Yamaha is making boats with wood 5x stronger than steel… But Aussie spinifex cellulose nanofibre is tougher, mate
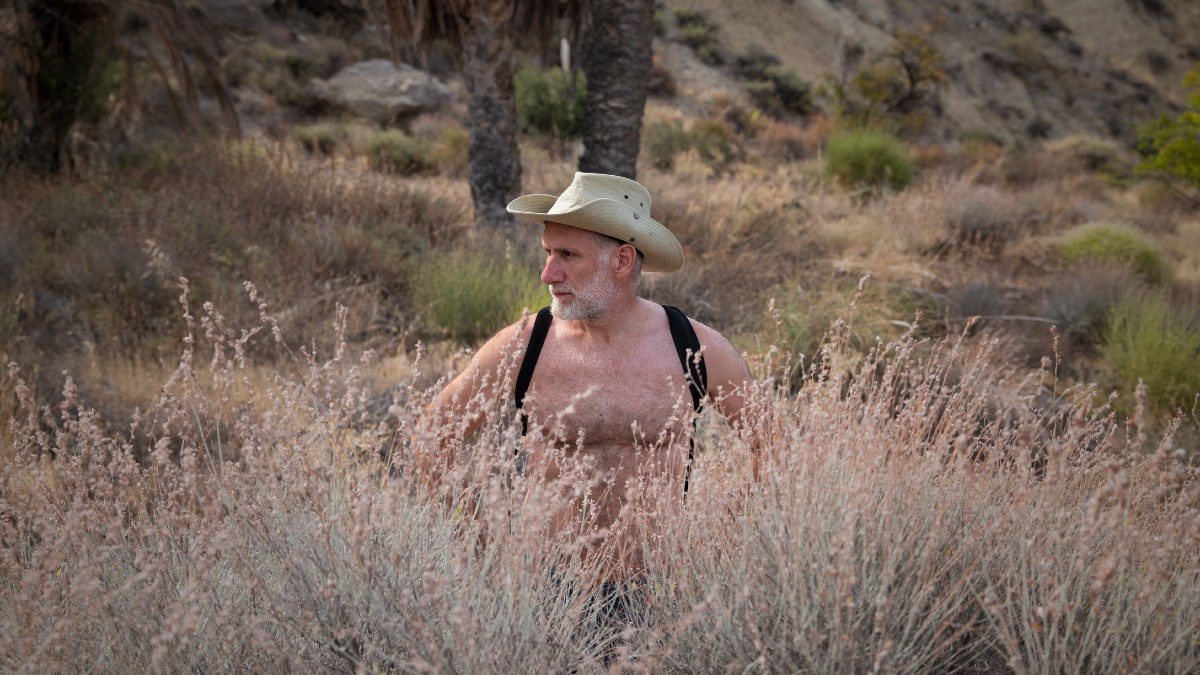
Via Getty
Going green is working out for the Yamaha Motor Co which has started using the ultra-strong wood-derived cellulose nanofibers (CNF) to replace plastic parts in its line of boats.
Asahi Shimbun reports Yamaha’s CNF is no less than five times stronger than steel, and is part of Japan’s next-generation material, designed and developed in-country.
According to Japan’s New Energy and Industrial Technology Development Organisation, cellulosic materials, including those other than CNF, which offer the strength, heat resistance, impact resistance, and other performance requirements of plastic parts, are being developed in more than 15 countries around the world.
One of those countries is Queensland. But more of that in a jif.
Yamaha says it’s adopted the use of plant-derived CNF reinforced resin for parts in its 2024 models of WaveRunner – that’s a jetski (personal watercraft) – and snazzy sports boats and is already being flogged at a premium in the States.
This initiative cuts CO2 emissions and the company’s environmental footprint.
Asahi says it’s ‘the world’s first case of mass-producing vehicle parts’ using this material.
The CNF reinforced resin part being mass-produced is the engine cover for power units and was developed with local paper giant, Nippon Paper Industries Co.
Spinifex: CNF goes Australian
The Aussie Gov provides cutting edge national research infrastructure funding through the National Collaborative Research Infrastructure Strategy (NCRIS).
Long story, short: back in 2011, the Uni of Qld discovered that the Australian arid spinifex grass is ‘a unique source of flexible cellulose nanofibers (CNF) of very high yield, aspect ratio, ductility and toughness.’
Nothing surprising there – Aussies being both very tough and wildly ductile.
Spinifex, a hardy Australian grass, spread widely across inland Australia, presents a new high-tech opportunity for the future of construction, medical technology, and day-to-day life.
In partnership with the Indjalandji-Dhidhanu People of NW Queensland, through Bulugudu Ltd, researchers at UQ have been developing a high-tech product from the spinifex that grows abundantly around the country and particularly on the Indjalandji-Dhidhanuon lands: hello again, nanocellulose.
Spinifex nanocellulose is a stronger, more eco-friendly, and energy efficient alternative to other sources of nanocellulose, and its harvesting and initial processing supports local Indigenous jobs.
Spinifex nanocellulose can be used in a pretty incredible range of applications.
Who doesn’t want stronger concrete and better condoms?
Super tough, low-cost carbon fibre?
What has seed investors pumped as well is it can also form a gel made up of a network of nanocellulose fibres that trap and hold water.
“This gel has some potentially exciting applications in healthcare, as a medical gel, and in agriculture as a growth regulator to boost crop yield in semi-arid regions of Australia,” according to investors including the National Collaborative Research Infrastructure Strategy (NCRIS)
Two facilities supported by the Department of Education through NCRIS, Microscopy Australia and the Australian National Fabrication Facility (ANFF), provided the encouragement and the cash for long-term support for this project.
Since the project’s inception in 2012 Microscopy Australia has provided the research team with access to advanced microscopes that have allowed them to develop, refine and test new products, including the new nanocellulose gel.
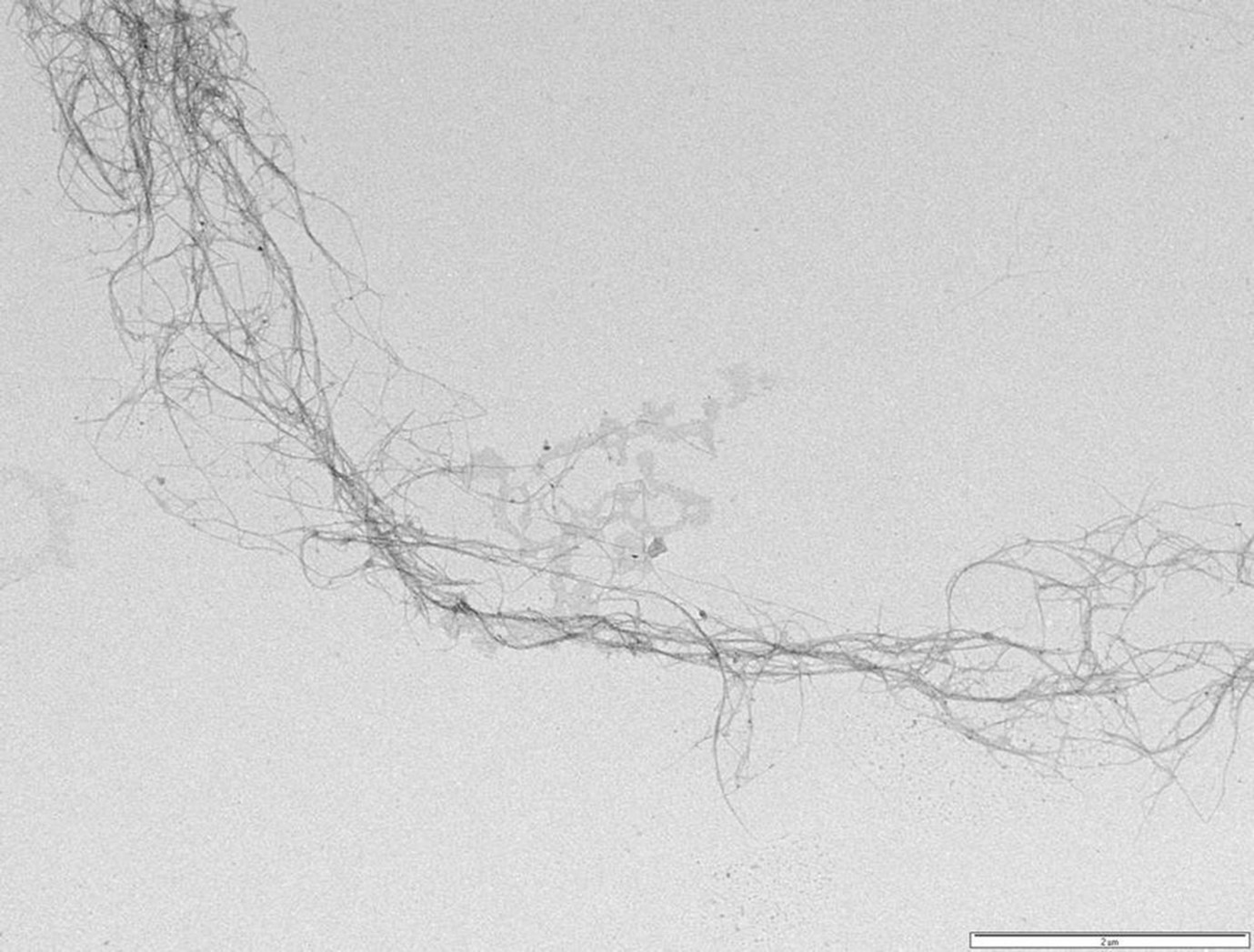
Images from these microscopes helped to demonstrate proof-of-concept and were used in the nanocellulose product patent. ANFF’s support for this project includes access to the specialist tools needed for working in the nano regime and, through its commercialisation arm, ANFF-C, the funding and facilities for further proof-of-concept work to advance the product to a point of maturity where it was investable.
But the UQ’s Martin Group, formerly led by senior group leader Professor Darren Martin, began the work out of the Institute for Biotechnology and Nanotechnology delivering on the thesis ‘that extreme environments drive the evolution of plants with unusual material properties.’
Former lead researcher on the project, and spinifex nanocellulose discoverer, Prof Darren Martin’s goal has been to ‘replace or improve everyday materials such as plastics, rubbers, packaging, insulation foams and carbon materials, many of which are unsustainably sourced from petrochemical-derived materials, with sustainable alternatives or additives.’
“These types of projects typically involve over a decade of work, many researchers, funding sources and partnerships. These partnerships include Microscopy Australia and ANFF who have provided valuable infrastructure and long-term support that have helped make this project possible,” Martin adds.
UniQuest, Bulugudu and ANFF-C has funded the spin-off company, Trioda Wilingi, who are commercialising a new medical gel developed from the spinifex nanocellulose.

Trioda Wilingi has already been seeded with $2.6 million of funding this year from Uniseed and Bulugudu to commercialise and create injectable medical gels, with Trioda maintaining exclusive rights – with potential uses “including osteoarthritis, drug delivery and cosmetic treatments” and using the process developed with the ANFF.
“ANFF is proud to support projects which look to use traditional knowledge of our world to create new technologies that can improve all our lives”, ANFF CEO Jane Fitzpatrick, said last month.
“We hope that this is just the beginning of the tidal wave of information that our traditional custodians can turn into technologies that will benefit us all”.
In developing such new material tech , the group’s aim is to try and enhance the mechanical properties and OFC performance compared to what’s out there now.
‘You bought a boat?’
Meantime, back in Japan Yamaha and Nippon Paper developed a reinforced CNF resin, with an eye toward commercial applications for the new high-strength material – somehow created by kneading and dispersing the biomass material made from wood resources – into resins such as polypropylene.
Nippon Paper says CNF is made from wood-derived pulp that has been micro-refined to the nano level ‘of several hundredths of a micron’ and smaller, cellulose nanofibre, “is the world’s most advanced biomass material.”
Yamaha Motors is exploring a broader set of applications for cellulose fibres, not only in marine products but also in motorbikes and a wide range of other Yamaha products in the future. Keyboards, one would hope.
In addition to being more than 25% lighter than existing resin materials, Yamaha and Nippon Paper reckon the resin also has excellent material recyclability, slashing plastics use and greenhouse gases.
Yamaha began selling the products in North America about seven weeks ago.
Now that it’s being used commercially – mainly in transport equipment parts – CNF applications are gaining global attention in the brace to minimise carbon footprints.
Yamaha says it went with ‘personal watercraft such as speedboats’ as they carry a ‘sufficiently high price tag to absorb’ the cost of the material.
There are some 26 factories making the CNF resin in Japan, but while it has a high environmental adaptability, it’s hella expensive to make.
Watercraft utilising the resin arrived on the North American market in August and they sell for around US$13,700, about the same punch as earlier models.
Yamaha is looking to release across Japan and then worldwide, by which time the price of the resin products should drop after hitting widespread commercial use.
“We will be moving to take advantage of the material for high-end motorcycle bodies and other parts, too,” Yamaha said in a statement.
Back at home, starting with pre-clinical trials, Trioda will develop its medical gels which have already shown potential across an array of health and wellness markets with applications from osteoarthritis, drug delivery to cosmetic treatments.
UNLOCK INSIGHTS
Discover the untold stories of emerging ASX stocks.
Daily news and expert analysis, it's free to subscribe.
By proceeding, you confirm you understand that we handle personal information in accordance with our Privacy Policy.