EcoGraf takes first step in decarbonising steel-making process
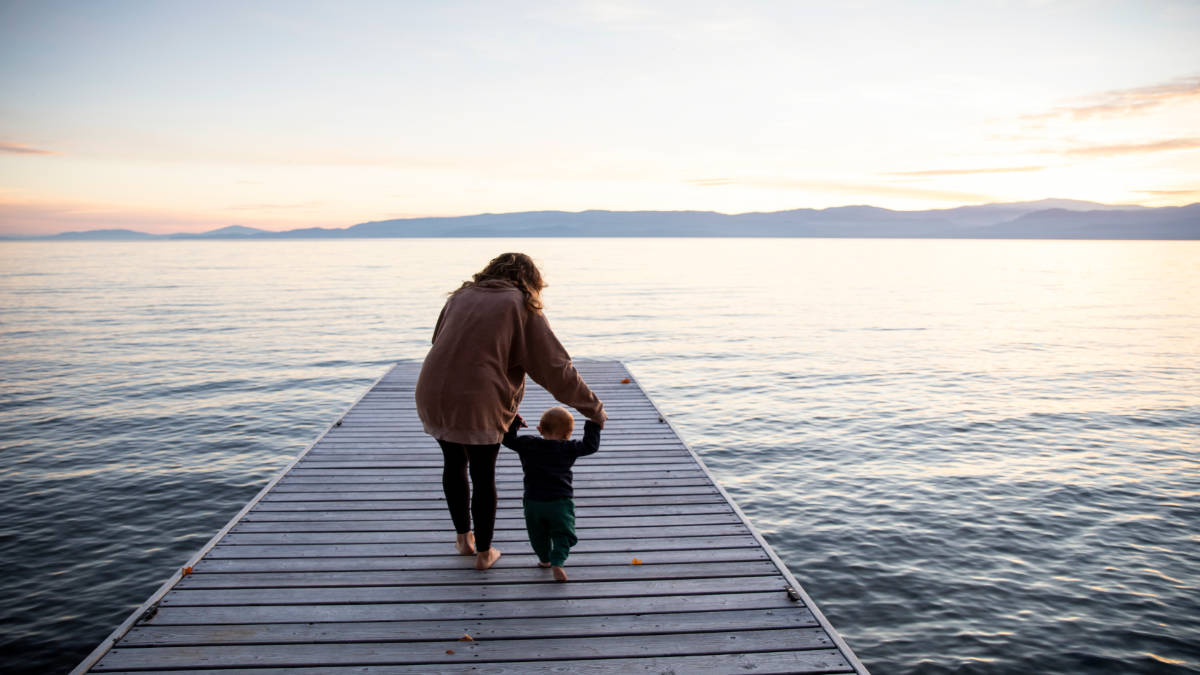
Pic: Getty
Tuesday wasn’t the best of days for good news, as Stockheader Sam Jacobs put it – local markets executed a proper face-plant as the microcap Emerging Markets index slumped by 5.03%.
But in an exciting move, ASX-lister EcoGraf (ASX:EGR) revealed how it is looking to drastically reduce the level of emissions associated with the production of steel.
The company announced the first GreenRECARB products had passed the specification test for use as an environmentally ‘superior’ replacement for petroleum coke furnace additives.
Petroleum coke furnace additives are associated with high carbon emissions, as well as polluting materials such as sulphur and nitrogen. However, EGR managing director Andrew Spinks says by using natural graphite as a feedstock, carbon emissions are substantially reduced.
This comes at a time when steel manufacturers continue to seek more sustainably produced additive materials to replace the use of energy intensive, fossil-fuel based calcined petroleum coke products.
“Our material comes from natural graphite, it’s pure carbon, and there are lower impurities compared to existing coke products used to increase the carbon content of steel,” Spinks said.
“It is also a by-product through the manufacturing of purified spherical graphite at our planned battery anode material facility in Western Australia.
“So at the moment we have developed a flow sheet to create this recarburiser product as a green alternate carbon additive material for the steel industry, which is the critical first step and we have developed a product specification material data sheet and product samples for our customers,” he said.
Key advantages of GreenCARB include its high purity with reduced sulphur and nitrogen levels, improved carbon absorption efficiency, and low emission manufacturing process compared to existing coke products, which ultimately reduces the carbon footprint of the steel manufacturing process.
“If our customers accept the material, EcoGraf will move forward to a detailed engineering design to incorporate in our battery anode materials facility in Western Australia.”
With the steel manufacturing industry being one of the highest polluters, he said he hopes greenRECARB will play an important role in the push towards ‘green steel’.
Market opportunity of up to 1Mt of recarburiser each year
This work represents the initial phase of the EcoGraf GreenRECARB program, which consisted of bench scale formulation of optimum binding, granulation and pelletisation processes to produce a cost-effective and environmentally superior recarburiser product for steel manufacturers.
Recarburisers are carbon materials that are typically used to adjust the carbon content of steel before it is still in liquid form with EcoGraf’s GreenRECARB products used in electric arc and induction furnace steel manufacturing processes.
Electric arc furnace steel production currently accounts for 30% of the global steel market and requires a minimum of 3-4% recarburiser additive, providing a market opportunity of up to 1Mt of recarburiser each year.
Importantly, the high carbon absorption efficiency of natural crystalline graphite additives in both electric arc and induction furnace steel manufacturing processes is expected to increase the operating efficiency of these furnaces and lower steel production costs.
Data obtained from the process flowsheet and pelletiser manufacturing route for the GreenRECARB production program will be used for initial engineering design works in parallel with the customer testing program.
Related Topics
UNLOCK INSIGHTS
Discover the untold stories of emerging ASX stocks.
Daily news and expert analysis, it's free to subscribe.
By proceeding, you confirm you understand that we handle personal information in accordance with our Privacy Policy.