Eco-friendly rare earth mining? UniSA researchers are on the case
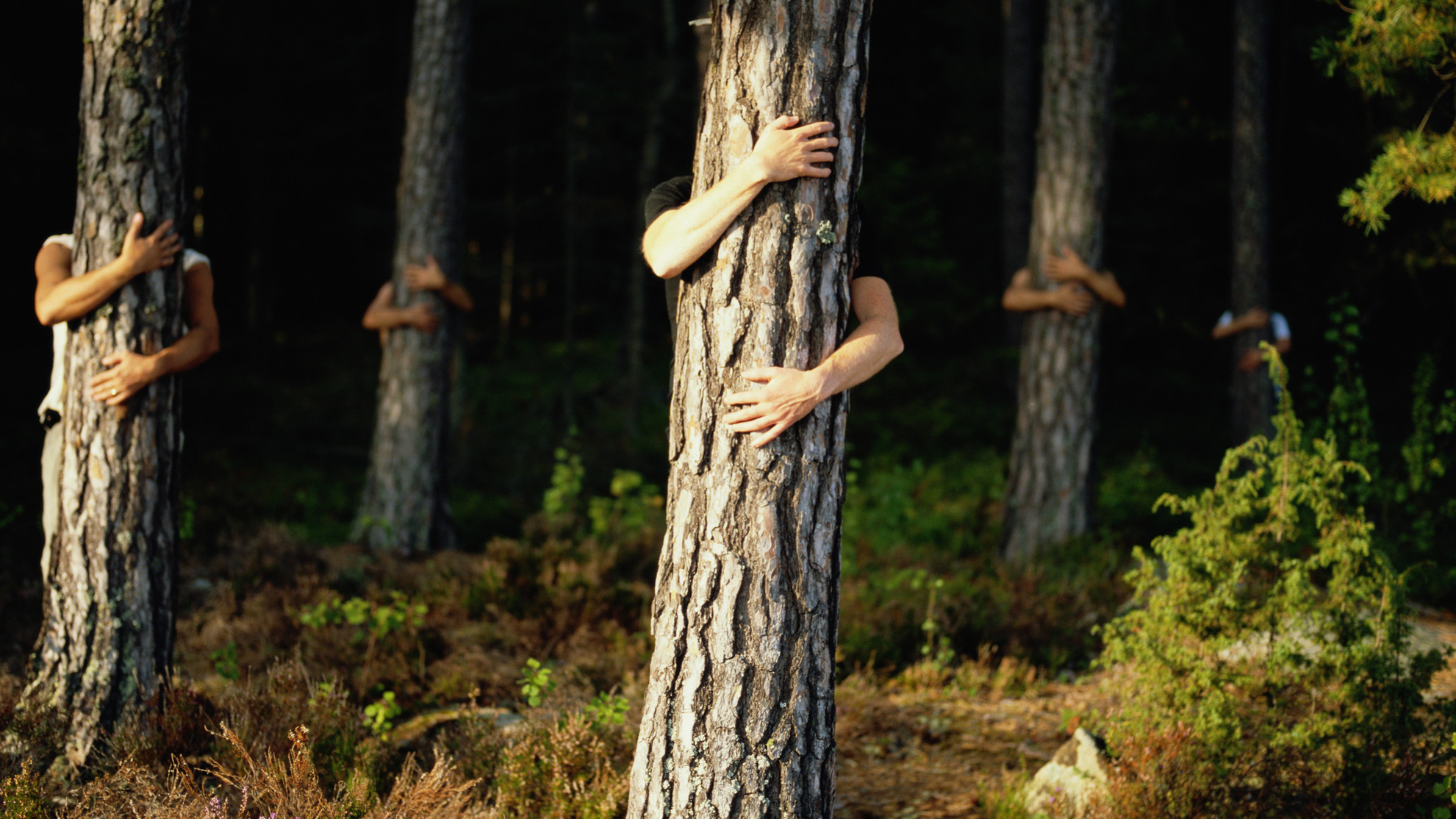
Pic: David Trood (DigitalVision) via Getty Images
- UniSA is researching how to process rare earths tailings and spent batteries and magnets
- Separation is energy intensive and uses highly toxic acids and produces a lot of waste
- Rare earth elements contribute nearly $200 billion to the Indian economy
The University of SA’s Future Industry Institute is working on transforming the way rare earths elements and other vital battery metals are recovered from the earth.
Rare earths are the driving force behind electric vehicles and are crucial to the manufacture of wind turbines and magnets – but they’re very hazardous to extract with highly toxic acids used to separate out the useful elements.
Dr Richmond Asamoah said the institute is developing methods to safely extract critical minerals from downstream ore processing, tailings reprocessing and wastewater treatments, which would enable safer extraction with fewer environmental impacts.
“Accumulated mining wastes are becoming an increasingly valuable source of metals and energy, but because there’s a lack of productive and economically viable extraction technologies, there’s also a notable loss of valuable metals,” Dr Asamoah says.
“The process of extracting these critical materials is very damaging to the environment, with conventional mining methods generating large volumes of toxic and radioactive materials.
“Our research will identify new technologies that have the capability to both extract minerals from existing industrial wastes and mineral tailings, and recycle and source minerals and metals from spent batteries and magnets.
“As a result, we should be able to significantly reduce the amount of waste and harmful materials that can seep into the environment.”
New @UniversitySA #research could transform the way rare earth elements and vital battery metals are recovered from the earth, enabling safer extraction with fewer toxic impacts to the #environment. #mines #mining #recycling #preciousmetals #technologies https://t.co/YnZYxVLO8F pic.twitter.com/xSug4c8WVI
— UniSA (@UniversitySA) March 31, 2022
Processing tailings to minimise environmental impact
When rare earth minerals are mined, they can be radioactive or only consist of around 1% rare earth elements (REE) – so processing and separation is needed.
The material is first crushed into an extremely fine powder and then the elements are further isolated by putting the crushed ore in flotation tanks.
This is where the minerals are coated with a chemical that repels water and allows them to float to the surface attached to air bubbles in agitated tanks, where they are skimmed off as a concentrate.
Then separation occurs, called solvent extraction, where the materials are put through solvent cycles with highly toxic acids, sometimes up to 100 times.
It’s energy intensive and often results in a lot of waste – plus it can be pretty pricey if a miner doesn’t have a production centre nearby and has to send their concentrate to China for separation.
But UniSA says their project has potential to make the processing part environmentally friendly.
The project will test two metal recovery processes – resin in pulp and resin in moist mix – to extract target metals from low grade ores, fine minerals and wastes such as tailings.
These processes can also be used to remove harmful substances from water and soils to minimise their environmental impact.
Backed by Australia-India Strategic Research Fund
Notably, the research is funded by the Australia-India Strategic Research Fund, and Dr Asamoah says it will deliver “significant benefits” to both countries.
“We’re not only talking about environmental benefits, but also economical and sustainable technologies that both countries can use to extract rare earth and battery minerals from current mining operations,” Dr Asamoah says.
“Rare earth elements contribute nearly $200 billion to the Indian economy, yet despite India having the world’s fifth largest reserves of critical metals, they mostly import their rare earth needs from China.
“This project hopes to enable Australia to export rare earth minerals to India, as an alternative to China, as well as to empower India to establish eco-technologies to extract minerals and metals within their own borders.
“Importantly, the research will build capacity for processing critical minerals in Australia and India and creating many new eco-efficient opportunities for economic growth, employment and investment.”
Related Topics
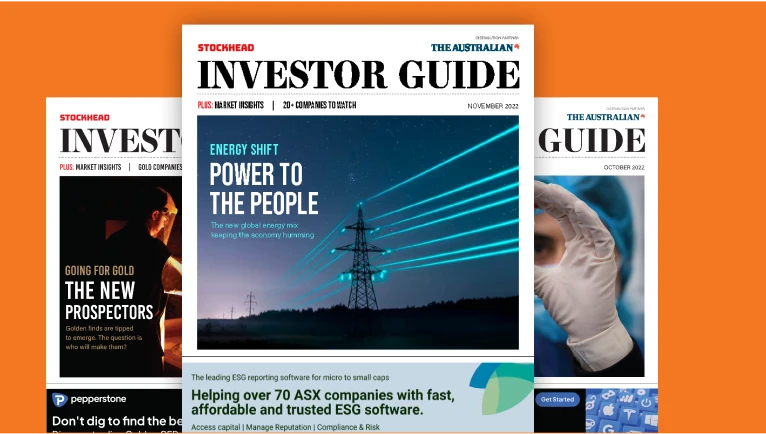
UNLOCK INSIGHTS
Discover the untold stories of emerging ASX stocks.
Daily news and expert analysis, it's free to subscribe.
By proceeding, you confirm you understand that we handle personal information in accordance with our Privacy Policy.