School of Rock: What exactly are rare earths and why magnets are vital to the clean energy mix
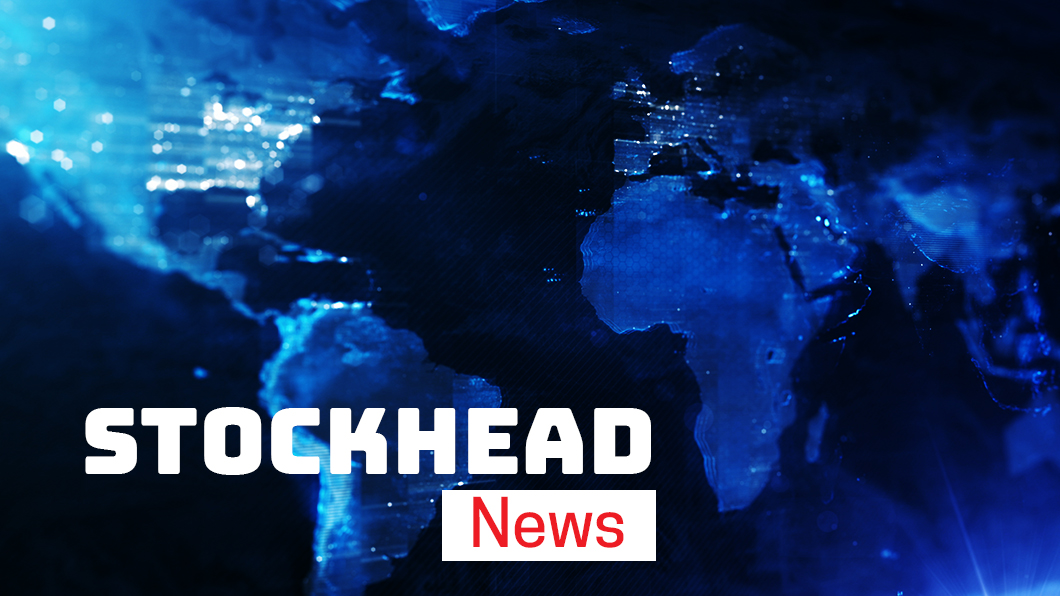
Pic: DKosig / iStock / Getty Images Plus via Getty Images
Have you heard all the fuss about rare earths but don’t quite understand why they’re so vital?
Basically, rare earth elements (REEs) are 15 soft heavy metals with a range of industrial applications.
They can be separated into two categories:
- Light REEs – including lanthanum (La), cerium (Ce), praseodymium (Pr) and neodymium (Nd); and
- Heavy REEs – including samarium (Sm) to lutetium (Lu) and yttrium (Y)
According to a recent report by Wood Mackenzie analyst Ross Embleton and battery & electric vehicle materials manager David Merriman, they’re used in the electrical and electronic industries, the oil industry, aviation and the manufacture of glass and lasers, among other things.
But it’s their use in magnet technologies that has caught the market’s eye because it provides an opportunity to shrink electrical components and improve their efficiency – which has proven vital to the development of some new energy technologies.
Where are REEs found?
Usually, the highest concentrations of REEs are found in alkaline complexes and carbonatites (a type of igneous rock).
The commercial extraction of rare earths is dominated by several mineralogies, including bastnaesite, ion-adsorption clays, monazite and xenotime which together account for more than 95% of economic production.
Light REEs are predominantly recovered from mineral concentrates of monazite and bastnaesite in China, the US, Australia, India and Madagascar. They’re also found in the mineral loparite, mined in Russia.
Most heavy REEs are sourced from ion-adsorption clay deposits and xenotime mineralisation in Myanmar and China, with minor volumes sourced from Australia.
Where is refined production centred?
Concentrates of rare earth minerals are processed into refined products, but for magnetic applications, rare earth oxides must be further refined into rare earth metals and alloys.
These are the requisite precursor materials for magnet manufacturing.
In 2020 China accounted for 85% of global production of refined rare earth products, with other Asian countries (Malaysia, India and Vietnam) and minor European operations making up the remainder.
Plus, China consolidated its domestic rare earth industry into six state-owned enterprises – which gives it greater control over the supply and pricing of rare earth exports globally.
It’s no surprise that the geographic concentration of rare earth mining and refined production has raised concerns over the potential for supply disruption, with countries like the US taking steps to boost domestic mining.
How is magnet demand looking?
REE use in clean tech like wind turbines and electric vehicle (EV) drivetrains has spurred demand for rare earth permanent magnets, with neodymium (NdFeB) magnets commanding the largest market share.
In 2020 the consumption of rare earths for catalysts, polishing powders and metallurgical applications accounted for 42% of rare earth demand in volume, while permanent magnets accounted for just 29%.
But in terms of market value, Nd accounted for 62%, Pr for 13% and Dy for 10.2%.
And driven by the global transition to a lower carbon future, the increased interest in the industry has resulted in higher prices – which is a boon for REE projects worldwide and presents opportunities to diversify supply.
Especially as around 90% of NdFeB magnet manufacturing currently takes place in China.
Several projects on the starting line
Wood Mackenzie pointed to several notable recent developments including the start of a production initiative between Chemours, Energy Fuels (NYSE:UUUU) and Neo Performance Materials (TSX:NEO).
Energy Fuels processes monazite sands from Chemours’ Starke project in northeast Florida at its White Mesa facility in Utah, which involves extracting uranium and thorium and producing a mixed rare earth carbonate product to be shipped to Neo’s Silmet facility in Estonia for separation.
Plus, the commercial-scale production of rare earth concentrate began at Vital Metals (ASX:VML) Nechalacho mine in Canada this year with material to be sent for refining at the Saskatchewan Research Council’s cracking and leaching facility in Saskatoon in late 2021.
In Australia, financial and legislative support from the government is helping to incentivise the development of multiple rare earth operations, including Iluka Resources’ (ASX:ILU) Eneabba refinery and Arafura Resources’ (ASX:ARU) Nolans project.
And there’s the ongoing relocation of Lynas’ (ASX:LYC) LAMP cracking and leaching facility from Malaysia to Kalgoorlie, which would see the first commercial-scale rare earth cracking and leaching capacity commissioned in Australia.
Plus, Lynas has also entered into agreements with the US Department of Defense to establish light REE and heavy REE separation facilities in Texas.
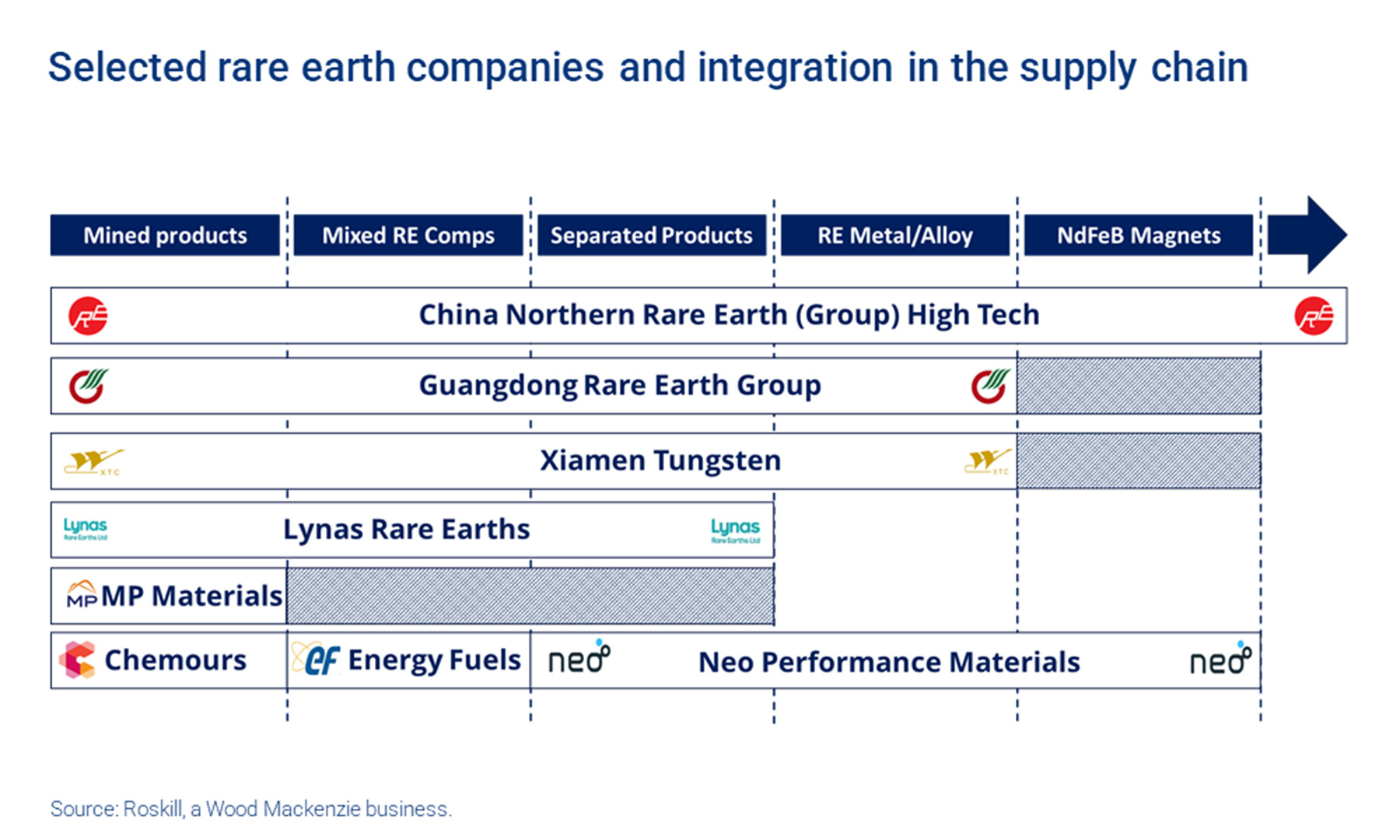
Related Topics
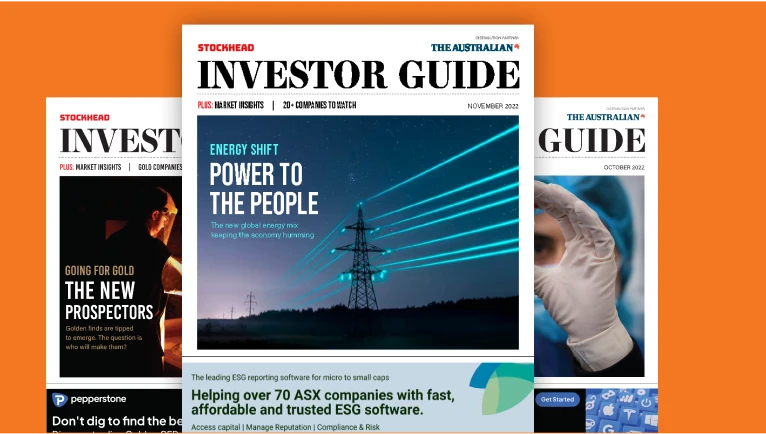
UNLOCK INSIGHTS
Discover the untold stories of emerging ASX stocks.
Daily news and expert analysis, it's free to subscribe.
By proceeding, you confirm you understand that we handle personal information in accordance with our Privacy Policy.