The pandemic could make companies think twice about manufacturing offshore
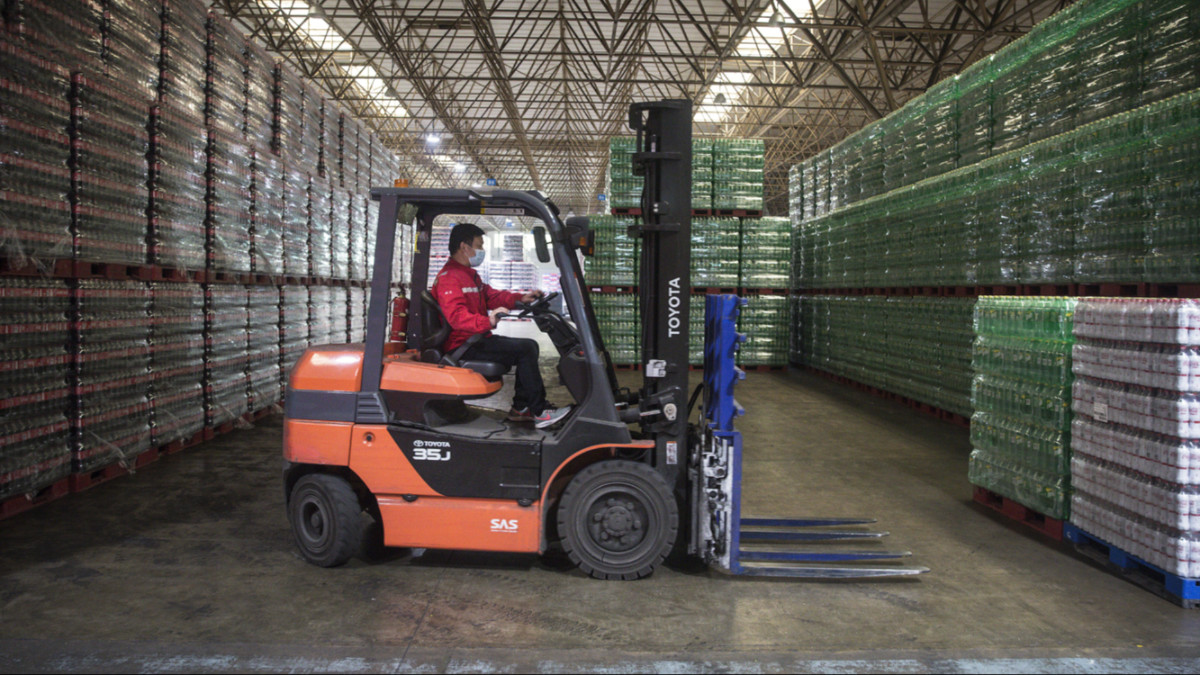
Factories in China are gradually re-opening, including this beverage factory in Wuhan (Picture: Getty)
The COVID-19 pandemic will result in changes to several industries and one of these is manufacturing.
Since the early 1960s manufacturing as a percentage of Australian GDP has dropped from 30 per cent to 5.7 per cent now.
Of course Australia still has a substantial industry. But much manufacturing that is less labour-intensive has shifted offshore.
COVID-19 has been a wakeup call for businesses but more so for businesses that have relied on overseas manufacturing.
Most, if not all, companies have been either forced to halt operations or at least drastically alter them to abide with regulations. Companies with offshore manufacturing have had the double whammy of COVID-19 restrictions and the disruption of international trade.
This experience could in future prompt companies to rethink the strategy of doing something just to keep costs down.
Fixing the local v import imbalance
Ben Lazzaro, the boss of the Australian Made campaign, says that while there will still be a need for some imports, up until recently there has been a big imbalance between local and imported, and COVID-19 has shone a spotlight on the issue.
He told Stockhead if businesses can produce products locally in bad times there’s no reason they can’t in good times.
“Australian business and government all have the ability to put in policies that prioritise Australian products and at a time like this it has been illustrated that if we’re reliant on imports we become exposed,” Lazzaro said.
“We know that for an economy you need a mix of imports and locally made products but there’s been an imbalance between the two in recent times.
“This is a reminder we should correct that balance and source locally for the benefit – for our local economy and employment.”
But Lazzaro stressed it wasn’t just about clothes and call centres – two more widely publicised industries that have gone offshore, but also industries such as chemicals and construction materials.
More to it than just cost
COVID-19 has not stopped deals with overseas manufacturing going ahead. But signs of a new norm are emerging.
One ASX small cap that did an overseas manufacturing deal last week was neurological-focused biotech NeuroScientific Biopharmaceuticals (ASX:NSB).
Japanese industrial giant Mitsubishi agreed to perform feasibility and analytical services for large-scale drug manufacturing for future clinical programs.
NeuroScientific Biopharmaceuticals CEO Matthew Liddlelow explained to Stockhead the decision made business sense.
“Being a drug development company working with a novel and complex compound in a highly regulated industry, we sometimes don’t have the option of using an Australia-based company for some aspects of the drug development process,” he said.
“There is only one manufacturer in Australia with the expertise to reliably produce our drug. We’ve successful worked with them and will continue to do so, but we exhausted their capacity to produce the amounts we need for future clinical development programs.
“Therefore, we had to partner with a manufacturing company that has the expertise and capacity to scale-up manufacturing to much greater production quantities.”
‘Enabling the repatriation of manufacturing’
Another example is additive manufacturer Amaero International (ASX:3DA) which has facilities in Australia and the US.
CEO Barrie Finnin told Stockhead earlier this month COVID-19 could overhaul business as we know it for additive manufacturers.
Being a capital intensive industry, government support was already an important factor. But the crisis has awakened governments to the merits of a vibrant local industry.
“There’s some stronger arguments around manufacturing and sovereignty and that’s influencing government policy,” Finnin said.
“In the present circumstances when people are just not moving around, being able to acquire manufactured goods locally is a big advantage. So [COVID-19] is probably enabling repatriation of manufacturing and it’s seen by the Australian and US government.
“Because we can turn around and produce something in days and not weeks and months. This is probably the tidal wave. Having required tools is a benefit.”
NOW READ: Here’s what COVID-19 means for additive manufacturers – and it’s not all bad news
Related Topics
UNLOCK INSIGHTS
Discover the untold stories of emerging ASX stocks.
Daily news and expert analysis, it's free to subscribe.
By proceeding, you confirm you understand that we handle personal information in accordance with our Privacy Policy.