Altech to expand Silumina project output to 120Gwh, enough to outfit 400 Victorian big batteries
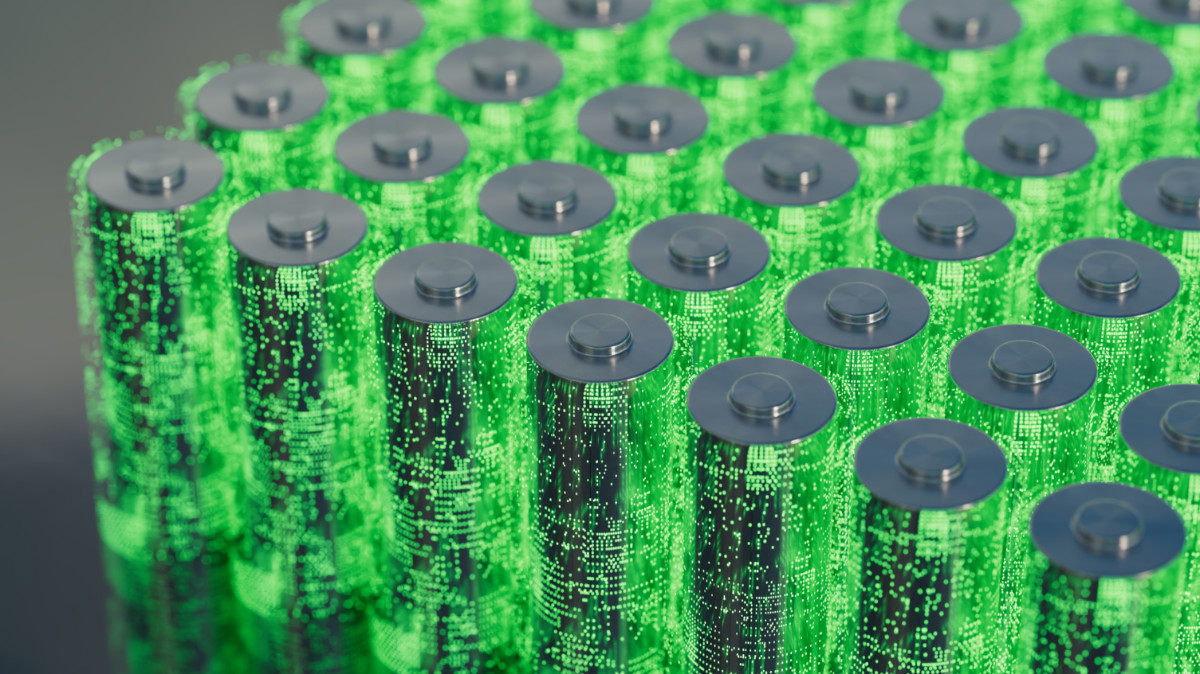
Altech will expand Silumina project output eightfold, from 15 GWh to 120 GWh. Pic via Getty Images
- Altech Batteries changes focus of Silumina project DFS to 8,000tpa of alumina-coated metallurgical silicon anodes
- As a result of this increased production of the ‘active’ component, output has expanded, rising from 15 GWh to 120 GWh
- Altech is currently in talks with Ferroglobe, the European silicon partner of Altech, to boost the supply of metallurgical silicon
Special Report: Altech Batteries has increased the Silumina project DFS output eightfold from 15 GWh to 120 GWh to produce 8,000tpa of alumina-coated metallurgical silicon for the electric vehicle market.
Altech Batteries (ASX:ATC) is angling to grab a piece of the EV pie with its Silumina Anodes product, which incorporates high purity alumina coated silicon and graphite into the anode of lithium ion batteries.
The lithium-ion battery market is expected to grow at a compound annual growth rate of 26% over 2020-25, and represents a lucrative opportunity for the company.
Its ability to achieve 30% higher energy capacity with the addition of silicon into the anodes makes for a meaningful competitive edge.
Altech’s magic ingredient is the use of its proprietary HPA coating technology with regular battery-grade graphite to produce a lithium-ion battery with a composite graphite/ silicon anode, which has 10 times the capacity of graphite only anodes.
This means when incorporated into a lithium-ion battery, the result is a battery with higher energy retention capacity by volume and weight meaning smaller, lighter batteries for the EV market.
DFS focus switches to “all silicon”
Altech has been powering towards the completion of a DFS at its Silumina Anodes Pilot Plant in Saxony, Germany.
The DFS initially proposed the production of 10,000tpa of Silumina anode product, comprising 1,000tpa of high-purity alumina coated metallurgical silicon incorporated into 9,000tpa of similarly coated graphite (10% mix).
But the focus has now changed.
The plant will solely focus on producing alumina-coated metallurgical silicon product at a rate of 8,000tpa and will be integrated into the graphite by the customers within their battery plants rather than at Altech’s facility in Germany.
As a result of this increased production of the ‘active’ component, the output has expanded eightfold, rising from 15 GWh to 120 GWh – enough to outfit 400 Victorian big batteries, a 300 MW grid-scale battery project.
Boost to bottom-line economics
Altech says the move to ‘all silicon’ is expected to yield substantial improvements in the bottom-line economics.
The most notable advantage lies in the ability to crack the silicon code, preventing expansion defragmentation, as well as curbing the significant first-cycle loss associated with silicon.
Battery manufacturers have the choice to either produce batteries with higher energy density or maintain their current energy density while reducing the graphite content. By decreasing the use of graphite, the cost of producing batteries can be reduced.
What’s next?
Altech is currently in talks with Ferroglobe, the European silicon partner of Altech, to boost the supply of metallurgical silicon for the Silumina project.
It has executed non-disclosure agreements (NDAs) with prominent automotive conglomerates in Europe and the United States, who have shown keen interest in acquiring commercial samples for their testing and qualification procedures.
Considering the limited production capacity of Altech’s R&D laboratory in Perth, the larger samples will be procured from the Silumina anodes Pilot Plant in Saxony.
The pilot plant is nearing completion and is expected to be operational in the early part of 2024.
This article was developed in collaboration with Altech Batteries, a Stockhead advertiser at the time of publishing.
This article does not constitute financial product advice. You should consider obtaining independent advice before making any financial decisions.
Related Topics
UNLOCK INSIGHTS
Discover the untold stories of emerging ASX stocks.
Daily news and expert analysis, it's free to subscribe.
By proceeding, you confirm you understand that we handle personal information in accordance with our Privacy Policy.