Environmental Clean Tech receives India patent for innovative HydroMOR ironmaking process
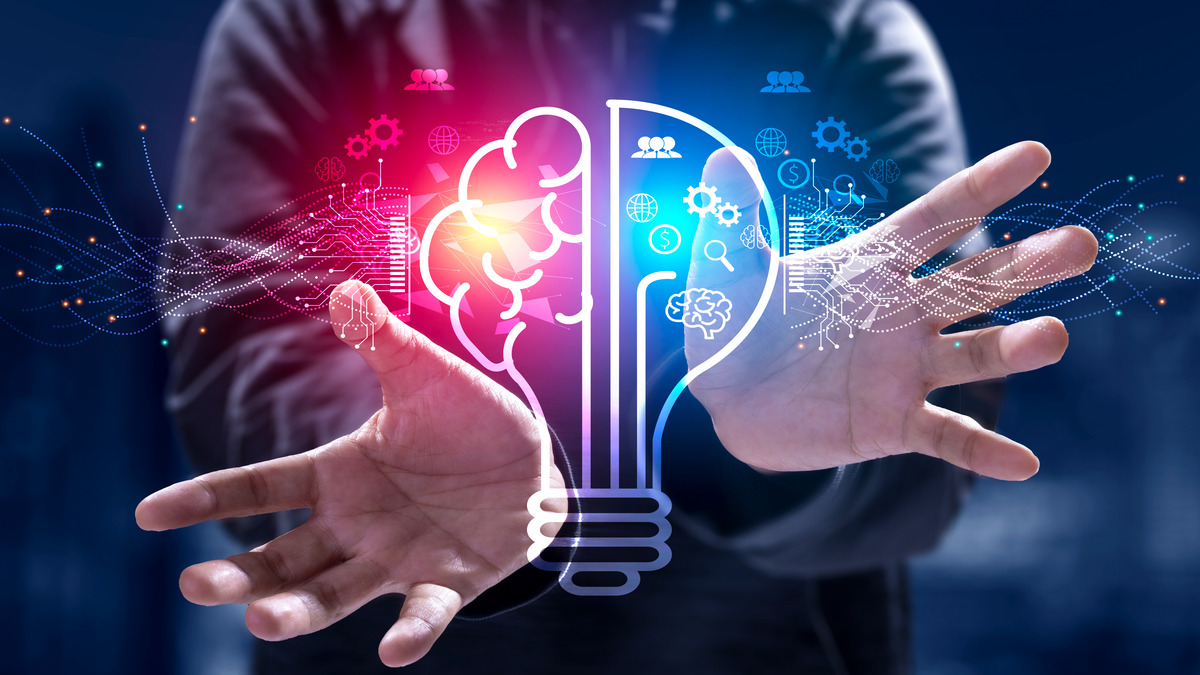
ECT’s HydroMOR tech using brown coal is set to provide a cost-effective, low-carbon emission solution to the steel-making industry. Pic via Getty Images.
- HydroMOR ironmaking patent expands into India, the world’s largest populous
- The tech uses cost-effective brown coal instead of coking coal for steelmaking
- Trials show a 30% reduction in CO2 emissions
Special Report: Environmental Clean Technologies, with its HydroMOR process, is looking to deliver cost-effective, low-carbon emission solutions to the steelmaking industry. It has just received a patent grant in India for its sustainable tech.
The news bolsters Environmental Clean Technologies’ (ASX:ECT) growing portfolio of patents for the tech which has already been granted in Australia, the EU, Hong Kong, Russia, and Canada.
The steel industry is responsible for ~8% of our world’s CO2 emissions. That’s where ECT’s tech comes in.
Traditionally, lignite, a soft, brown coal, is incompatible with conventional steelmaking processes.
ECT’s HydroMOR process harnesses the material and offers a low-carbon emission alternative to traditional, high-emission blast furnace steelmaking that predominantly uses expensive and polluting coking coal.
HydroMOR: A sustainable steelmaking solution
HydroMOR employs a unique hydrogen-based reduction pathway within a proprietary furnace design. This design allows for the efficient use of lower-grade and waste iron ore sources, resulting in a more sustainable and cost-effective steel production method with ~30% lower emissions.
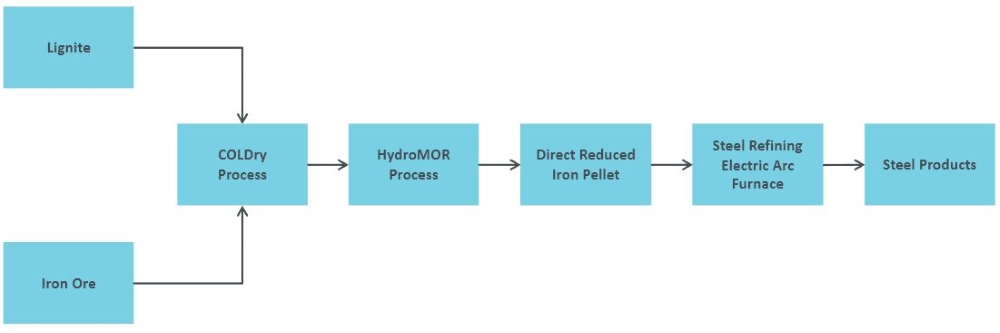
The HydroMOR process. Pic supplied: (ECT)
HydroMOR v Traditional methods
While hydrogen-based iron ore reduction is not a new concept, adoption has been hindered by the lower cost of coal, lack of regulations on carbon emissions, and the high cost of upgrading infrastructure for hydrogen-based direct reduced iron (DRI).
Green steel production using green hydrogen offers a path to decarbonisation, but the process remains energy-intensive and expensive.
HydroMOR stands out by not only rivalling blast furnaces in terms of cost but also achieving significant reductions in CO2 emissions.
Key economic benefits of HydroMOR include 30-40% lower capex, 10-15% lower opex, and a whopping 70% reduction in raw material costs.
There are also all-important environmental benefits, with ECT demonstrating a 30% reduction in CO2 emissions and the utilisation of low-grade waste resources, which reduce tailings and fines – not to mention less land and water use and lower maintenance.
The road ahead
ECT is currently engaged in early discussions with potential partners for projects considering HydroMOR for direct-reduced iron (DRI) production.
The innovative process, the company says, has the potential to deliver a near-term decarbonisation solution to the steel industry, paving the way for a more sustainable future.
This article was developed in collaboration with Environmental Clean Technologies, a Stockhead advertiser at the time of publishing.
This article does not constitute financial product advice. You should consider obtaining independent advice before making any financial decisions.
UNLOCK INSIGHTS
Discover the untold stories of emerging ASX stocks.
Daily news and expert analysis, it's free to subscribe.
By proceeding, you confirm you understand that we handle personal information in accordance with our Privacy Policy.