Could this be the face of mining in the net zero world?
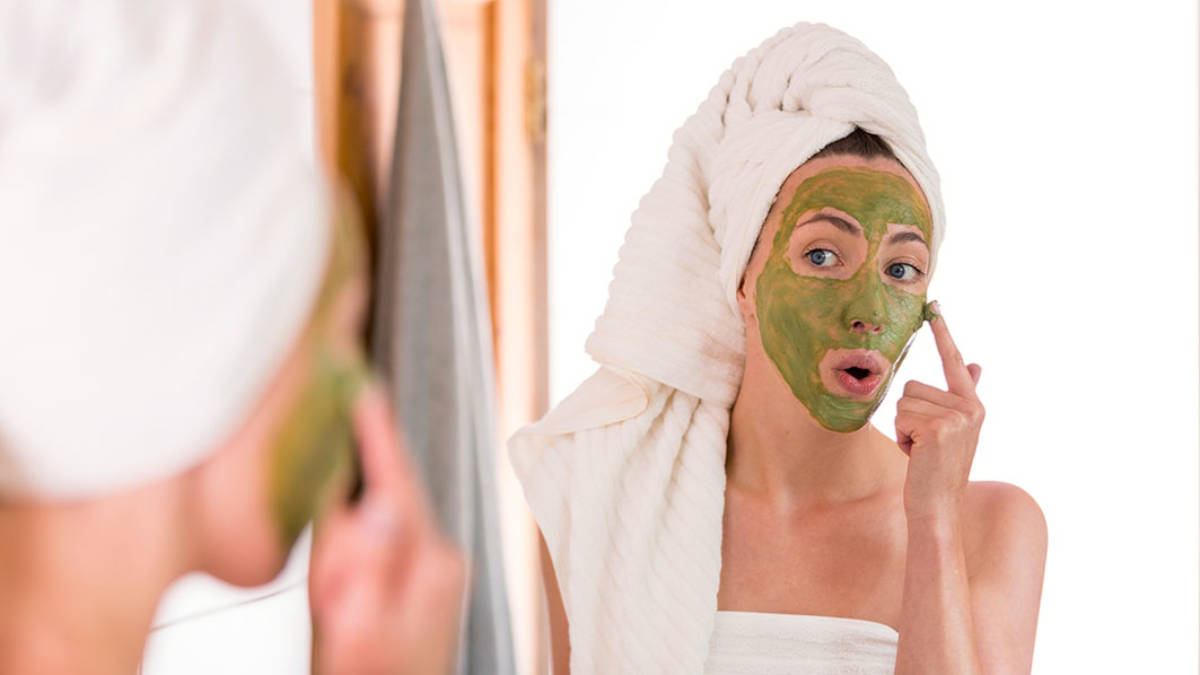
Going green. Pic: via Getty Images
- Anglo American develops largest HFCV mine haul truck
- Green hydrogen produced on mine site
- Hydrogen offers advantages over batteries for industrial users
As we continue the charge into the brave new world of net zero emissions, multinational miner Anglo American has given us a glimpse of how the mining industry could embrace the change.
The company has unveiled a prototype of the world’s largest hydrogen-powered mine haul truck that is designed to operate in everyday mining conditions at its Mogalakwena PGM mine in South Africa.
As with many things in the mining sector, the scale of the conversion to make the 210 tonne truck run on the fuel of the future is equally massive.
Anglo American ripped out the original 16-cylinder diesel engine that used to power its electric traction motors and replaced it with a bank of eight 100 kilowatt hydrogen fuel cells and a 1.1 megawatt lithium-ion battery pack that actually generates more power than its predecessor – allowing it to retain its ability to haul 290t of material.
The truck will be powered by green hydrogen produced on site using a 3.5MW electrolyser that will draw power from an existing 100MW solar array to produce about 1t of hydrogen per day.
Chief executive Duncan Wanblad noted that with the company’s haul trucks accounting for between 10% and 15% of its emissions, the nuGen solution was an important step in its path to carbon neutral operations by 2040.
“If this pilot is successful, we could remove up to 80% of diesel emissions at our open pit mines by rolling this technology across our global fleet,” he added.
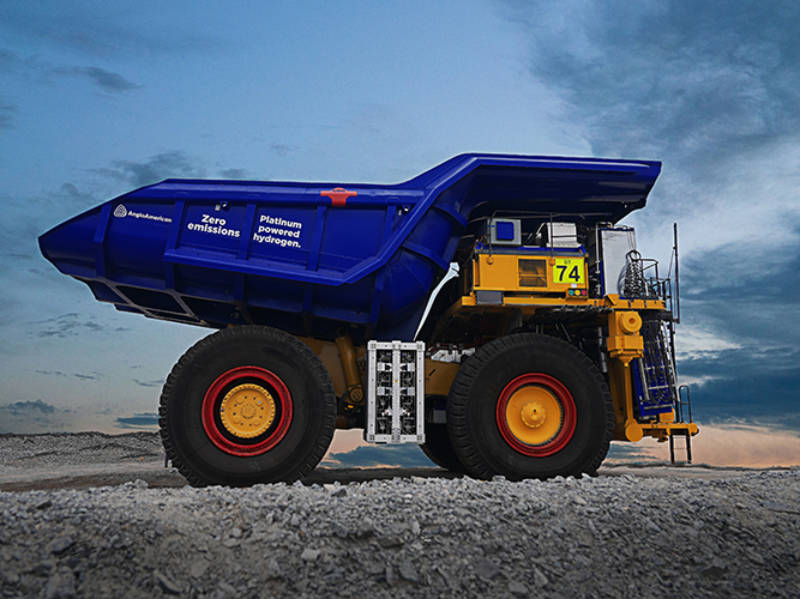
Hydrogen over batteries
Anglo American’s selection of hydrogen fuel cells over batteries is potentially another sign that industrial and commercial users may favour the former in their vehicles as they pursue net zero initiatives.
There are several reasons for this.
Firstly, while battery storage systems paired with electric motors are fine for consumer vehicles – and indeed have a massive head start over HFCVs, the weight of batteries is less than ideal for larger vehicles be they trucks, buses or giant mining vehicles.
This is due to the higher energy density of hydrogen compared to batteries, which taking the example of the mine haul truck means lower payload.
The same factor also means that HFCVs could potentially have greater range than BEVs, which is far more critical in a industrial or commercial setting.
Second up is the ease of refuelling or recharging and there is quite literally no competition here.
Commercial and industrial vehicles typically require as less downtime, something BEVs and their long recharge times do not support especially when contrasted with HFCVs having the ability to be refuelled quickly just like regular internal combustion powered vehicles.
Last but certainly not least is battery degradation, something that all lithium-ion batteries suffer from.
Simply put, a BEV that has been in use for some time will have lower range due to the permanent reduction in the amount of energy that its onboard battery can store. Hardly ideal for vehicles that are used for long periods of time.
Green mining
Anglo American is hardly the first miner to take steps to reduce its environmental blueprint, though it is certainly a front runner in greening its haul fleet.
BHP and Rio recently formed a consortium to study a “green corridor” for iron ore, which is basically a low emissions shipping route from Australia to East Asia, to help achieve net zero.
This includes the use of green ammonia, which is incidentally considered to be one of the best carriers for hydrogen, as the fuel of choice.
Separately, BHP has also signed a power purchase agreement to take all the energy from the Flat Rocks Wind Farm for its Kalgoorlie nickel smelter and Kambalda concentrator from 2024 on.
Related Topics
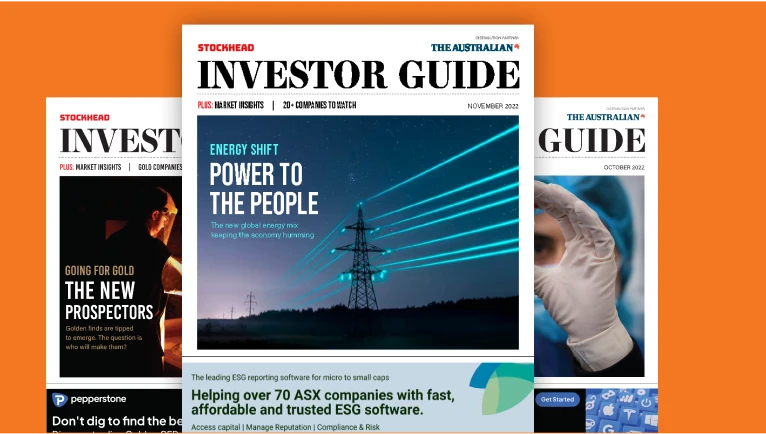
UNLOCK INSIGHTS
Discover the untold stories of emerging ASX stocks.
Daily news and expert analysis, it's free to subscribe.
By proceeding, you confirm you understand that we handle personal information in accordance with our Privacy Policy.