Battery recycling is gaining momentum; here’s why and who’s into it
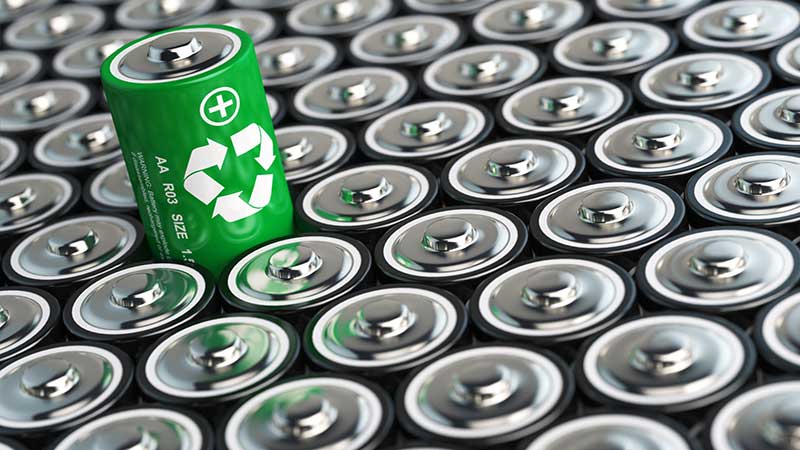
Battery recycling will recover critical minerals, reducing their impact on the environment and improving supply chain security. Pic: Getty Images
As adoption of electric vehicles (EVs) and energy storage increases, the demand for battery metals such as lithium, nickel, cobalt and graphite will also increase in tandem.
In Australia alone, IDTechEx expects more than 2.5 gigawatt hours of battery installations in 2021, a seven-fold increase over 2017.
However, the greater use of lithium-ion batteries will increasingly be accompanied by more LiBs being disposed after they are depleted.
And that is cause for concern. Many of the heavier metals used in batteries will leach into surface and groundwater, which could pollute the environment, once the batteries start to break down in landfill.
Speaking to Stockhead, Lithium Australia (ASX:LIT) managing director Adrian Griffin noted that with most EV batteries having an anticipated useable life of 10-12 years, most of the EVs on Australian roads still have a fairly significant service life.
“Once we’ve gone beyond that and those vehicles are retired, we will start to see a constant flow of larger batteries,” he noted.
Once these early generation batteries reach their end of life, the volumes of spent batteries is also expected to climb.
Chemical & Engineering News reported industry analysts as predicting that China alone would generate 2 million tonnes of used lithium-ion batteries per annum by 2030, up from the expected 500,000 metric tonnes in 2020.
If current trends continue, most of those batteries will end up as landfill.
In 2019, the CSIRO released a study showing that just 2 per cent of Australia’s annual LiB waste was recycled.
This is a potentially large amount given that it also estimated that Australia could generate 100,000tpa of LiB waste by 2036.
It is also sobering when one considers that 98 per cent of all lead-acid batteries – an older more mature technology – are recycled.
Why recycle?
Besides removing the amount of battery waste that goes into landfill, LiB recycling also allows us to recover the high value materials used in their manufacture.
As Griffin pointed out, people are concerned about the longevity of critical mineral and an enormous amount of energy goes into mining and processing the metals before they are turned into battery chemicals that are then used to make cathode and anode powders.
“That’s a big energy footprint and then we just throw them away when they get to the end of their effective life,” he said.
“That’s just crazy both from an environmental point of view and a commercial point of view.”
Recycling battery metals could also improve supply chain security, particularly with cobalt, as it is rare for the entire supply or production chain to be located in a single country.
Lithium is a notable example with Griffin saying that about 70 per cent of the spodumene concentrate produced in Australia is shipped to China for processing with the rest going into Europe, North America, Japan and South Korea.
Recycling would see at least a (hopefully significant) portion of the battery metals already present to stay within the same country or region and be reused, which could alleviate supply concerns.
Current progress
Fortunately, there is a definite move towards battery recycling.
Volkswagen, one of the world’s largest automobile manufacturers and a major proponent of EVs, has just opened a pilot battery recycling plant in Salzgitter, Germany, that is aimed at industrialising the recovery of battery metals such as lithium, nickel, manganese and cobalt.
The company plans to achieve a recycling rate of more than 90 per cent over the long term.
While this plant has been designed to initially recycle about 1,500t of waste per annum, it can also be scaled up to handle larger quantities.
The German carmaker’s move to establish recycling operations stems in part from the European Union’s requirement that manufacturers be responsible for disposing of spent batteries in an environmentally friendly way.
This same rule resulted in Tesla copping a 12 million euro ($18.9m) fine late last year for alleged non-compliance of ‘take-back obligations with respect to end-of-life battery products’.
Meanwhile, a Singapore-based start-up has claimed that its patented technology could be the solution for recycling LiBs.
Green Li-ion claimed its multi-cathode processor can speed up current recycling processes while lowering costs.
It added that its solution is only technology able to fully rejuvenate every type of LiB cathode.
Australian battery recycling
They are not the only player in the recycling game.
Lithium Australia had initially developed technology to recover battery metals from spent LiBs before realising that it was not viable to own the technology without getting the batteries.
This led to the company acquiring Victorian recycler EnviroStream, which Griffin said was the only recycler that actually recycled batteries rather than just collecting and exporting them.
Another point of difference from most other battery recyclers is that while the common method of recycling involves incineration, Lithium Australia shreds the batteries at ambient temperature before recovering the various commodities.
While incineration solves the problem of handling plastics and the organic solvents used in the electrolyte by burning them off, it also burns about half of battery’s lithium content, which is contained in the electrolyte, and potentially produces a pollution problem.
In contrast, Lithium Australia’s method allows the company to a lot more without polluting the environment.
“The plastics go into a process where they are mixed with waste oil, they are thermally treated and produce synthetic bitumen for use in servicing roads,” Griffin told Stockhead.
Laboratory scale work has been successful in recovering certain organic compounds from the electrolytes with the company just installing circuits to do so on a commercial scale.
Griffin added that currently most of the active components that make up the cathode and anode powders are currently being exported to South Korea where SungEel Hitech, the largest refiner of that sort of material, recovers the battery metals, as the Australian market is currently too small to warrant the capital expenditure for refining.
“But I think that’s going to grow very rapidly, and in particular with the introduction of the battery stewardship scheme in July this year,” Griffin noted.
“The scheme charges a levy at the point of sale of the battery, the money goes back to the Stewardship Council which divides that amongst the parties collecting, sorting and recycling the batteries.
“When they do that, it effectively puts a price on a battery so they’ve commoditised that waste material and as a consequence of that we would expect to see the quantity of batteries covered as a percentage of those sold in Australia go from sub 10% – which it is today – to more like the average that we see in countries that have similar stewardship schemes, and that number is between 40 and 50%.”
Related Topics
UNLOCK INSIGHTS
Discover the untold stories of emerging ASX stocks.
Daily news and expert analysis, it's free to subscribe.
By proceeding, you confirm you understand that we handle personal information in accordance with our Privacy Policy.