manufacturing and testing of its flagship AL250 commercial laser powder bed fusion printer earlier this year.
A3D says the printer’s material paramaters were optimised for low power and 1500W printing to deliver printed material quality compliant with industrial and aerospace standards – with those sectors the company’s main marketing focus.
The company has received positive test results for its qualification print for Woodside Energy Technologies Pty Ltd, for a variety of stainless steel 316L artifacts and test samples produced on its beta machine and according to Woodside’s engineering standards for additive manufacturing.
A3D were then tested by a NATA certified lab and included mechanical and corrosion tests, along with visual analysis using optical and scanning electron microscope (SEM) microscopy.
The company says testing results showed that A3D can print SS316L consistent with the material properties required.
A3D is also expanding engagement across Australian universities to open up industry-based research opportunities to strengthen the domestic AM sector.
The TTT, AL3, 3DA & A3D share price today:
Related Topics
UNLOCK INSIGHTS
Discover the untold stories of emerging ASX stocks.
Daily news and expert analysis, it's free to subscribe.
By proceeding, you confirm you understand that we handle personal information in accordance with our Privacy Policy.