Aussie company Neometals is building a battery recycling plant… in Canada
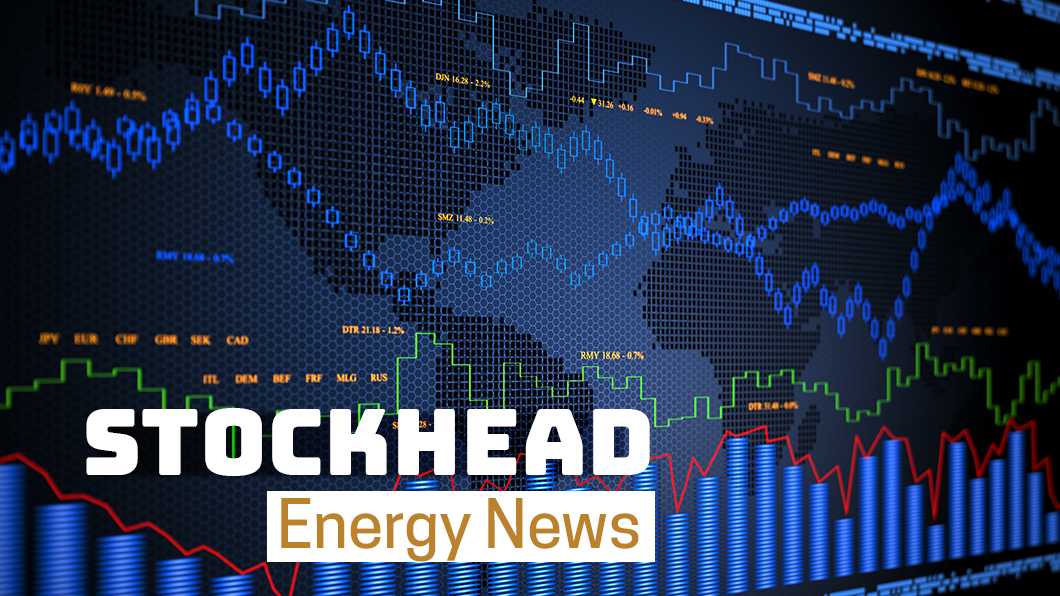
Pic: Vertigo3d / E+ via Getty Images
Yesterday, Perth-based battery tech company Neometals fired up its lithium-ion battery recycling pilot plant in Canada.
Neometals (ASX:NMT) says it has developed a profitable process that recovers 90 per cent of all raw battery materials, like cobalt, manganese, nickel and lithium from used batteries.
These are end-of-life or faulty batteries that would otherwise find their way into landfill or inefficient base metal recovery circuits, Neometals says.
Oh, Canada
Two recent reports have mapped out big plans for a local Australian EV manufacturing sector.
New industries, such as charging infrastructure manufacturing and installation, battery manufacturing, recycling, repurposing and related mining and processing activities, and EV research and development could emerge as growth sectors for the Australian economy, the government says.
So why is Neometals setting up shop in Canada? Are they friendlier than us?
Not at all, Neometals boss Chris Reed says.
Australia is doing “great job” fostering local battery metals R&D — it’s just that North America is much closer to Neometals’ target market.
“Anything that the Canadians can do, we can do down here as good, if not better,” Mr Reed told Stockhead.
“We do lots of R&D in Australia at CSIRO, Queensland University of Technology, … you name it.
“But this pilot plant is a showcase for potential partners — and Australia isn’t really a target market.”
It’s a business model that will initially focus on partnerships with auto and battery makers to recycle off-spec cells that fail QA/QC, and end-of-life returns.
Based in North America, the company is close to these target customers in the US, Europe and Asia.
This process involves shredding the old batteries (Stage 1) and a subsequent hydrometallurgical processing and refining stage to deliver high purity battery materials (Stage 2).
This pilot plant is intended to show that Neometals’ process can recycle a range of battery types from multiple sources, including consumer electronics, electric vehicles (EV), and stationary storage.
It will also produce product samples for prospective customers and provide essential data for a commercial-sized plant.
“The pilot will give the company product samples of the battery materials like cobalt sulfate, nickel sulfate, manganese sulfate, and lithium sulfate which we can give to potential buyers,” Mr Reed says.
“It will also give us data for the front-end engineering and design (FEED) phase on a 50 tonnes per day recycling plant.”
Recycling will be really important, hmmkay?
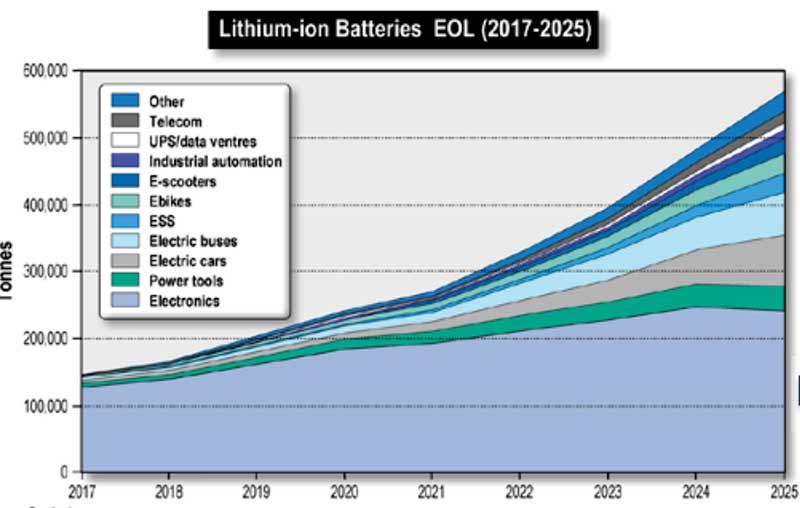
Efficient battery recycling is going to be crucial as the EV production volumes really accelerate.
Neometals has a pretty robust economic proposition on its hands as well, even as prices for battery metals come down from recent highs.
A 2017 scoping study estimated operating costs of about $US4.45/lb of contained cobalt based on a 10 tonne per day plant.
And as that is scaled up to 50 tonnes a day, Neometals reckons costs will come down even further.
“It’s a pretty robust process; [even] at current cobalt prices of $US15-$US16 a pound,” Mr Reed says.
“An LCO (lithium cobalt oxide) battery is about 20 per cent by weight cobalt.
“That’s about $US7000 per tonne contained cobalt in an LCO battery from consumer electronics.”
It took Neometals “quite a bit of time” to perfect the backend for treating the more complex, NMC (nickel manganese cobalt) EV batteries, Mr Reed says.
“But the volumes of car batteries that are being produced are increasing quickly and the numbers coming back [for recycling] are bigger than we had planned,” he says.
“One Tesla car has between 20,000 and 25,000 equivalent sized phone batteries.”
- Subscribe to our daily newsletter
- Bookmark this link for small cap news
- Join our small cap Facebook group
- Follow us on Facebook or Twitter
UNLOCK INSIGHTS
Discover the untold stories of emerging ASX stocks.
Daily news and expert analysis, it's free to subscribe.
By proceeding, you confirm you understand that we handle personal information in accordance with our Privacy Policy.