GOT GAS: Toyota fires the first shot in hydrogen’s new offensive
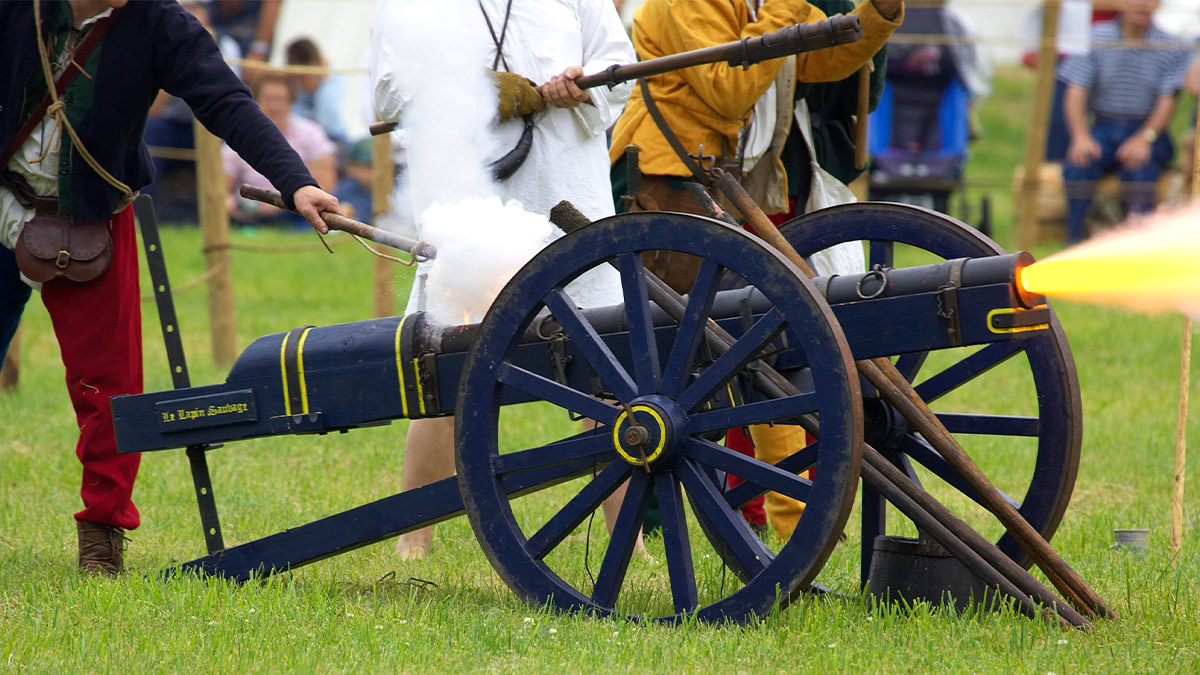
Is Toyota's salvo at BEVs enough to breathe life into the hydrogen sector. Pic: via Getty Images.
Some of the biggest proponents of hydrogen have come out swinging in recent weeks as they push to increase adoption of the green gas.
Toyota, the world’s largest car maker and also the most stubborn in its advocacy for the use of hydrogen in consumer vehicles, unveiled a prototype of its HiAce van with a hydrogen-fuelled internal combustion engine in Australia.
Let’s be clear. The Japanese car giant is not promoting hydrogen fuel cells that generate electricity to power motors; this is a petrol engine with minor changes to let it burn hydrogen instead of a fossil fuel to drive cylinders that move the van.
However, the system still needs work with the van having a range of just 200km – far less than the 650km claimed by the company’s Mirai HFCEV.
Toyota claims it intends to fully commercialise the technology at some stage and clearly believes this is the magic bullet that could end the run of battery electric vehicles.
This doesn’t change any of the old arguments against hydrogen at this point though, chief of which is the complete lack of supporting infrastructure.
At last count, there are just six – count them – places when one can refuel a hydrogen vehicle in Australia.
To make its dream work, Toyota will have to a) increase the number of refuelling stations by several orders of magnitude, b) increase the range of the hydrogen burning vehicles and c) find some way to convert existing vehicles quickly.
Iron ore major puts the stamp on green hydrogen projects
Speaking of green hydrogen proponents, Andrew Forrest’s Fortescue Metals Group (ASX:FMG) has given the go-ahead to two green hydrogen projects (and a green iron project).
The company will develop the US$550m Phoenix Hydrogen Hub in Arizona, which will use a 80MW electrolyser and liquefaction facility to produce up to 11,000t of liquid green hydrogen per annum, and the US$150m Gladstone PEM50 facility that will feature a 50MW electrolyser of FMG’s own design.
The latter will have the accompanying goal of proving up the ability of the company’s proprietary technology to produce green hydrogen at an industrial scale.
Not that FMG has forgotten its roots.
After all, the green iron project will leverage existing green hydrogen production and renewable energy as well as existing iron ore production at its Christmas Creek project for a US$50m green iron trial commercial plant.
Further highlighting why having a major company invested in hydrogen is so important, FMG has also fast-tracked the Pecem project in Brazil, Project Chui in Kenya and Holmaneset in Norway.
However, the planned Gibson Island green hydrogen and ammonia project in Queensland remains on the drawing board with more work required.
Micro hubs make a hell of a lot of sense
Got Gas is not in the habit of plugging or promoting companies; it prefers to call a spade a spade.
And Pure Hydrogen’s (ASX:PH2) revelation last week that it would embrace low-capex, green hydrogen micro-hubs to meet the refuelling needs of its customers makes perfect sense.
It is all too easy to be bedazzled by companies hawking their claims for large-scale hydrogen production facilities, but the sector faces two other equally massive issues.
First being where’s the demand beyond replacing hydrogen used for industrial processes or fed in small percentage into natural gas pipelines for consumer consumption, and second – how are you going to get the hydrogen to the customer in the first place?
Using existing gas pipelines is largely out as large concentrations of hydrogen can damage said pipelines thanks to a process known as hydrogen embrittlement, which happens when the gas penetrates into the metal causing a loss of ductility and tensile strength.
Needless to say that’s a bad thing.
Building pipelines designed specifically for transporting hydrogen is entirely possible, but costly as they would need to be laid anew.
Taking the route of natural gas, ie liquefaction, to enable overseas export or for distances that make pipelines unviable, is certainly possible but comes with its own set of problems.
For starters, hydrogen liquefies at a temperature of -253 degrees Celsius, way lower than the -162 degrees Celsius for natural gas.
This means that we require considerably more energy to both liquefy hydrogen and keep it there then we do for natural gas.
Further compounding this is that even when liquefied, hydrogen has lower energy density than liquefied natural gas (about 42% of LNG to be precise).
So all that effort still yields you less contained energy for the same volume.
Other options include converting hydrogen into ammonia, which has its attractions but again attracts the energy penalty needed for the conversion at both ends of the supply chain. And we haven’t gotten to the fact that like liquefaction, this adds to the infrastructure demands (aka cost).
Here’s where having micro-hubs capable of producing just enough hydrogen (with a buffer) to meet a customer’s needs comes into play.
By its very nature, green hydrogen actually lends itself very well to this concept.
All you need is a renewable power source – solar panels are likely the best option here in Australia, an electrolyser, a source of clean water, storage tanks and facilities to carry out refuelling.
Doing so also neatly sidesteps that troublesome need to transport the green gas.
Having such micro-hubs in place will more than likely help drive demand and potentially set the stage for bigger, better infrastructure to be built. Or they could just be expanded – either works.
Incidentally, micro-hubs might also just be the answer to meeting problem number one facing Toyota’s hydrogen ambitions as outlined earlier, but Got Gas still reckons that the battle between HFCEVs and BEVs for consumer vehicles has already been settled in favour of the latter.
At Stockhead we tell it like it is. While Pure Hydrogen is a Stockhead advertiser, it did not sponsor this article.
Related Topics
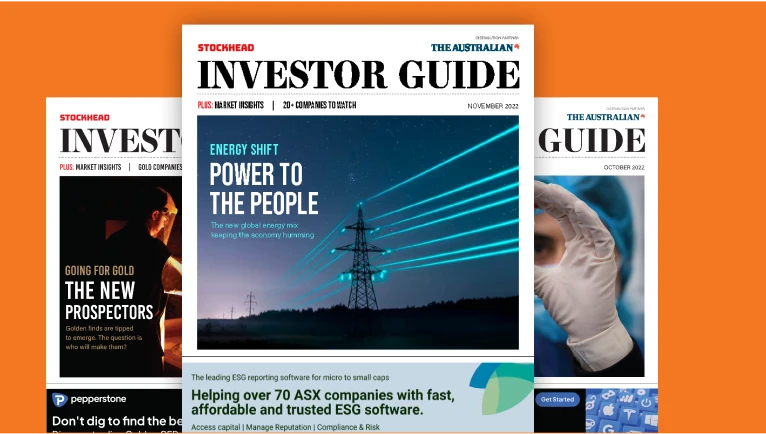
UNLOCK INSIGHTS
Discover the untold stories of emerging ASX stocks.
Daily news and expert analysis, it's free to subscribe.
By proceeding, you confirm you understand that we handle personal information in accordance with our Privacy Policy.