Eagle Mountain scales new heights at Oracle Ridge with a simpler processing method to produce LME grade copper
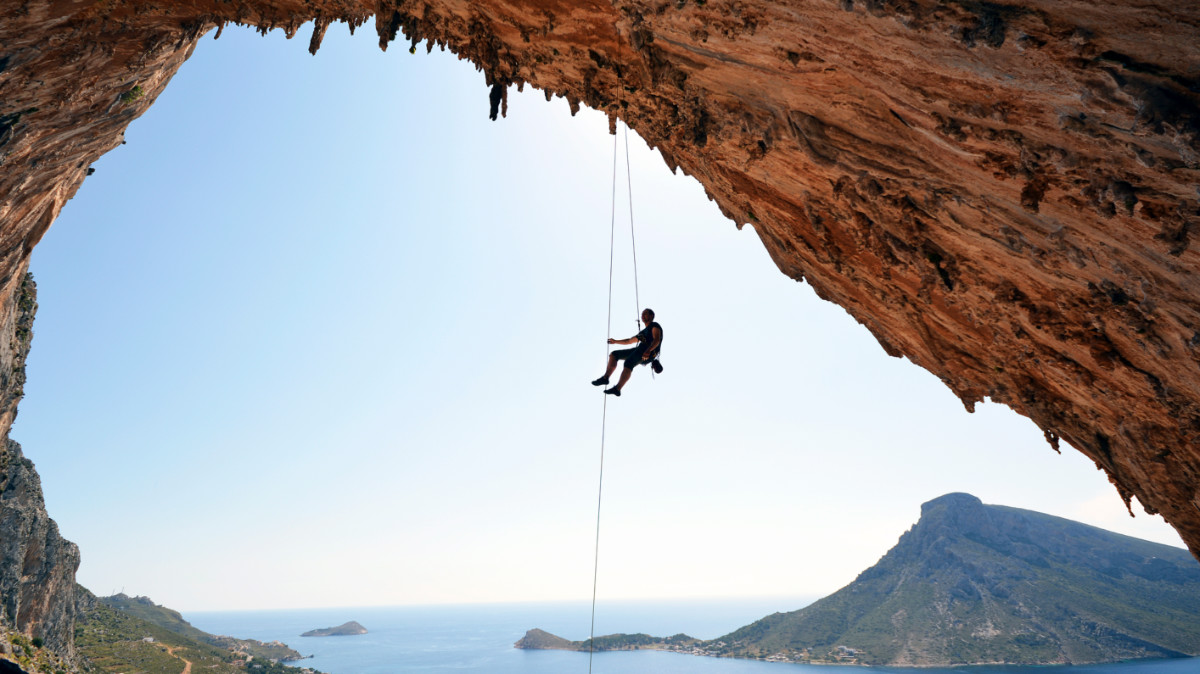
Eagle Mountain Mining has identified a simplified process flowsheet for its Oracle Ridge copper project in Arizona. Pic via Getty Images
- Eagle Mountain has identified a simplified process flowsheet involving production of LME grade copper on site at Oracle Ridge in Arizona
- This option offers the potential for lower capital and operating costs compared to conventional mining and processing, as well as a reduced environmental footprint
- Glycine leaching is currently being tested on run-of-mine ore and low-grade material, the next stage will be testing the rougher concentrate and the existing tailings
Special Report: Eagle Mountain Mining has identified a simplified process flowsheet for its Oracle Ridge copper project in Arizona, offering the potential for lower capital and operating costs.
November marked a month of milestones for Eagle Mountain Mining (ASX:EM2) at Oracle Ridge with highlights including an updated resource of 28.2Mt at 1.35% copper for 380,000t contained copper on the fourth anniversary of acquiring the project.
Recent work has largely focused on extensional, infill and upgrade drilling since EM2’s first major exploration program at Oracle Ridge in September 2020.
But the momentum isn’t slowing down yet.
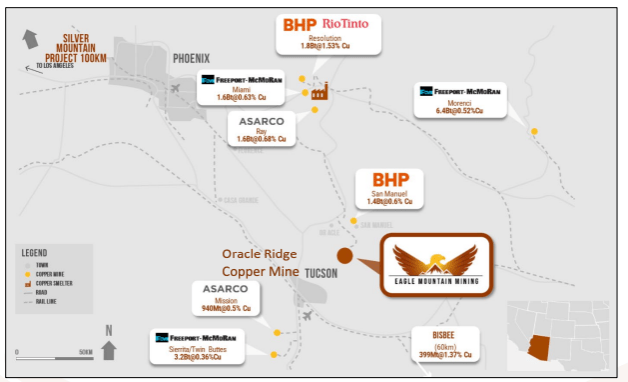
A range of metallurgy and comminution results have been received supporting a simplified flowsheet to produce copper on site at Oracle Ridge via leaching, solvent extraction and electrowinning.
Thanks to the work conducted on the recent resource, EM2 says the mineralisation is much more continuous using lower cut-offs which support the potential for larger stopes.
The most suitable mining method will be long-hole open stoping with multiple mining fronts allowing higher production rates and backfill to be incorporated, which may include paste fill, waste rock or reclaimed heap leach material.
As large portions of the mineralisation are above the current portal, EM2 plans to use a battery-powered mobile fleet, with the added benefit of reduced emissions and ventilation costs within the mine.
Keeping it simple delivers the goods
While the production of a bulk concentrate remains an option for the project via a conventional mining and processing route, a simplified flowsheet has been identified that avoids smelting and refining beyond the mine gate.
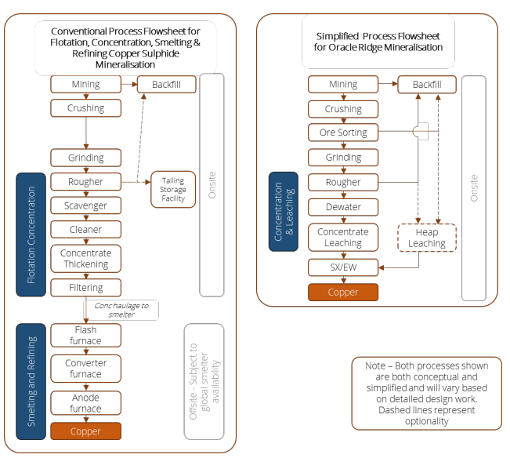
Benefits of a bulk concentrate include potentially lower capital and operating costs, the avoidance of downstream transport and processing, reduced environmental impact potentially derived from smelting, and the security of copper supply for US domestic consumption.
Long-term expectations are that copper will fall into big deficits from the latter part of this decade as green demand rises and miners struggle to expand operations or develop new ones unless prices rise substantially.
Improved plant infrastructure for strong metal recoveries
During the early 1990s, a bulk copper, silver and gold concentrate was produced on site using a standard flotation circuit and sold to a nearby smelter.
Smelter records at the time showed consistent high-grade concentrate, in excess of 26% copper with payable gold and silver credits as well as no deleterious penalty element.
But the recovery was not optimum as there was reportedly up to 50% scat recirculating load which impacted processing.
EM2 says this suggests that with improved plant infrastructure (such as appropriate crushers, including a pebble crusher), strong metallurgical recoveries can be achieved while also producing high-grade concentrates.
Its borehole sampling of the historical tailings average just under 0.3% copper with one sample over 1.0% copper. This suggests sub-optimum recovery in previous operations, according to EM2.
Glycine leach testwork on part of these tailings will soon commence to identify whether they can be reclaimed via vat leaching.
Ore sorting test work has demonstrated a 30% increase in copper head grade – made possible by the removal of lower grade ore or waste material – has the potential to deliver lower capital and operating costs due to a reduction in grinding requirements.
On the path of becoming a mid-tier copper producer
“I’m very excited that our team has identified a far simpler processing method for mineralisation at Oracle Ridge,” EM2 CEO Tim Mason says.
“Excellent copper recovery from rougher flotation alone paves the way for direct tank-leaching of the concentrate which in turn feeds to an SX/EW plant onsite that produces LME grade copper sheet.“
There is no need for filtering and shipping of concentrate to smelters and refiners.
“Glycine leaching is currently being tested on run-of-mine ore and low-grade material but results received to date are very encouraging and the next stage will be testing the rougher concentrate and the existing tailings.
“These latest developments support our goal to become a mid-tier copper producer in the USA.”
This article was developed in collaboration with Eagle Mountain Mining, a Stockhead advertiser at the time of publishing.
This article does not constitute financial product advice. You should consider obtaining independent advice before making any financial decisions.
Related Topics
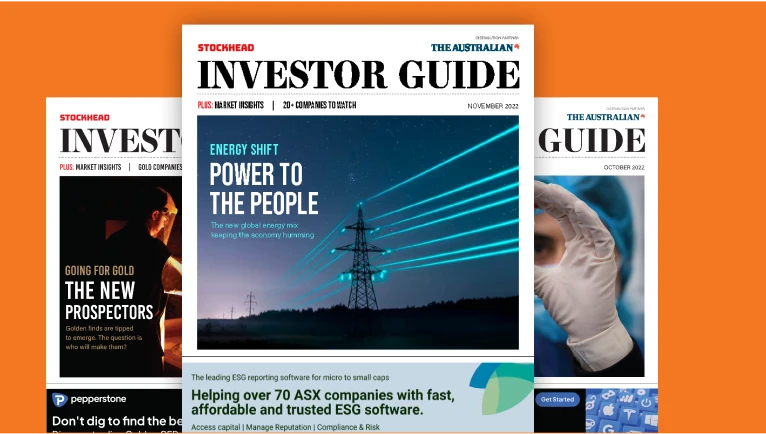
UNLOCK INSIGHTS
Discover the untold stories of emerging ASX stocks.
Daily news and expert analysis, it's free to subscribe.
By proceeding, you confirm you understand that we handle personal information in accordance with our Privacy Policy.