Sparc’s graphene additives improve anti-corrosion performance by 62pc
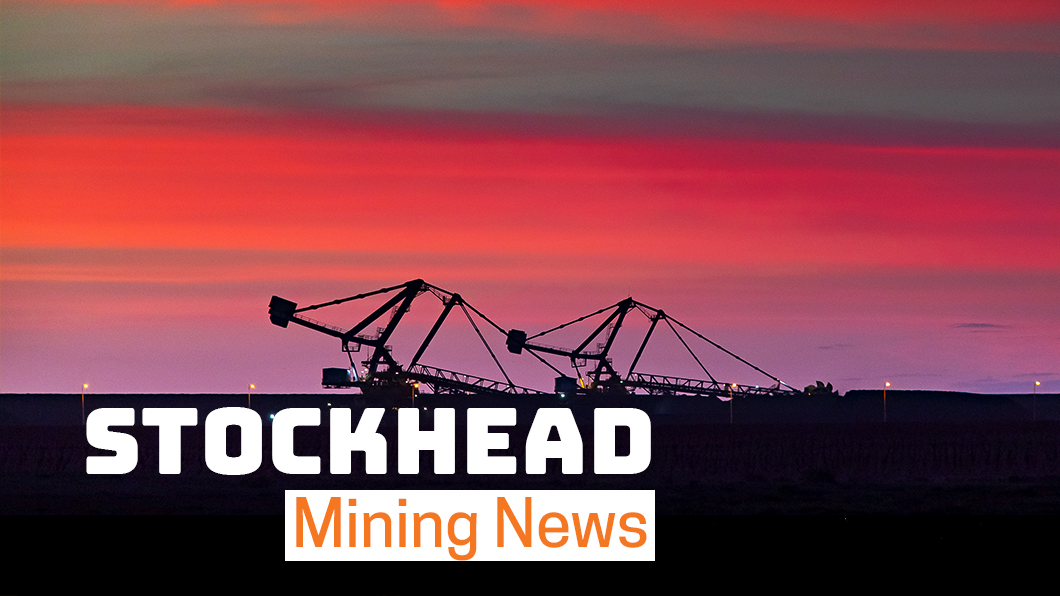
Pic: Bloomberg Creative / Bloomberg Creative Photos via Getty Images
Test work has demonstrated the excellent potential of Sparc’s graphene-based additives to improve the performance of anti-corrosion coatings.
It is not hard to see why, given that the testing of leading commercially available coatings products enhanced with the proprietary additives has returned a 62 per cent improvement in anti-corrosion performance.
This test was carried out over 1,344 hours on smooth cold-rolled steel that provides standardised results for direct implementation.
Sparc Technologies (ASX:SPN) says the results confirm the significant commercial applicability of its graphene additives for the world’s leading coatings products used in industrial applications, marine environments and global shipping
“Once again Sparc’s proprietary graphene coatings technology demonstrates its superior ability to substantially improve the corrosion performance of commercially available coatings,” chief executive officer Mike Bartels.
“These results will provide an enormous benefit to our continued discussions with the global coatings companies that are looking to commercialise our coatings technology.
“Furthermore, Sparc is undertaking graphene test work on 12 separate coatings projects and the ongoing anti-corrosive work program will benefit our optimisation work in other coatings projects such as antifouling, anti-bacterial, anti-viral and drag resistance.”
Test work
Sparc’s graphene additives were added to commercially available epoxy coatings, from leading global coatings companies. They were applied to smooth cold-rolled steel panels, which are a far more challenging environment compared to previous work on abrasive blast-cleaned steel.
These panels and controls with no graphene additives were subjected to 1344 hours of salt spray under controlled conditions.
Carried out on non-standard substrate, the work approximates the requirements of ISO12944-6 for high durability in aggressive environments and was intended to amplify observable differences in corrosion performance between the various samples evaluated.
This article was developed in collaboration with Sparc Technologies, a Stockhead advertiser at the time of publishing.
This article does not constitute financial product advice. You should consider obtaining independent advice before making any financial decisions.
Related Topics
UNLOCK INSIGHTS
Discover the untold stories of emerging ASX stocks.
Daily news and expert analysis, it's free to subscribe.
By proceeding, you confirm you understand that we handle personal information in accordance with our Privacy Policy.